How “Paint jetting” could help save our planet
September 16th 2021 marked the 34th anniversary of the Montreal Protocol, one of the most successful climate initiatives in United Nations history. Yet, despite its success in reducing the use of ozone-depleting chemicals, researchers are still finding new ways to reduce our reliance on volatile organic compounds.
Perhaps one of humanity’s greatest climate wins has been our handling of aerosol products. In 1987, 46 signatories in Montreal ratified a treaty designed to phase out the use of ozone-depleting hydrocarbons, which came into wide-spread use in the 1950’s and 1960’s as more and more products requiring solvents, propellants, and refrigerants came to market. In hindsight, the quickness with which the Montreal Protocol was ratified is staggering. In 1976, The National Research Council in the United States issued one of the very first reports confirming that these hydrocarbons could be reacting in the stratosphere, causing the loss of our ozone layer. Then in 1985, researchers from the British Antarctic Survey reported significant ozone loss above the South Pole consistent with the 1976 report. Several other studies followed finding similarly shocking results, ultimately leading to the signing of the most successful international climate agreement in UN history. In 2009 the Montreal Protocol became one of the first UN treaties to be universally ratified, having been signed by 196 countries and the European Union.
Before the Montreal Protocol, ozone-depleting hydrocarbons like chlorofluorocarbons (CFCs) and hydrofluorocarbons (HCFCs) were used in a variety of products, often for their high volatility and ability to reduce the viscosity of fluids like paint. These features enabled aerosol manufacturers to use CFCs as not only the solvent, but also the compressed propellant, which ejected the paint as an aerosol spray. Limiting the use of CFCs and HCFCs is a huge success, and the UN is now projecting that the ozone layer should return to pre-1980 levels by mid-century. But there are plenty of alternative compounds that have replaced them; many of which are dangerous in their own way. These alternatives may be safer for the ozone layer but are often toxic, flammable, carcinogenic, or release carbon dioxide when they are burned. Because of how useful aerosol products are, it’s unlikely volatile chemicals of this sort will ever be completely replaced, but new inventions could be leveraged in certain applications to help to reduce their impact.
In the automotive industry, spray-coating is used extensively despite several application-specific drawbacks. Besides the environmental harm of using volatile organic solvents to reduce the coating’s viscosity, spraying is inaccurate and requires masking the surfaces that need to stay coating-free. The inaccuracy of spraying creates significant waste, as much of the coating will not make it to the desired location. Inkjet printing is one currently available technology that could potentially be adapted for paints and coatings to achieve higher accuracy and reduce wasted ink, but it is difficult to implement with liquids that are particularly viscous, such as the paint used on vehicles.
Most inkjet printers rely on ejecting droplets by squeezing ink through a nozzle, often by applying a small voltage to a “piezoelectric”[TC5] crystal – a commonly used component in electronic devices that deforms with changes in voltage. This causes the crystal to flex, applying pressure to the attached reservoir and squirting out a precise amount of ink through the nozzle. However, when using thicker inks or paints there is a higher chance of clogging the ejection nozzle. As a result, wider nozzles would need to be used, limiting how small and precise the delivery of ink droplets can be. For this reason, inkjet printers will generally use inks with low viscosities which are comparable to olive oil or very thin motor oil. Unfortunately, many paints and coatings are far more viscous than these thin inks, bearing a greater resemblance to something like ketchup. However, researchers from the Tokyo University of Agriculture and Technology may have found an alternative to sprays that could work for thicker paints. In a paper recently published in FLOW, these researchers demonstrate a purely mechanical system that, in a sense, combines inkjet printing and shaking ketchup out of a glass bottle, all while eliminating the need for viscosity-thinning, volatile organic compounds. But, unlike ketchup, which can be difficult to get out of a bottle in a consistent manner, the technique shows that highly viscous paint can be shaken out of a reservoir while still maintaining a high degree of accuracy and control over the delivery of the ejected paint.
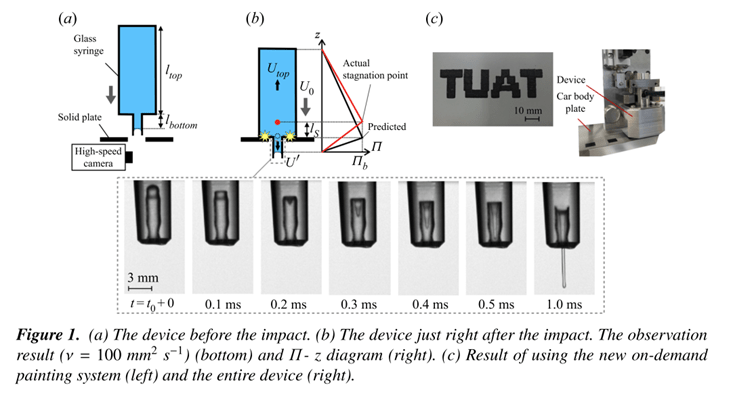
The device shown in Figure 1 is remarkably simple; the bulk of the machine being just a reservoir with a short narrow nozzle. To eject a droplet, the nozzle is essentially slammed against a solid plate and this causes a small jet of paint to escape the nozzle at velocities up to 30-times faster than the reservoir’s impact speed. To understand and harness this technique, the researchers considered the paint-jet production as a result of the pressure increase during the slamming action, and solved for how the liquid in the reservoir would flow according to a fluid dynamics model published in the Journal of Fluid Mechanics. The model helped identify how the relative sizes of the reservoir and nozzle, along with the impact speed, influence the paint jet. This information allowed the research team to build a computer-controlled painting device, demonstrated in Figure 1 c). Notably, the crisp lines spelling out the initials of Tokyo University of Agriculture and Technology in Figure 1 c) were made without masking the painting surface first and with little-to-no material waste. The whole process was demonstrated with commercially available automotive paint, without using a paint thinner, suggesting that a scaled-up version of this technique could be a good candidate for a low-cost alternative to spray-coating.
Applying spurts of paint is one application of this jetting phenomenon, but it may also find uses in medicine. Another interesting application uses this type of microjet to performing needle-free injections where tiny, high-speed volumes of liquid are made to pass through human tissue while causing minimal damage on their way in. Of course, it can be difficult to tell where new technologies will finally take hold, but as a paint delivery mechanism, this technique appears very promising. Scrutinizing even small-scale industrial processes can help in developing a more comprehensive shifts toward more efficient and/or climate-aware technologies. It will not eliminate our need for volatile organic solvents entirely, but every little bit counts.
In addition to publishing interdisciplinary and widely interesting research, FLOW is committed to making research accessible through articles like this. Be sure to follow Flow and the Journal of Fluid Mechanics on Twitter to stay up to date with the latest developments in the field and see what is featured next on the blog