6060 results
Introduction to Solid Mechanics
- Coming soon
-
- Expected online publication date:
- June 2024
- Print publication:
- 01 November 2025
-
- Textbook
- Export citation
12 - Urbanization and Housing Infrastructure in Urban India
-
-
- Book:
- India Population Report
- Published online:
- 15 August 2023
- Print publication:
- 31 May 2024, pp 452-497
-
- Chapter
- Export citation
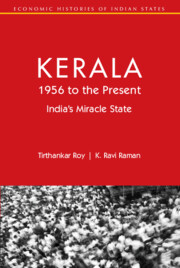
Kerala, 1956 to the Present
- India's Miracle State
- Coming soon
-
- Expected online publication date:
- May 2024
- Print publication:
- 31 July 2024
-
- Book
- Export citation
A granular examination of gender and racial disparities in federal procurement
-
- Journal:
- Data & Policy / Volume 6 / 2024
- Published online by Cambridge University Press:
- 19 April 2024, e25
-
- Article
-
- You have access
- Open access
- HTML
- Export citation
Turbulence induced by a swarm of rising bubbles from coarse-grained simulations
-
- Journal:
- Journal of Fluid Mechanics / Volume 984 / 10 April 2024
- Published online by Cambridge University Press:
- 12 April 2024, A68
-
- Article
- Export citation
106 Transforming Health Equity with an Innovative Social Determinants of Health Platform: Application of HOUSES Index to Colorectal Cancer Screening
- Part of
-
- Journal:
- Journal of Clinical and Translational Science / Volume 8 / Issue s1 / April 2024
- Published online by Cambridge University Press:
- 03 April 2024, p. 30
-
- Article
-
- You have access
- Open access
- Export citation
371 Pre-Clinical Models of Penetrating Brain Injury: Study Protocol for a Systematic Review
- Part of
-
- Journal:
- Journal of Clinical and Translational Science / Volume 8 / Issue s1 / April 2024
- Published online by Cambridge University Press:
- 03 April 2024, p. 112
-
- Article
-
- You have access
- Open access
- Export citation
Alteration of Clay Minerals and Zeolites in Hydrothermal Brines
-
- Journal:
- Clays and Clay Minerals / Volume 31 / Issue 5 / October 1983
- Published online by Cambridge University Press:
- 02 April 2024, pp. 383-391
-
- Article
- Export citation
Vanadium Chlorite from a Sandstone-Hosted Vanadium-Uranium Deposit, Henry Basin, Utah
-
- Journal:
- Clays and Clay Minerals / Volume 34 / Issue 4 / August 1986
- Published online by Cambridge University Press:
- 02 April 2024, pp. 488-495
-
- Article
- Export citation
Development of Layer Charge and Kinetics of Experimental Smectite Alteration
-
- Journal:
- Clays and Clay Minerals / Volume 33 / Issue 2 / April 1985
- Published online by Cambridge University Press:
- 02 April 2024, pp. 81-88
-
- Article
- Export citation
Cation-Exchange Properties of (Al + Na)-Substituted Synthetic Tobermorites
-
- Journal:
- Clays and Clay Minerals / Volume 35 / Issue 5 / October 1987
- Published online by Cambridge University Press:
- 02 April 2024, pp. 385-390
-
- Article
- Export citation
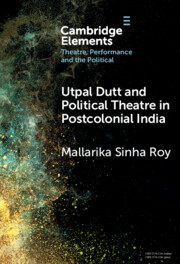
Utpal Dutt and Political Theatre in Postcolonial India
-
- Published online:
- 21 March 2024
- Print publication:
- 11 April 2024
-
- Element
- Export citation
Status of Sustainability Management Education in African MBA Programmes: A Web-based Research Approach
-
- Journal:
- Australian Journal of Environmental Education , First View
- Published online by Cambridge University Press:
- 18 March 2024, pp. 1-19
-
- Article
-
- You have access
- Open access
- HTML
- Export citation
Racial Feudalism
-
- Journal:
- Modern Intellectual History , First View
- Published online by Cambridge University Press:
- 13 March 2024, pp. 1-32
-
- Article
-
- You have access
- Open access
- HTML
- Export citation
Chronic constipation in people with intellectual disabilities in the community: cross-sectional study
-
- Journal:
- BJPsych Open / Volume 10 / Issue 2 / March 2024
- Published online by Cambridge University Press:
- 01 March 2024, e55
-
- Article
-
- You have access
- Open access
- HTML
- Export citation
Overcrowding in the Dispatching Centre During the COVID-19 Crisis: Are Medical Students a Resource?
-
- Journal:
- Disaster Medicine and Public Health Preparedness / Volume 18 / 2024
- Published online by Cambridge University Press:
- 28 February 2024, e38
-
- Article
- Export citation
Rehydration of Zn-Al Layered Double Hydroxides
-
- Journal:
- Clays and Clay Minerals / Volume 45 / Issue 1 / February 1997
- Published online by Cambridge University Press:
- 28 February 2024, pp. 92-98
-
- Article
- Export citation
Microfabric of Altered Ash Layers, ODP Leg 131, Nankai Trough
-
- Journal:
- Clays and Clay Minerals / Volume 42 / Issue 4 / August 1994
- Published online by Cambridge University Press:
- 28 February 2024, pp. 428-436
-
- Article
- Export citation
The merger of co-rotating vortices in dusty flows
-
- Journal:
- Journal of Fluid Mechanics / Volume 981 / 25 February 2024
- Published online by Cambridge University Press:
- 26 February 2024, A27
-
- Article
-
- You have access
- Open access
- HTML
- Export citation
Reclaiming Public Spaces in Post-pandemic India (Kolkata): Activist Theatre, Gender and a Resurgence of the Marginal
-
- Journal:
- Theatre Research International / Volume 49 / Issue 1 / March 2024
- Published online by Cambridge University Press:
- 26 February 2024, pp. 111-117
- Print publication:
- March 2024
-
- Article
- Export citation