A new technique for crafting optical components: easy, cheap, and fluid
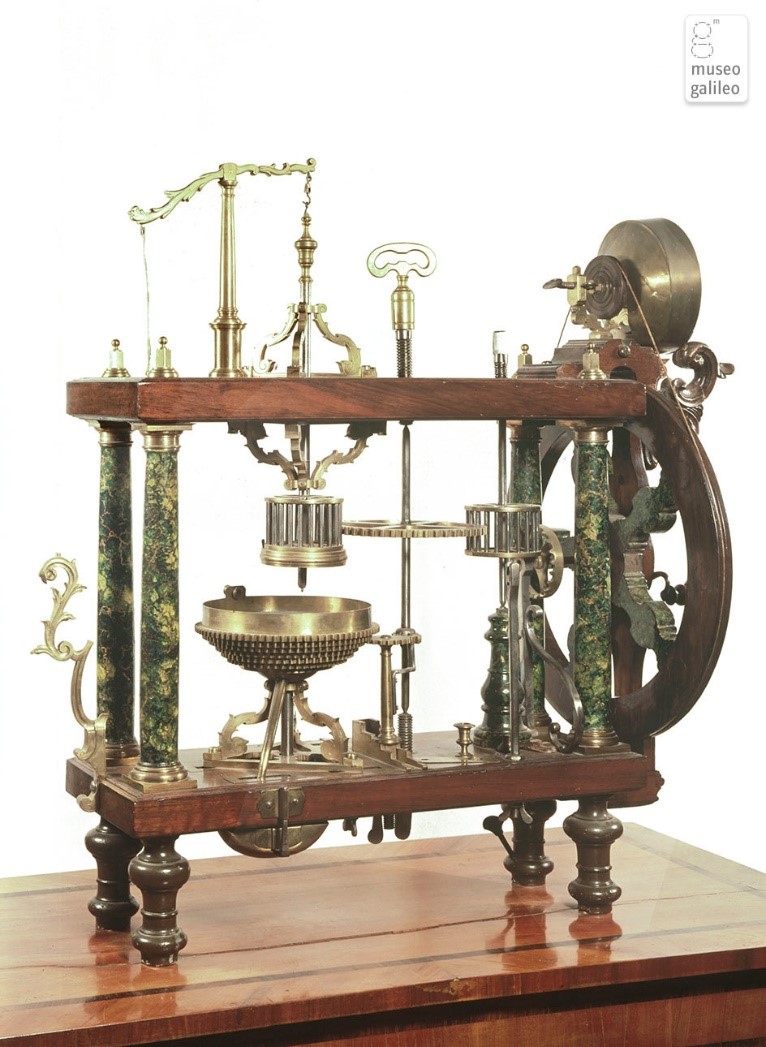
The device above might not look familiar, but the object it produces (or used to produce) probably would. Lens grinding – or shaping a lens by the removal of material – has been the method of choice for lens production for hundreds of years, and very little has changed in that time. Better, more precise tools and specialized coatings have helped improve the exactness and power of lenses, but lens makers still need to grind and polish their glass in much the same way as their ancient contemporaries did. It can be a slow, laborious process, and for this reason is often left to companies specializing in optics, but this can become costly and cause serious delays for labs and companies that need custom optical devices.
One possible solution might be to try to take advantage of rapid prototyping techniques like 3D printing – as has been seen in many other manufacturing processes – but unfortunately the level of detail required to make high-quality lenses puts this idea out of reach. However, there could be another way. In a recent paper published in FLOW, Valeri Frumkin and Moran Bercovici from the Israel Institute of Technology show that the physics that gives raindrops and bubbles their shape can also be used to make large, high-quality lenses quickly and cheaply. And we mean way faster and way cheaper…
In the absence of gravity or other forces, a volume of liquid will form a perfect sphere. This is because surface tension causes a fluid to minimize the amount of surface area it shares with the materials (like air or another fluid) it comes into contact with. Despite Bercovici’s lab being earthbound, there are ways of counteracting gravity, namely through buoyancy. If a volume of liquid is placed inside another liquid with matching density, the force of gravity is compensated for by buoyancy, and so a droplet of fluid will not be compelled to rise or fall. “[Gravity] basically flattens the lens, and you get a puddle and that’s not very useful from an optical perspective. So really the big deal here is cancelling or neutralizing the effect of gravity by going with this neutral buoyancy trick.”
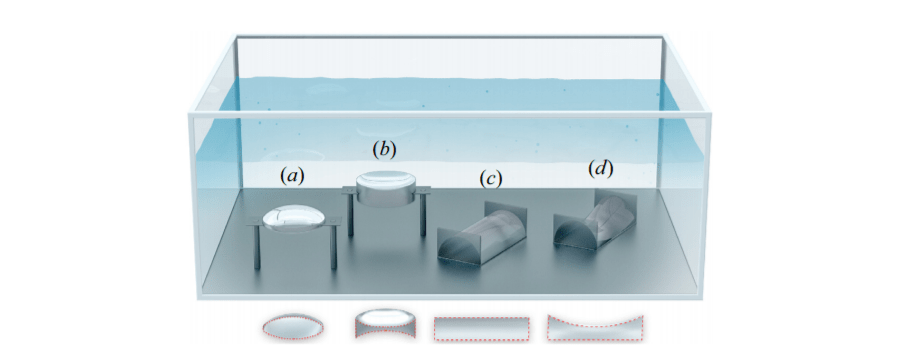
It is this principle that Frumkin and Bercovici use to shape their lenses. A polymer is first injected into a frame that is held below the surface of a liquid bath. The frame is a lot like a ‘bubble-wand’ one might use to blow soap bubbles as a child and depending on its shape and the volume of polymer injected, it can either form a curved surface inside the frame (b), or bulge out of it (a). At this point nature takes over and will create a smooth and glassy liquid lens to minimize the liquid’s surface area.
The exact shape of the lens (and thus its focal length, aperture, and magnification) can be customized by changing the density, surface tension, and volume of polymer injected into the suspending liquid. The most difficult step, however, comes at the end. Once surface tension and buoyancy finish shaping the lens, the researchers need the fluid to solidify.
This is done by “curing” the polymer with either UV light or by mixing it with a cross-linking agent and letting it rest. This, in a sense, “sets” the fluid into its final shape. The best part is that it can be done quickly – on the order of minutes. But the process is tricky. Transitioning from liquid to solid can cause many materials to change in volume, which can cause deformations in the final product as Frumkin explains “The biggest challenge we’re facing that has to do with the polymerization is the volumetric change. Usually polymers will shrink, and you have to account for the shrinkage when you design the component. You also want it to happen in a very uniform way.”
The researchers reduced the severity of this problem by using materials that exhibit smaller volume changes, but they admit there is still room for improvement. “We had a very rigorous selection process for polymers,” joked Frumkin. “We opened the drawer in the lab and took the first two polymers that were in there which were PDMS and an optical glue.”
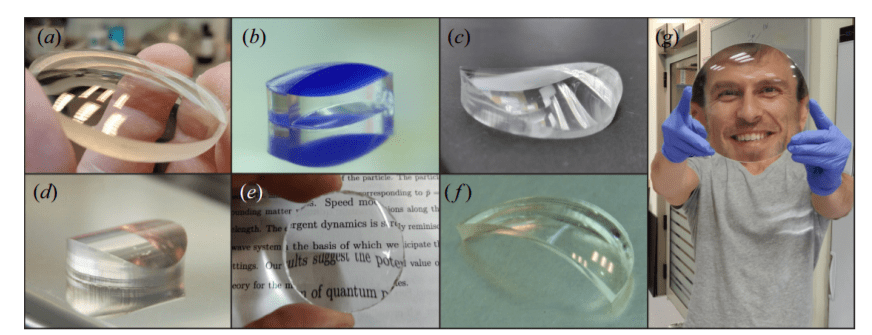
“Currently we have a superb material that my daughter found on AliExpress when she was looking for ‘slime’ [to play with]” says Bercovici. “There are a lot of polymers out there and we just bought a bunch of bottles of different resins that people typically use for hobbies, like to make jewellery. We tried a bunch of them having no idea of what was in there, and we found a couple that were just amazing with their optical properties, their low shrinkage, uniformity… and they look great!” Of course, the eventual plan is not to use off the shelf mystery polymers, and in fact it would appear there could be an emerging, application-driven interest in designing new polymers specifically for this job.
Despite the apparent success of the ‘neutral buoyancy’ approach, the team believe they may have a way of both simplifying the technique, while also avoiding the need for solidifying the polymer lens in the first place. Building these lenses in the microgravity of Earth’s orbit would be another way of creating the right atmosphere for crafting a liquid lens, and in fact, this is exactly what Frumkin and Bercovici intend to do.
“First of all, in microgravity, since there is no immersion liquid, there really is no reason to solidify the lens, so you can keep it in liquid form,” says Frumkin. “So, you could imagine having a huge liquid lens, much larger than anything currently achievable by existing technologies, and you can actually modify the focal length of these lenses in real time because you can inject or aspirate liquid into or out of the lens. Also, these lenses are not susceptible to space debris since, if you have space junk flying through the lens, if it’s a liquid lens, it just goes through.”
The team will soon be testing their technique in microgravity by taking it on a series of parabolic flights. Each parabola their aircraft makes will give them less than 20 seconds of microgravity in which they will need to inject the lens, then image through it. The follow up to this experiment will take place on the International Space Station (ISS) in February of 2022 as part of the Axiom AX1 mission (the first fully private mission to the ISS). On this mission, liquid lenses will be fabricated in space, polymerized, and then brought back to Earth.
Bercovici believes the long-term goal for space-based hardware is self-sufficiency “If something breaks, you can’t just get a delivery from Earth.” But another aspect to consider is how these expensive devices get into space to begin with. “[The James Webb Telescope] has a crazy folding mechanism to fit it to the frame of the launcher, and that is a 6.5 meter diameter space telescope. Basically, we want to launch a bottle and a syringe, and inject the telescope in space. You overcome a lot of the launch limitations in terms of the forces acting on the telescope during the launch, and of course you can shape the liquid in any way you want.” If this idea works, Bercovici and Frumkin believe we could see telescopes on the scale of tens or even hundreds of meters in size, which could help in imaging planets outside of our solar system.
All of this may sound out of this world, but the technique also shows promise as a very quick and inexpensive way to make prescription eyewear and other every day, terrestrial tools, in places that may not have easy access to lens fabrication equipment. Really, the physics behind their technique is simple enough to demonstrate in your own kitchen at home.
“What you need are three materials,” explained Frumkin. “The first material is for the lens, the second material is for your immersion liquid, and they have to be immiscible with each other, like oil and water. Then you need something to change the density of the fluids.” This can be easily achieved with sugar or salt which can be added to increase the density of a fluid, or by adding alcohol to reduce it. When you find the right balance, a drop of one liquid will take on the shape of an otherworldly, stationary sphere suspended in the other liquid. Frumkin adds, “we are trying now to design kits that you can just take to school and demonstrate so the kids can do the experiment too!”
This exciting research is just one of the articles published in the first ever issue of Flow by Cambridge University Press. You can find full, open-access articles online here. Also, be sure to follow Flow and the Journal of Fluid Mechanics on Twitter to stay up to date with the latest developments in the field.