1. Introduction
The set of technological advances brought about by digitalisation have enabled radical changes in products that have become ‘smart’, in processes that have abandoned their physical nature to become ‘digital’, and in services that are consequently enabled by such smart products and digital processes (Cantamessa et al. Reference Cantamessa, Montagna, Altavilla and Casagrande-Seretti2020; Verhoef et al. Reference Verhoef, Broekhuizen, Bart, Bhattacharya, Dong, Fabian and Haenlein2021). These changes are often accompanied by disruption in business models, industries and value chains, whereby ‘servitisation’ has become a pervasive phenomenon and ‘digital’ corporations have now risen to the top of the market capitalisation league tables.
Since digital technology has led to changes in many industries throughout the world, it is reasonable to presume that innovation processes, design and product development have consequently been affected.
Digitalisation, in particular, has been having consequences on designers, both individually and when they are part of a team, thus leading to changes in design processes (Porter & Heppelmann Reference Porter and Heppelmann2014; Bstieler et al. Reference Bstieler, Gruen, Akdeniz, Brick, Du, Guo, Khanlari, McIllroy, O’Hern and Yalcinkaya2018; Cantamessa et al. Reference Cantamessa, Montagna, Altavilla and Casagrande-Seretti2020; Jiao et al. Reference Jiao, Luo, Malmqvist and Summers2022). Moreover, digitalisation has induced a shift in the use of digital product data and also extended the types of data that can be used. Data, in fact, can be derived from both customers/users (‘demand-side data’) and the production/distribution chain (‘supply-side data’) (Cantamessa et al. Reference Cantamessa, Montagna, Altavilla and Casagrande-Seretti2020), or they can be specifically related to the features, performances or operating processes of a product, or to all such aspects throughout the product lifecycle (Wellsandt et al. Reference Wellsandt, Hribernik and Thoben2015). Data may also be generated by different sources (‘sensor-collected, user-generated, expert-generated and internal/external documents’; Lee & Ahmed-Kristensen Reference Lee and Ahmed-Kristensen2023) and acquired through various channels (Zero-, First-, Second-, Third-party data; Khatibloo et al. Reference Khatibloo, Sridharan, Stanhope, Liu, Joyce and Turley2017). Among others, a value chain perspective is deemed appropriate to reveal the organisational and operational consequences of digitalisation (Cantamessa et al. Reference Cantamessa, Montagna, Altavilla and Casagrande-Seretti2020), especially since a distinction into demand-side and supply-side is useful in analysing technological paradigm transitions like the digital one. ‘Any technological paradigm (in fact) ideally is fostered by supply and demand-side elements’ (Dosi Reference Dosi1982; Cantamessa et al. Reference Cantamessa, Montagna, Altavilla and Casagrande-Seretti2020).
The ubiquity of data has correspondingly been enabling advancements in data analytics, which, in turn, aid design decision-making processes (Van Horn et al. Reference Van Horn, Olewnik and Lewis2012), allow product innovation opportunities, but also imply challenges and operational changes in product development. However, these process changes have not yet been accompanied by any theoretically-framed or structured support, although proposals of practices to guide product design processes within data-driven innovation environments are emerging (e.g., Cao et al. Reference Cao, Sun, Tan, Zhang and Liu2021; Liu et al. Reference Liu, Wang and Wang2022).
Therefore, the aim of this paper has been to determine what data flows characterise data-driven innovation processes. The objective has been to validate, at least partially, the challenges and concerns resulting from the literature, which can be associated with the data flows and can be discussed in light of the engineering design resources currently available to designers. The paper considers the definition of ‘challenge’, according to the Oxford dictionary, as a ‘new or demanding task’ that could test the current abilities and skills of designers, and ‘concern’ as an issue brought about by digitalisation that causes ‘shared solicitous regard, anxiety or worry’ in designers.
The paper builds upon the relational model of Cantamessa et al. (Reference Cantamessa, Montagna, Altavilla and Casagrande-Seretti2020) and its following extensions –specifically Kim Reference Kim2022 – which depict the new paradigm of data-driven design, and attempts to overcome their limitations. It does so through the analysis of 36 case studies of data-driven innovation processes, by considering a greater number of involved actors and discussing engineering design practices in light of the challenges and concerns that have emerged. As such, the paper can be seen as an extension of the works of Cantamessa et al. (Reference Cantamessa, Montagna, Altavilla and Casagrande-Seretti2020) and Kim (Reference Kim2022), with the goal of validating and complementing those models.
The ultimate objective of the concluding discourse about engineering design practices is to identify relevant topics emerging from this knowledge domain that can support data-driven innovation and, at the same time, anticipate directions of further development for engineering design research.
The paper is structured as follows: first, the Literature Review outlines the challenges and concerns that arise from the usage of data by distinguishing the data type and roles; this section is followed by the identification of the gap in the literature and a reflection on the original contribution of the paper. The Methodology section then presents and briefly describes the analysed companies. Finally, the Results and Discussion are illustrated and followed by possible Implications and Conclusions.
2. Literature review
The ‘Digitalisation’ of product and process data has been characterising the evolution of product development processes for more than four decades. Since early digitalisation processes, product/process information migrated to digital models, which allowed product information to be conveniently generated and stored, and then to shift to ‘virtual product models’. However, such a ‘fast forward’, which involved the substitution of hand drawings with CAD models, the integration of simulations and experimental data through Product Data Management (PDM) tools and the transition to Product Lifecycle Management (PLM) systems, has led to the progressive broadening of product digital data, from the micro-perspective of an individual designer to the multiple dimensions of enterprise operations and product life stages (Terzi et al. Reference Terzi, Bouras, Dutta, Garetti and Kiritsis2010).
Although product development was able to boast well-established practices of using digital data or integration processes with external data, digitisation was beginning to completely change the environment in which product development took place and, consequently, the role data could play as digital-based antecedents of innovation (Agostini et al. Reference Agostini, Galati and Gastaldi2020; Luo Reference Luo2023). Hence, the purposes of and the roles that data can play in aiding design and development activities are overviewed hereafter, together with a discussion about how data forces design and development to integrate with other business processes to enable innovation.
2.1. Customers’ or users’ data as sources of needs, preferences and behaviour
Amazon’s story highlights the power that digital data processes provide with respect to traditional ones (Moore & Tambini Reference Moore and Tambini2018). Walmart was gathering more than 2.5 petabytes of data every hour from its customers’ transactions already a decade ago (McAfee et al. Reference McAfee, Brynjolfsson, Davenport, Patil and Barton2012), and General Electric has become the leading manufacturing industry in managing customers’ data and designing service offerings (Davenport & Dyché Reference Davenport and Dyché2013).
Customers’ data are mainly collected by recording the purchasing behaviour of customers through the observation of individual choices (Lesser et al. Reference Lesser, Mundel and Wiecha2000), by investigating customers’ preferences (e.g., Stone & Choi Reference Stone and Choi2013; Jin et al. Reference Jin, Liu, Ji and Liu2016; Ng & Law Reference Ng and Law2020) and sometimes by analysing customers’ complaints and claims (e.g., Park & Lee Reference Park and Lee2011). It is apparent that these elements can guide product development in defining and choosing design alternatives (e.g., Park & Lee Reference Park and Lee2011; Gangurde & Akarte Reference Gangurde and Akarte2013), even if they change over time and, therefore, need to be continuously tracked. In this sense, customers’ reviews (e.g., Tucker & Kim Reference Tucker and Kim2011) or social media mining (e.g., Jeong et al. Reference Jeong, Yoon and Lee2019; Choi et al. Reference Choi, Oh, Yoon, Lee and Coh2020) are more able to address such dynamic capturing requirements.
Users’ data are gathered in parallel from people who use products and services or from users’ stakeholders (Cantamessa et al. Reference Cantamessa, Cascini and Montagna2012, Reference Cantamessa, Montagna and Cascini2016). In the same way as Facebook or LinkedIn collect data to suggest new personal contacts, Netflix continuously adapts its content offer according to individual daily choices of fruition. Nowadays, this usually occurs in digital services, but it is increasingly happening for products since designers integrate users’ data with product ones (Ferguson et al. Reference Ferguson, Greene, Repetti, Lewis and Behdad2015) or because smart products are able to provide data about users or their usage during use (Wang et al. Reference Wang, Chen, Zheng, Li and Khoo2019). Smart speakers, such as Alexa, pick up conversations, and Tesla collects more data than most car companies, that is, data that spans from a vehicle’s location and a car’s settings to short video clips from the car’s external cameras.
Users’ data also allow the users’ profiles (users’ psychological and social characteristics, physical and sensory characteristics, demographics, ISO 20282-1 section 7, 2006), behaviour, needs and preferences to be detected, and this leads to the product features that are explicitly linked to the users’ experiences being recognised (Timoshenko & Hauser Reference Timoshenko and Hauser2019). Again, users’ data are sometimes gathered from the field, even though perhaps with more design-oriented purposes (e.g., Lewis & van Horn Reference Lewis and van Horn2013; Lee et al. Reference Lee, Yang and Chen2017): about the users’ profiles (Yang et al. Reference Yang, Liu, Liang and Tang2019), about the most essential requirements (e.g., Li et al. Reference Li, Nahar and Fung2013; Jiao & Yang Reference Jiao and Yang2019) or about the affordance elements (Hou et al. Reference Hou, Yannou, Leroy and Poirson2019). Sometimes, they are collected from sensor data or product usage logs to detect the users’ profiles, behaviour or real-time interactions (e.g., Klein et al. Reference Klein, van der Vegte, Hribernik and Klaus-Dieter2019; Voet et al. Reference Voet, Altenhof, Ellerich, Schmitt and Linke2019). Social media help identify the users’ needs or preferences (Wellsandt et al. Reference Wellsandt, Hribernik and Thoben2015), and identify those stakeholders that could affect the modes of product use (Rathore et al. Reference Rathore, Das and Ilavarasan2018) or the lead users (Tuarob & Tucker Reference Tuarob and Tucker2014).
It is well known that demand-side data allows companies not only to have a real, and not simply estimated, understanding of mission profiles but also to continuously adapt to market stimuli. This adaptation might consist of newly added functions, identified through the analysis of data generated by already launched products, or real-time adjustment of the offering to address the evolving customers’ needs or self-customised products (Porter & Heppelmann Reference Porter and Heppelmann2014).
However, this speed of adaptation is far from being taken for granted and represents a challenge that still has to be solved for designers (Challenge 1, in the following, CH1). Moreover, it calls for new analysis methods and leads to operational, managerial and organisational changes in design and development processes.
2.1.1. Contextual data and the role of complementary goods in determining environmental, economic and socio-cultural conditions
Not only are users a source of information, but also the usage context can be referred to. The usage context of a product represents ‘all aspects that describe the context of product use that vary under different use conditions and that affect product performance and consumers’ preferences for the product attributes’ (He et al. Reference He, Chen, Hoyle and Yannou2012). The context of use is embodied by environmental or external/boundary conditions, including both physical and social aspects, the main usage goal(s) and other related equipment (ISO 20282-1 2006).
While marketing studies on environmental factors that influence adoption/purchasing are more traditional (Kotler Reference Kotler2000), those on the determination of usage are novel and are strictly due to the possibility of collecting real-time data from smart/digital systems (Sestino & De Mauro Reference Sestino and De Mauro2021). Wang et al. (Reference Wang, Chen, Zheng, Li and Khoo2019), for instance, investigated various contextual data (e.g., raining or not, wind speed, etc.; ISO 20282-1 section 6.3, 2006) associated with the use conditions of smart bicycles (e.g., riding time), while Martí Bigorra and Isaksson (Reference Martí Bigorra and Isaksson2017) associated environmental conditions with the car owners’ driving styles.
Producers also relate such working context/external conditions with other data about products to derive insights into the performances/behaviour of products in relation to their main goal(s) (ISO 20282-1 section 6.1, 2006; Von Stietencron et al. Reference Von Stietencron, Hribernik, Røstad, Henriksen and Thoben2017; Bertoni et al. Reference Bertoni, Larsson, Larsson and Elfsberg2017). Martí Bigorra and Isaksson (Reference Martí Bigorra and Isaksson2017), for instance, included other factors that they considered beneficial for technical design analysis in their study, such as the precondition of a car before starting, which they associated with engine braking, smooth operation, etc.
Apart from working on environmental/external conditions, the influence that socio-cultural settings could have on the form and usage of a product, as an immaterial factor of a user’s behavioural experience and interpersonal interaction (ISO 20282-1 section 6.4, 2006), has been investigated for decades (Ram & Jung Reference Ram and Jung1990). New means for gathering data can support this practice. Hou et al. (Reference Hou, Yannou, Leroy and Poirson2019), for instance, adopted online reviews to detect in what conditions customers use/interact/perceive products and how these affect product affordances.
Finally, complementary assets also play an important role in determining contextual data (ISO 20282-1 section 6.2, 2006), especially when an architecture design assumes more strategic implications since they are enablers of adoption and affect the technological paradigms (Montagna & Cantamessa Reference Montagna and Cantamessa2019; Burton & Galvin Reference Burton and Galvin2020). These data often include the interaction of the system with complementary components, especially when such an interaction occurs through the real-time exchange of functional data.
Again, real-time data need to be collected, albeit about all the implications the product has for the outside. In order to ensure these data become readily usable for the definition of functional changes or design parameters, the procedures of design and development processes need to change (CH2).
2.1.2. Product usage and operational data used to analyse product performance
Product data have traditionally been investigated to analyse a system’s performance, monitor failures and optimise efficiency. The emerging difference is that the analysis of data can be conducted in real-time, on data collected either directly from embedded sensors (for instance, spin rate and load weight, which allow a washing machine’s bearing load to be calculated during washings; Klein et al. Reference Klein, van der Vegte, Hribernik and Klaus-Dieter2019), or from data that are ‘around’ the product, in order to provide insights into such a product. Tesla represents an emblematic case: the company was able to adapt the functional parameters of the suspensions of their cars without the car owners having to go to a maintenance station to do so (Muller Reference Muller2019). Suspension damping can, in fact, be adjusted in real time on the basis of the driving preferences, specific driving locations or the encountered road conditions. Similarly, smart irrigation systems (e.g., Irriga-Smart; Swamp, Togneri et al. Reference Togneri, Kamienski, Dantas, Prati, Toscano, Soininen and Cinotti2019) plan different irrigation operations according to the data received from weather stations or on the basis of different culture development needs and soil characteristics.
Field data from customers (e.g., Akinluyi et al. Reference Akinluyi, Ison and Clarkson2014; Joung et al. Reference Joung, Jung, Ko and Kim2019), customers’ services (e.g., Bandaru et al. Reference Bandaru, Gaur, Deb, Khare, Chougule and Bandyopadhyay2015) and warranties (e.g., Bueno & Borsato Reference Bueno, Borsato, Chou, Stjepandic, Xu, Cha and Curran2014; Moudoub et al. Reference Moudoub, Delaux and Hami2018) are just a few examples of other usage data that can be used to aid designers in envisioning the failures, reliability and performance degradation of products, as well as in monitoring failure modes and detecting failure patterns. Similarly, reviews and social media data can help in the investigation of those product features that are debated more among people when they are commenting on their experience and the reasons why a certain product performs better/worse than others (e.g., Zhang et al. Reference Zhang, Rao and Feng2018; Kim & Noh Reference Kim and Noh2019).
The previously cited typologies of data can be used to investigate specific product features or components, especially when failure modes can be explicitly associated with failure-prone elements (Tseng et al. Reference Tseng, Hsu and Lin2016; Ma et al. Reference Ma, Chul, Lyu and Xue2017; Pal et al. Reference Panchal, Fuge, Liu, Missoum and Tucker2019). In other cases, they can allow comparative analysis to be conducted among performance indicators (Ma & Kim Reference Ma and Kim2016; Mikulec et al. Reference Mikulec, Felke and Bangale2017) or provide indications on product industrialisation (Alkahtani et al. Reference Alkahtani, Choudhary, De and Harding2019).
Users’ and usage data can also be considered to investigate the performance and functional improvements of a product, as well as how usage affects a product’s lifecycle. This can lead to suggestions for design changes (e.g., Shin et al. Reference Shin, Kiritsis and Xirouchakis2015b) or even for conceiving product family design variants (e.g., Sotos et al. Reference Sotos, Okudan Kremer and Akman2014). Again, in this case, data can be derived from embedded sensors (e.g., Klein et al. Reference Klein, van der Vegte, Hribernik and Klaus-Dieter2019; Voet et al. Reference Voet, Altenhof, Ellerich, Schmitt and Linke2019), usage field data (e.g., Shin et al. Reference Shin, Jun, Catteneo, Kiritsis and Xirouchakis2015a) and warranty data (e.g., Dai et al. Reference Dai, He, Liu, Yang and He2017).
In turn, the real-time collection of operational data could lead to immediate functional adjustments of the design parameters, but this challenge (CH3), although more advanced in designer practice, still partially needs to be addressed, especially considering its generalisation to all industrial sectors.
2.2. Supply-side data used to identify production/distribution requirements and industrialisation alternatives
Companies also collect valuable data from their manufacturing environments, such as production machinery, supply chain management systems, etc. (Ghobakhloo Reference Ghobakhloo2019), often using systemic approaches (Mahmood & Montagna Reference Mahmood and Montagna2013). In these cases, data are often analysed by focusing on cost and efficiency issues (Jenab et al. Reference Jenab2019) or by addressing sustainability (Li et al. Reference Li, Wang, Chen and Zheng2021). However, they sometimes lead to broader benefits when this information is fed early to product development (Schuh et al. Reference Schuh, Rudolf and Riesener2016; Tao et al. Reference Tao2018). For instance, Tesla Model 3 proved to be particularly critical during the assembly phase, since many of its weld points and rivets were not suitable for heavy production automation (Welch Reference Welch2018). Data obtained from the manufacturing sector stimulated the definition of alternative product architectures in view of the consequences in the assembly phase.
Maintenance processes or the prototyping and testing phases of development processes are obviously valuable sources of information. These data are used more traditionally (e.g., Product re-engineering) and are easier to imagine, in part due to the PLM systems usually implemented in companies which are accustomed to exploiting data from maintenance, e.g., from MRO (Maintenance, Repair and Operations) reports. Again, what is different is the immediate use of data. Field data on maintenance, for instance, can be used to determine changes in design parameters (e.g., material, functional constraints, Abramovici et al. Reference Abramovici, Gebus, Göbel and Savarino2017) or used more widely on entire components (Soleimani et al. Reference Soleimani, Pourgol-Mohammad, Rostami and Ghanbari2014) with the purpose of reducing the probability of failure.
Similarly, data pertaining to logistics and the supply chain can affect the design of a product (Manohar & Ishii Reference Manohar and Ishii2008): supply chain metrics, in fact, which were originally aimed at measuring the performance for customers, have a huge impact on the social and environmental sustainability aspects of the product itself, but also affect the material procurement and transportation constraints that define specific functional and shape requirements.
Supply-side data represent the traditionally most applied application, although real-time collection poses the same concerns as the other data analysis sources and with respect to the operational/managerial/organisational changes induced for design and product development (CH4).
2.3. New sources of data call for design analytics to support design decisions
Apart from the increased computational capabilities of companies, the ubiquity of data has enabled the creation and advancement of a new field, which is known as design analytics (Van Horn et al. Reference Van Horn, Olewnik and Lewis2012). Design Analytics embodies a set of practices and tools that support the transformation of design-related data to make them suitable for aiding design decision-making processes (Cotter Reference Cotter2014; Chiarello et al. Reference Chiarello, Belingheri and Fantoni2021).
In general, data mining techniques (cluster analysis, conjoint analysis, etc.), optimisation algorithms, neural networks and machine learning are relatively well-established and widely applied to design problems (e.g. Liao Reference Liao2010; Elgendy & Elragal Reference Elgendy and Elragal2016; Tan et al. Reference Tan, Steinbach, Karpatne and Kumar2019). The former are mainly used to suggest requirements from data patterns or to determine the optimal settings of design attributes; the latter are instead primarily applied for leveraging decisions on previous design cases or to provide designers with relevant insights into the reasons behind the generated predictions. Machine learning (mainly classified as supervised and unsupervised algorithms) is used for both descriptive and predictive purposes (for a review, see Kotsiantis et al. Reference Kotsiantis, Zaharakis and Pintelas2007; Leskovec et al. Reference Leskovec, Rajaraman and Ullman2020).
There are many application contexts of such tools/techniques along with the different phases of product development. Cluster analysis, for instance, has been employed for descriptive purposes during the planning phase for product positioning purposes (Tao et al. Reference Tao2018) and within requirement elicitation (Zhang et al. Reference Zhang, Kwon, Kramer, Kim and Agogino2017). Conjoint analysis has instead been used to define customers’ preferences and suggest the possible functions and performances of a new design solution (Song & Kusiak Reference Song and Kusiak2009). Finally, the multiple response surfaces methodology (Jun & Suh Reference Jun and Suh2008), ordinal logistical regression (Demirtas et al. Reference Demirtas, Anagun and Koksal2009) and genetic algorithms (Hsiao & Tsai Reference Hsiao and Tsai2005) have been used, for instance, to determine the optimal settings of design attributes to maximise customers’ satisfaction. Case-based reasoning, data-driven design-by-analogy and neural network approaches have been used extensively during idea generation, either to leverage decisions of previous design cases (e.g., Hu et al. Reference Hu, Ma, Feng and Peng2017) and analogical reasoning (Jiang et al. Reference Jiang, Hu, Wood and Luo2021) or to simulate design alternatives concerning specific performance parameters (e.g., Dering & Tucker Reference Dering and Tucker2017). Optimisation tools have mainly been employed for predictive purposes during the design phase of the details. In this case, the aim is to foresee the impact of a design change at the subsystem level on the overall performance of a system (e.g., Yao et al. Reference Yao, Moon and Bi2017) or of design optimisation (Quintana-Amate et al. Reference Quintana-Amate2015). Finally, data-driven computational tools can support problem-exploration practices (Obieke et al. Reference Obieke, Milisavljevic-Syed and Han2021) and information retrieval (Shi et al. Reference Shi, Chen, Han and Childs2017; Han et al. Reference Han, Sarica, Shi and Luo2021) along the whole design process.
However, the choice of using data to aid design decisions introduces certain technical, operational and managerial concerns and consequences, all of which will be discussed in the following.
2.4. The resulting concerns (CN) induced by data-driven design in product development
The aforementioned technical concerns specifically refer to data analysis techniques, the operational concerns refer to the purpose of using data, while the managerial/organisational concerns refer to the interactions of design teams during the innovation and development processes inside a company.
Technical concerns arise since data analysis tools are contextual to the phase of product development in which they should be applied (Concern 1, in the following, CN1) (Van Horn et al. Reference Van Horn, Olewnik and Lewis2012; Bstieler et al. Reference Bstieler, Gruen, Akdeniz, Brick, Du, Guo, Khanlari, McIllroy, O’Hern and Yalcinkaya2018; Altavilla & Montagna Reference Altavilla and Montagna2019). Algorithms are specific to the context and application for which they were developed and cannot be applied independently for any purpose. Moreover, the ability of algorithms to automate the learning process has experienced a lack of implementation during the different design and development phases (CN2) (Fisher et al. Reference Fisher, Pazzani and Langley2014).
Three operational concerns emerge from the operational point of view. First, the modalities of the identification of the customer segments whose needs have to be addressed should be entirely changed for two reasons. On the one hand, customisation/personalisation leads to each customer being considered as a ‘segment-of-one’ (Canhoto et al. Reference Canhoto, Clark and Fennemore2013), whose needs are different from the ‘standard’ ones (Chen et al. Reference Chen and Storey2012; Ma & Kim Reference Ma and Kim2016); on the other hand, companies are increasingly turning towards continuous/real-time interactions with customers and designers and therefore must keep abreast with the evolving needs not only of those who have already adopted such interactions but also of those who will adopt them (Roblek et al. Reference Roblek, Meško and Krapež2016).
Therefore, the traditional separation between ex-ante product development and ex-post product use no longer exists, and companies experience almost simultaneous elicitation and satisfaction of the customers’ needs together with the validation of the corresponding product/service performance for each product development iteration (CN3) (Montagna & Cantamessa Reference Montagna and Cantamessa2019).
Moreover, since new needs are collected after commercial deployment and because of digital technology re-programmability, the possibility of derivative innovations emerges (Yoo et al. Reference Yoo, Boland, Lyytinen and and Majchrzak2012). More in general, designers discover implications that were not anticipated during the initial design process (CN4) (Gawer Reference Gawer2010), new features that were initially not conceived and therefore new functions and behaviour to be designed (Van Horn & Lewis Reference Van Horn and Lewis2015; Bstieler et al. Reference Bstieler, Gruen, Akdeniz, Brick, Du, Guo, Khanlari, McIllroy, O’Hern and Yalcinkaya2018; Wang et al. Reference Wang, Sha, Huang, Contractor, Fu and Chen2018). This transformation calls for the integration of information from different domains, such as marketing, design, manufacturing and after-sales services (Schuh et al. Reference Schuh, Rozenfeld, Assmus and Zancul2008; Li et al. Reference Li, Roy and Saltz2019), and new competencies in data analysis (De Mauro et al. Reference De Mauro, Greco, Grimaldi and Ritala2018). Furthermore, the capability of managing such diversity in extensive volumes of data (Li et al. Reference Li, Tao, Cheng and Zhao2015; Trunzer et al. Reference Trunzer, Calà, Leitão, Gepp, Kinghorst, Lüder, Schauerte, Reifferscheid and Vogel-Heuser2019) has become essential (CN5) since virtual prototyping, digitalisation or simply collection from diverse data sources generate various data formats, as has the requirement of making the use of such data volume effective (Zhan et al. Reference Zhan, Tan, Li and Tse2018).
Apart from operational processes, all these elements also have managerial consequences on the interactions that design teams have externally and on other functions and departments of the firm (e.g., Bstieler et al. Reference Bstieler, Gruen, Akdeniz, Brick, Du, Guo, Khanlari, McIllroy, O’Hern and Yalcinkaya2018; Agostini et al. Reference Agostini, Galati and Gastaldi2020), as well as on the product development process itself (Cantamessa et al. Reference Cantamessa, Montagna, Altavilla and Casagrande-Seretti2020).
First, it becomes impossible – but also irrelevant – to develop a reliable and complete set of product/service specifications (CN6) (Gunasekaran et al. Reference Gunasekaran, Subramanian and Ngai2019). Designers have to design an initial product version, which is then used as a basis for further product improvements/extensions. Subsequent iterations lead to iterative validation steps, and it is possible to wonder who should be in charge of deciding on these iterations, that is, designers, marketing people or data analysts (Song Reference Song2017). This, in turn, can lead to a reissuing (but also an amplification) of the problems posed by concurrent engineering practices (Krishnan et al. Reference Krishnan, Eppinger and Whitney1997), as well as reflections on the applicability of Agile principles (Ahmed-Kristensen & Daalhuizen Reference Ahmed-Kristensen and Daalhuizen2015). Moreover, without a given or fixed set of specifications, producers cannot draft any legal documents, and certification processes should be revised coherently (Magnusson & Lakemond Reference Magnusson and Lakemond2017; Song Reference Song2017).
Second, design modularity and platforms become key enablers (Porter & Heppelmann Reference Porter and Heppelmann2014; Rossit et al. Reference Rossit, Tohmé and Frutos2019) since they enable customisation/personalisation (Mourtzis & Doukas Reference Mourtzis and Doukas2014) and combinatorial innovations (Yoo et al. Reference Yoo, Boland, Lyytinen and and Majchrzak2012; Marion et al. Reference Marion, Meyer and Barczak2015). However, they have their counterpart and entail costs. Companies are, in fact, faced with the issue of understanding the trade-off between cost, production constraints, openness and flexibility of the product architecture (Ripperda & Krause Reference Ripperda and Krause2017), which has strategic and managerial consequences, such as significant economies of scale and a lower development cost (CN7) (Simpson et al. Reference Simpson, Maier and Mistree1999).
Moreover, apart from deciding what product components should be shared and what should not, companies have to choose what layers of the platform they will permit other firms to extend (Yoo et al. Reference Yoo, Boland, Lyytinen and and Majchrzak2012) and, therefore, they have to decide on a vertical integration at the organisational level (CN8) (Cantamessa and Montagna, Reference Cantamessa and Montagna2016; Cantamessa et al. Reference Cantamessa, Montagna, Altavilla and Casagrande-Seretti2020).
Third, ‘form’ decouples from ‘function’ (Zittrain Reference Zittrain2006), and ‘digital affordance’ for features and functionalities of a digital product (Oxman Reference Oxman2006; Yoo et al. Reference Yoo, Boland, Lyytinen and and Majchrzak2012; Colombo et al. Reference Colombo, Montagna, Cascini and Palazzolo2022) might overturn the traditional approach to design, which was based on a relatively rigid mapping between functions, behaviour, and structure (CN9). Product development managers have to control a process in which new structural (immaterial/digital) features and their related behaviour are added, even after the product has been designed, produced and delivered, thus introducing new functions or changing previously existing ones (i.e., derivative innovations). This situation may represent a means of encouraging and supporting unpredictability in innovation processes (CN10) (Austin et al. Reference Austin, Devin and Sullivan2012), which implies understanding how to control and support creativity and serendipity behaviour in such frequently changing processes (Andriani & Cattani Reference Andriani and Cattani2016).
A final shift occurs in design information and knowledge management. In the distant past, digitisation processes helped explicate design knowledge through modelling (CAD systems and simulations), thus making what had previously been done through intuition and experience (e.g., storing design choices and verification activities through validated parameters and variable values) codifiable. Instead, the progressive transition to design automation is currently having the opposite effect, that is, of attributing an active role in design processes to support systems. Design support systems can incorporate the knowledge that had previously belonged to an individual or to the design team (CN11), that is, moving it from individuals to capital and changing process rules and organisation equilibria.
2.5. Gap in the literature and original contribution of the paper
The previous discussion describes the opportunities, challenges and concerns about the use of data, as well as the operational and managerial changes in design and development (summarised in Figure 1), and it highlights an increasing relevance of design analytics in design, which has led to a new data-driven design paradigm (Cantamessa et al. Reference Cantamessa, Montagna, Altavilla and Casagrande-Seretti2020, in Figure 2).
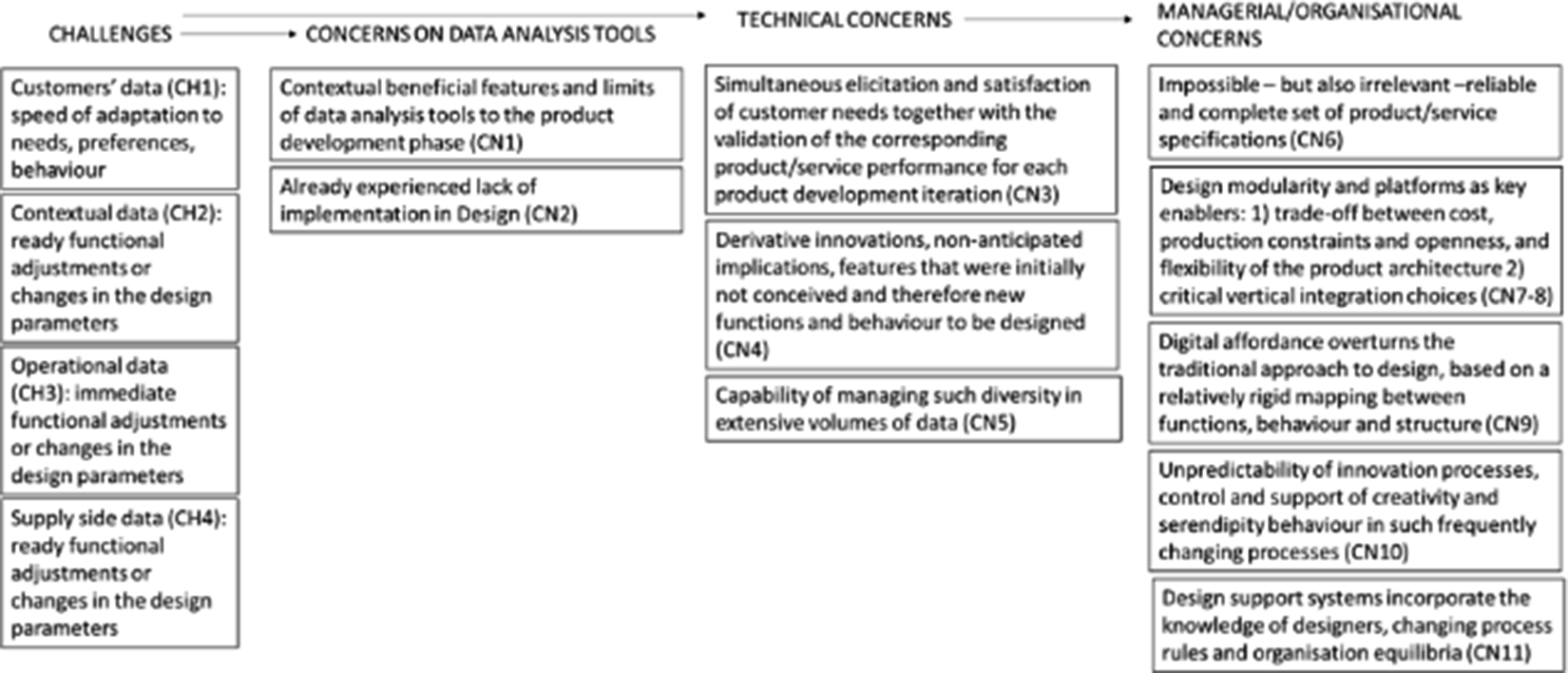
Figure 1. The challenges and emerging concerns according to the literature.
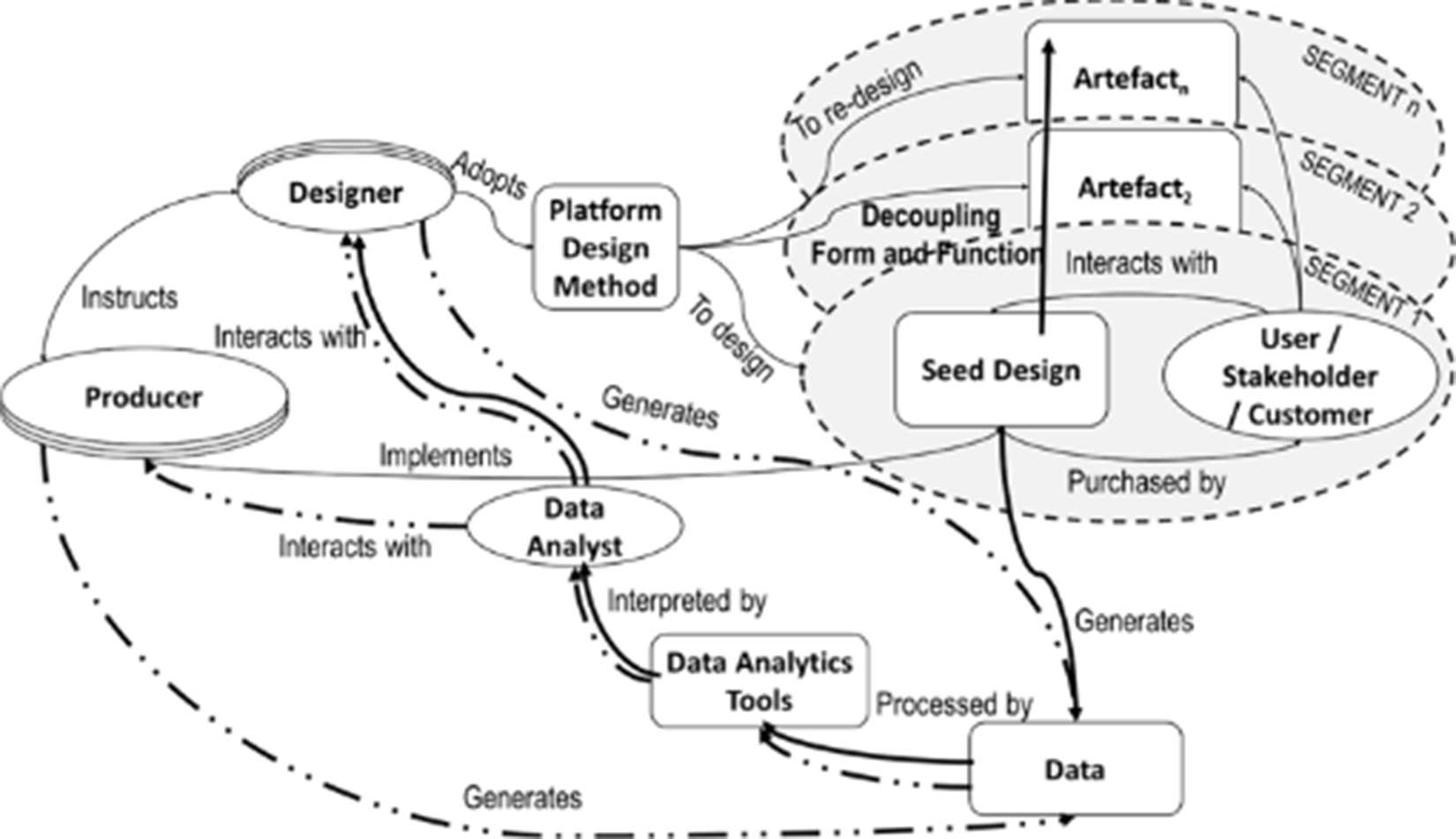
Figure 2. The new paradigm of the data-driven design context (as presented in Cantamessa et al. Reference Cantamessa, Montagna, Altavilla and Casagrande-Seretti2020).
The paradigm shown in Figure 2 represents a first overview of the shift that has been occurring in the data-driven design context; however, this overview fails to investigate the challenges and technical/operational concerns posed by the literature (the ones shown in Figure 1) in great detail and to characterise the innovative processes. In fact, it neither details the sources of the data flows and the involved stakeholders nor defines the emerging processes and practices. Indeed, only customers and producers are represented as stakeholders, without other players, such as complementors or policy-makers, who are typically decisive in innovation processes, being considered. At the same time, again with reference to the latter point, the model in Figure 2 does not represent a guideline for product design processes within data-driven innovation environments, as other emerging early proposals do (e.g., Cao et al. Reference Cao, Sun, Tan, Zhang and Liu2021; Liu et al. Reference Liu, Wang and Wang2022).
Thus, the paper investigates data-driven innovation processes on the basis of 36 case studies and elaborates on their characterising data flows. The large number of analysed companies and the rich amount of data collected allow for the validation, at least partially, of the opportunities, challenges and concerns that emerge from the literature. Specifically, it reflects on the actors involved in the processes and their roles, the data and information exchanged, as well as the tools and methods adopted. This enables to build a relational diagram upon the data-driven paradigm of Cantamessa et al. (Reference Cantamessa, Montagna, Altavilla and Casagrande-Seretti2020), incorporating also the extension of Kim (Reference Kim2022) about experience-centred data, so as to validate and complement that conceptual model. On the basis of the obtained results, considerations about the current engineering design practices that can contribute to addressing the emerged challenges are discussed.
Since the studies in the literature on emerging engineering practices (Cao et al. Reference Cao, Sun, Tan, Zhang and Liu2021; Liu et al. Reference Liu, Wang and Wang2022) are still somewhat scant and not equally structured, the contribution of this paper, that is, of clearly and rigorously framing the resources for designers in such a data-driven environment, might constitute a definitive and original step forward. Moreover, it does so on the basis of the elements of complexity that emerged from the literature investigation and the validation of numerous case studies from different industries. This approach, albeit consolidated in adjacent fields such as the domain of innovation management, represents an element of novelty in the Design research.
3. Methodology
The present paper has analysed 36 Italian companies that have invested in Industry 4.0 technologies, using a qualitative multiple case study method, and investigated their resulting data-driven innovation processes. The selection criterion was aimed at representing the composition of Italian industry in terms of the most relevant sectors. Overall, 90% of the selected companies operate in the manufacturing sector, which represents the most important Italian industrial activity. Moreover, among these companies, 30% represent the metal and mechanical sector, 13% operate in the fashion industry and 9% operate in the furniture sector, while 6% operate in the food industry. These sectors are among the most relevant manufacturing sectors in Italy, according to the number of companies (Cappelli et al. Reference Cappelli, Castagnetti, DI IORIO, Letizia Georgetti, De Santis and Monducci2024).
Although most companies in Italy are ‘micro’ enterprises (Istat, 2021), the companies considered in the sample are larger in size (i.e., medium-large companies). Such companies were included since they either represent leaders in digitalisation initiatives or are business units of multinational companies (hence, akin to an Small Medium Enterprise). In the latter case, the official registered number of all the corporation employees had to be considered.
Table 1 presents the sample and the different sectors in which the companies operate, together with a brief description of their offerings and other characteristics of their business model. The last column shows the scope of their digitalisation initiatives according to the adopted grouping approach explained below.
Table 1. Companies selected for the study
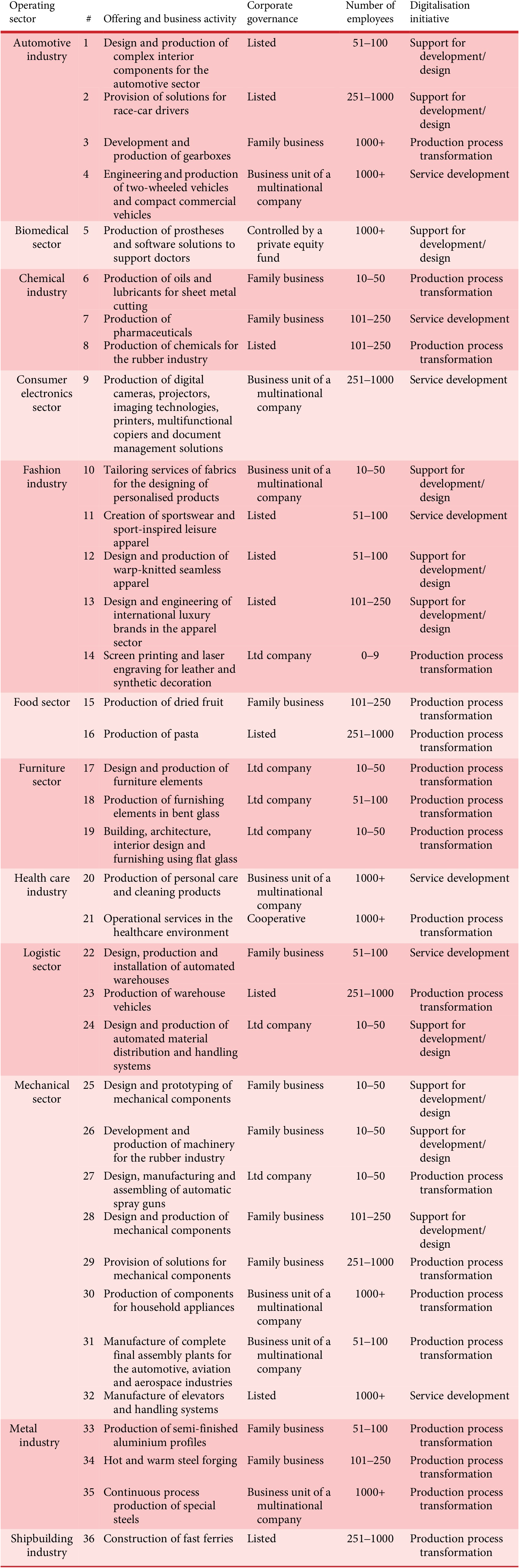
Data were collected through desk research in the field, and companies were chosen based on the documented digitalisation initiatives. Some of the case studies have been generated as a part of a project conducted with the Turin Chamber of Commerce between 2020 and 2022. The objective of such a project was to investigate the impact of design on strategic decisions and business model conversion choices (Bruno Reference Bruno2024).
The remaining case studies were selected from a number of contributions that describe the digitalisation processes of companies. Some were chosen from studies on the role of capabilities in digital transformation (e.g., Ardolino et al. Reference Ardolino, Rapaccini, Saccani, Gaiardelli, Crespi and Ruggeri2018; Matarazzo et al. Reference Matarazzo, Penco, Profumo and Quaglia2021; Mazali et al. Reference Mazali, Neirotti and Scellato2023), others were taken from papers aimed at presenting efficient applications of digital tools and data analytics (e.g., Datar et al. Reference Datar, Mehta and Hamilton2020; Giallanza et al. Reference Giallanza, Aiello, Marannano and Nigrelli2020) and still others from contributions that examined digital trends in a given sector (e.g., Trino Reference Trino2020). Such documentations recognised the exploitation of digital opportunities by analysing companies’ management of innovation, strategies and business models. Changes in value creation processes, along with the relationships and transformation of roles, collaboration with stakeholders and the generation of new information and knowledge, were described. Therefore, from the readings, it was possible to extract the activities involved in the technological change resulting from those investments, which, according to their objective, led to the distinction of three prevalent groups, namely service development, production process transformation and support to development/design (the groups and their characteristics are later presented in Table 2, adopting the labelling of group 1, group 2 and group 3, respectively). Seven companies in the sample belong to the first group, 19 to the second group and 10 to the third.
Table 2. Characteristics of the groups and their initiatives
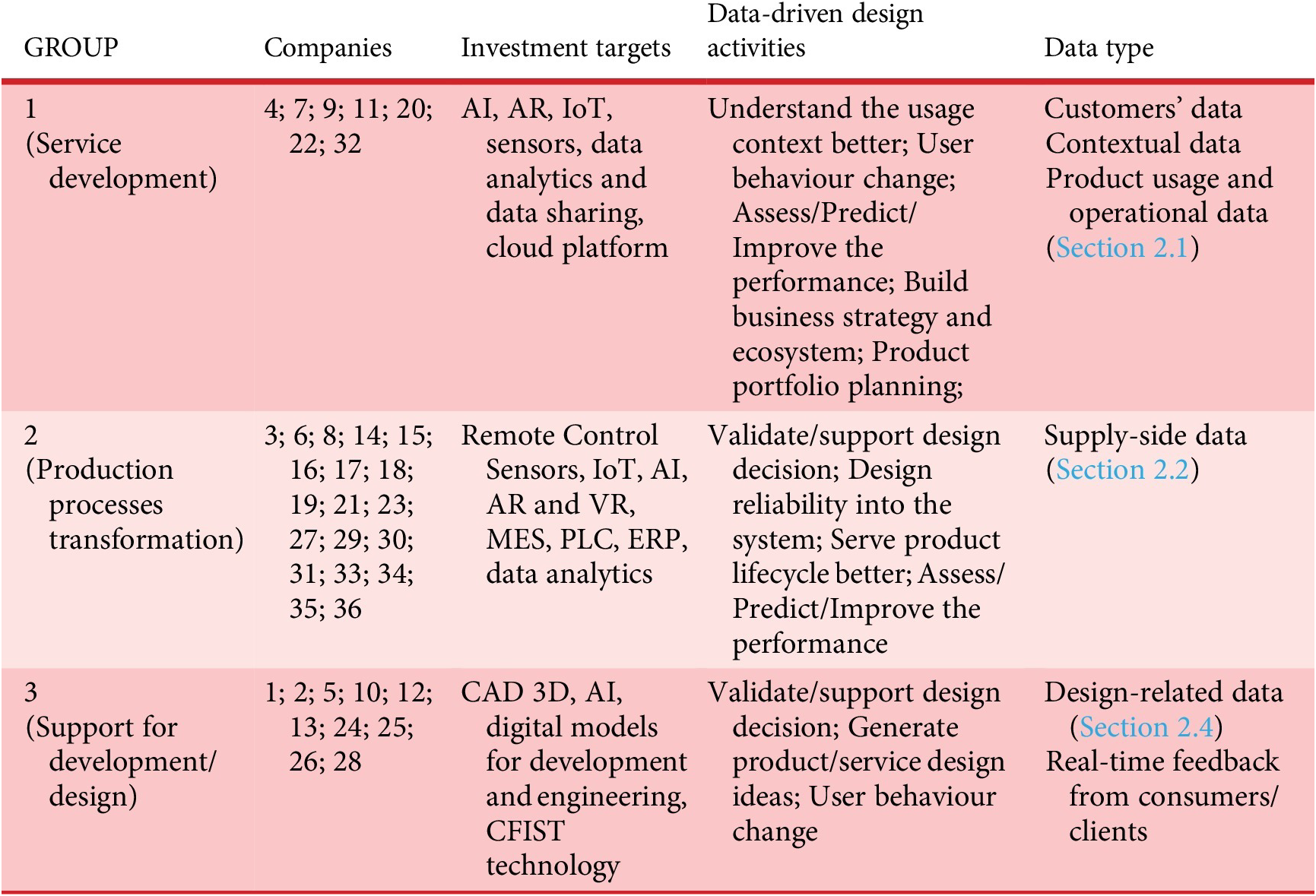
Reflecting on the data flows and information gathered and exchanged in the processes, a relational diagram was built and overlaid upon the data-driven paradigm (Cantamessa et al. Reference Cantamessa, Montagna, Altavilla and Casagrande-Seretti2020, Figure 2). That activity was used to validate the already represented relationships and complement them with those that had emerged. Finally, the raised opportunities, challenges and concerns were examined against the findings from the literature review and framed according to the scope of the initiative (Table 3 in Section 4).
Table 3. Data flow types and the related opportunities and concerns
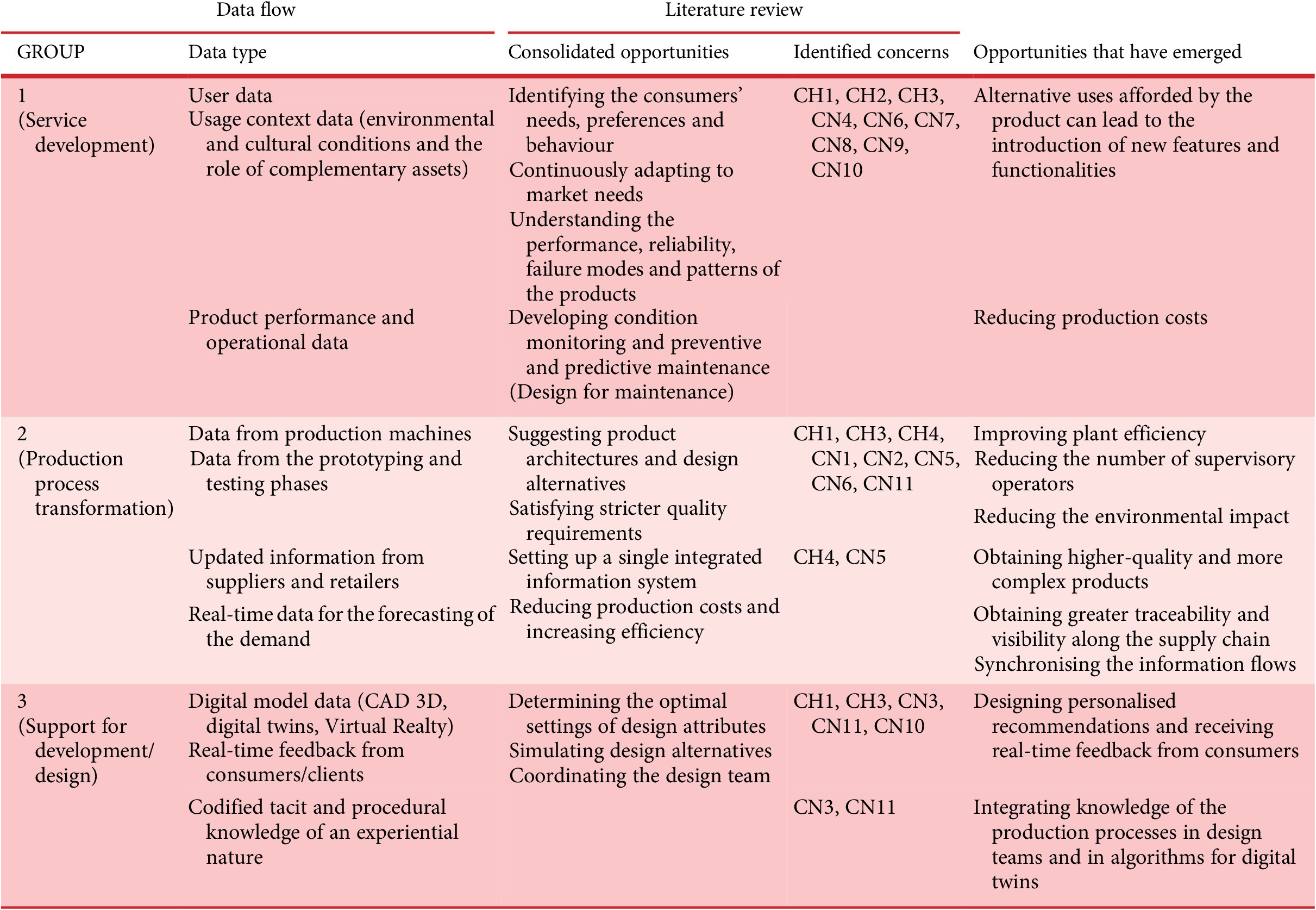
4. Results and discussion
4.1. Companies’ digitalisation initiatives and the emerging data flows
Group 1 identifies the companies in the sample that have mainly invested in Artificial Intelligence (AI), Augmented Reality (AR) and Internet of Things (IoT) technologies to target specific customer segments or provide personalised services, coherently with section 2.1 of the literature review and with Wang et al. (Reference Wang, Chen, Zheng, Li and Khoo2019), who had identified such a trend, especially about user and usage data (demand-side data). Moreover, thanks to their capacity to perform data analysis, these companies have been able to offer complementary or additional services (sometimes also very far from their original focus) to position themselves in different markets. This is the case of Company 9, which operates in the consumer electronics sector (Ardolino et al. Reference Ardolino, Rapaccini, Saccani, Gaiardelli, Crespi and Ruggeri2018). By provisioning their printing machines with IoT sensors, they have managed to combine the sales of printers with a subscription for the automatic replenishment of consumables. Consequently, data on machine status and usage (e.g., the number of printed copies) have been used to generate automatic invoices and to schedule maintenance interventions and toner supplies.
Apart from demand-side data exploitation, some of the companies in the sample have also invested in digitalisation for production assets and automation (i.e., group 2) in view of increasing their production efficiency, integration and quality. The target technologies in group 2 mainly included IoT, Manufacturing Execution System (MES) or Programmable Logic Controller (PLC). Coherently with the literature, elements of non-quality tend to become less frequent or at least measurable and predictable, thanks to these technologies (Tao et al. Reference Tao2018). For example, Company 36, which is a leading fast ferry operator, applied the principles of Industry 4.0 to a shipyard to collect accurate real-time data, especially during real-life condition tests (Giallanza et al. Reference Giallanza, Aiello, Marannano and Nigrelli2020). During thruster test runs, digital technologies, such as the IoT, cloud computing and big data analytics, allow specific control parameters (rotation speed, rated power, applied torque, etc.) to be monitored and real-time values (plus the maximum values) of the temperature, pressure and strain to be collected.
At the same time, industrialisation alternatives can be conceived as advanced technologies that enable the production of enhanced-performance products (Soleimani et al. Reference Soleimani, Pourgol-Mohammad, Rostami and Ghanbari2014; Abramovici et al. Reference Abramovici, Gebus, Göbel and Savarino2017) or the minimisation of the environmental impact of production processes (Mayyas et al. Reference Mayyas, Qattawi, Omar and Shan2012). For instance, Company 19 operates in the glass furniture sector and, thanks to investment in PLC and automation in their cutting and grinding lines, has been able to process large sheets of float glass up to 19 mm thick. Data from digital models are sent directly to digital printing machines, which are able to reproduce any graphical element and decoration using ceramic inks. Company 18 pursued digitalisation initiatives or even created ‘ad hoc’ technologies within the production environment in order to control the success of specific processes (e.g., glass bending process) and, at the same time, integrate environmental practices (e.g., reprocessing activities concerning waste and garbage) (Barbaritano & Savelli Reference Barbaritano and Savelli2020).
Finally, digitalisation initiatives cannot exclude investments in CAD 3D and in AR for the development of a ‘digital twin’ and support in product development (i.e., group 3). Again, coherently with the literature in Section 2.4, these technologies support designers in the exploration of alternatives and their decision-making processes, and they assist the creative process by reducing designers’ discretion (Chiarello et al. Reference Chiarello, Belingheri and Fantoni2021). The development activities frequently take place in co-design mode with the customer/client, which is frequently the main goal of the investment. Companies 10 and 13, both of which operate in the fashion industry, are examples of this approach (Trino Reference Trino2020; Mazali et al., Reference Mazali, Neirotti and Scellato2023). In Company 10, the user, supported by systems that gather data directly from customers (e.g., body scanner 3D), can personalise each tailoring detail through a 3D configurator. The output can be visualised in real-time through the 3D model so that immediate feedback can be obtained. Similarly, Company 13 has included 3D technologies in product development phases, thereby increasing the interactions between model makers and stylists, as well as enabling users to be involved in choosing the design solution. Coordination takes place remotely and almost in real-time.
Company 5 is a similar case, but in a different sector. Working on the production of prostheses and software solutions to aid doctors, they model a patient’s skeleton, digitally reproduce the prostheses, detect any possible fitting problems and intervene in the fine-tuning (Mazali et al. Reference Mazali, Neirotti and Scellato2023). When they employ additive manufacturing techniques, they send digital models directly to the production machines.
Table 2 shows the differences between the digital initiatives of the companies, grouped according to the objective of the activities in their innovation processes (i.e., group 1, group 2 and group3). The table highlights the technology investment targets and maps the data-driven design activities (as suggested in Lee & Ahmed-Kristensen Reference Lee and Ahmed-Kristensen2023) affected by the initiatives. The last column reports the type of data exploitable thanks to the new technologies, with reference to the literature section where they are presented.
The data flows emerging from the case studies have been overlaid on the data-driven design paradigm (Cantamessa et al. Reference Cantamessa, Montagna, Altavilla and Casagrande-Seretti2020) and presented in Figure 3, distinguishing the initiatives from which they originate (i.e., group 1, group 2 and group 3). Such a representation emphasises how the observed data flows validate and complement the paradigm.
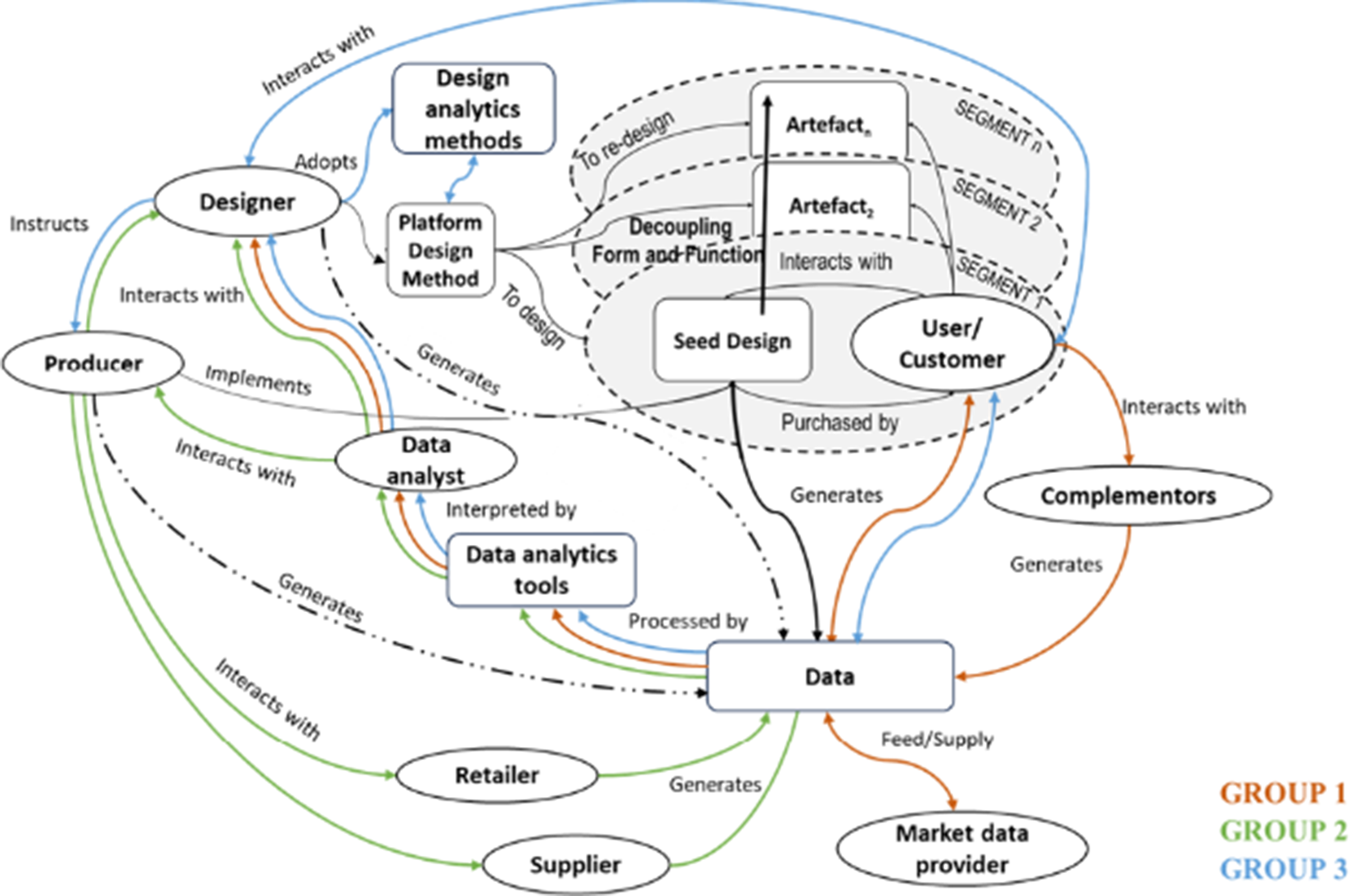
Figure 3. Extended data-driven design paradigm with the new data flows identified in the present study.
Indeed, the role of both demand and supply flow of information is confirmed to be relevant and to involve designers and producers together with the novel figure of the data analyst. Moreover, the role of tools and methods in guiding designers’ analysis activity is broadened, recognising the relevance not only pertaining to data analytics and platform design but also including design analytics methods.
Thanks to the case studies, new actors have been confirmed to be decisive in data-driven innovation activities, thus deserving consideration and, specifically, to be added to the paradigm. As a matter of fact, in light of a demand-side data evolution, actors like complementors and market data providers have demonstrated to be crucial in collecting data about the artefact usage and surrounding context, especially in those initiatives aimed at providing additional and personalised services to customers (i.e., group 1). Data provided directly by users, consumers and customers are also added here, with consideration of the extension of Kim (Reference Kim2022) with zero-party data, reflected in the dual-directional arrow between data and user.
The digitalisation of production assets and automation (i.e., group 2) instead revealed the contributions of external suppliers and final retailers in the exchange of data and information, often aimed at creating an integrated information system and generating new design alternatives. Finally, apart from confirming the direct observation of customers’ interaction with the artefacts, and thus the continuous acquisition of data, the paradigm in Figure 3 also adds a potential direct relationship between the designer and consumers through real-time feedback exchanged during co-design activities (i.e., group 3).
4.2. Challenges and concerns emerged from the literature and from the study
The analysis of the companies’ initiatives in digitalisation highlights the differences in the mode of action of the companies, which depend on their strategic intent, the scope and technological target of the initiative and the related application. Examining the companies was also useful in confirming the changes, concerns and challenges identified in the literature.
The digitalisation initiatives in group 1 have enabled companies to collect information on the users and their usage to develop tailored solutions and offer additional services. Data about the users’ profiles, behaviour, needs and preferences, as well as environmental/external conditions, are gathered in real time, and the gathered information is used to create new design parameters and make functional adjustments. Thanks to this information, features that were not anticipated and new functions emerge (CN4, CN6, CN9, CN10). However, it is neither trivial nor automatic to change design procedures in order to ensure that these data become readily usable and to keep up with continuously evolving market stimuli (CH1, CH2, CH3). Such solutions in fact often involve trade-offs between costs, production constraints and flexibility of the product architecture, with certain consequences at the organisational level (CN7, CN8). Company 9 is a clear example of this. On the one hand, the connected machines have guaranteed consumers the possibility of automatically replenishing consumables as soon as the printers detect that the ink or toner is running out. On the other hand, this has raised issues in terms of security, doubts about complexity and costs due to the necessary hardware and software modifications. In order to address these problems and to maximise the potential of the obtained data and the benefits of large-scale projects, the company decided to develop a new platform as a layer of the ‘technology stack’ (Porter & Heppelmann Reference Porter and Heppelmann2014), in order to build and support new technology infrastructures.
The companies in group 2 are characterised by initiatives of digitalisation and automatisation in their manufacturing environment. Such companies have the aim of receiving data directly from the production machines and integrating their supply chain with an updated exchange of information. These interventions enable greater efficiency and higher quality, and also offer novel industrialisation alternatives (CH4). In the same way as in group 1, but this time with a broader scope, the changes that had to be introduced were far from being straightforward (CH1, CH3). Different domains, such as design and manufacturing and after-sales services are affected, as they are called upon to cooperate by integrating different competencies and to make what was previously done by intuition codifiable (CN5, CN11). All of this contributes to the development of an innovative environment that supports the interactive engineering of the company, where the design and development phases are performed in parallel rather than in series (CN6), in order to reduce production times and costs.
Company 36 is an emblematic case, as the complete digital transformation of manufacturing has not only involved the production and management of the shipyard but also the product design and engineering techniques. Experimental data are directly transmitted to the technical office so that engineers can analyse the data in real time and perform an interactive design to improve the performance of the entire system or of any critical components. The digitalisation initiatives in Companies 16 and 19 are linked to the production of higher quality and more complex products: data integration helps Company 16 to choose higher quality wheat for the production of pasta, while the automation of the machines allows Company 19 to process thicker glass sheets, realise engravings, etc. Conversely, Company 18 was able to reinvent glass by transforming the production process, thanks to the technological advancements and a continuous interaction between material and process engineers, designers and marketers. Such an innovative material is composed of recycled scraps from sheets of glass, resulting in random combinations of colours, which improves the creative features of the final products and fully embraces the principles of circular economy.
Finally, the companies in group 3 have pursued digitalisation initiatives in product development and (co)design activities with the users. The customers/users contribute to the creation of an artefact, validate its characteristics and performance and give real-time feedback (CN3). Again, in this case, challenges associated with the speed of adaptation and with immediate functional adjustments and changes in the design parameters have emerged (CH1, CH3, CN10). Moreover, the use of digital tools to support the design process considerably decreases the discretion of the designers (CN11).
In Companies 10 and 13, both of which work in the fashion industry, the users are actively involved in the design process. In Company 10, thanks to a 3D configurator, the users autonomously edit and simultaneously visualise their preferences, while a 3D body scanner enables immediate functional and design adaptations to be made; the users of Company 13 can intervene remotely in the exploration of the different design alternatives and eventually highlight errors or more suitable options. Instead, in Company 5, digital models enable different simulations to be run (e.g., to move a screw) and mechanical tests to be performed without destroying expensive samples. In all these cases, the experience and intuition of designers are incorporated into the support systems/tools, which have begun to play an active role in the process.
The aforementioned results have been summarised and structured in Table 3, specifically highlighting the changes, concerns and challenges that have manifested within the case studies, to which the engineering design domain can contribute. Indeed, for each group, the type of data that characterises the flow of information exchanged and gathered in the process involved in digitalisation initiatives is explicated. Then, the opportunities and concerns arising from such data flows are presented and divided depending on whether they are ‘consolidated’ or newly emerging from the case studies. The former are examined in light of the state of the art and presented in the ‘Literature review’ column, while the latter are summarised in the final column.
Information that is more relevant for design and development processes has been distinguished from information that has other purposes, with the latter highlighted in grey, even though all the information is relevant to the innovation strategies of the companies.
5. The potential role of engineering design
Most of the evidence emerged from the study validates the literature discussion proposed in Section 2. However, some of these elements are still not established in the literature and concern the possibility of
-
1) Designing personalised recommendations and real-time feedback from the customers/users;
-
2) Recognising alternative uses afforded by the product for the introduction of new features and functionalities;
-
3) Integrating knowledge about the production processes in algorithms for digital models to complement the designers’ background, knowledge and expertise.
However, these elements of opportunity in data-driven environments present some unresolved problems related to the real-time data collection itself. Indeed, although innovation approaches are based on profound market research and are aimed at achieving an improved personalisation of customer experience, the adaptation of operational and management practices to arrive at the systematic use of real-time data still needs to be completed, and this involves an increasing variety of tasks and roles, as well as the definition of new practices and processes. However, some consolidated engineering design practices can help address the challenges arising from the new elements of complexity in such a data-driven environment and contribute to their resolution.
First, it is essential to radically enhance the changeability and adaptability of processes and products to ensure flexibility and deal with critical aspects rapidly. Moreover, exploiting supply-side data enables increasingly demanding requirements, in terms of quality, time and costs, to be dealt with. Practices such as Design for Manufacturing, Assembly or Logistics, etc. are aimed at reducing the lead times, total production costs and/or the total cost of ownership throughout the entire lifecycle, in view of ease of manufacturing, a simplified assembly of parts and reduced issues of transportation and maintenance (Emmatty & Sarmah Reference Emmatty and Sarmah2012). Robust design instead focuses on making the functions of a product more consistent with variations in the downstream processes and environmental changes. Design for Mass Personalisation approaches enable the user to tailor a seed design according to their own preferences, even beyond the range of configurations initially conceived by the manufacturer (Ozdemir et al. Reference Ozdemir, Verlinden and Cascini2022). Personalisation usually concerns aesthetic features, but it could also pertain to adjustments of product functionalities and ergonomics.
So far, personalisation has been introduced as the result of the explicit demands of consumers. However, Machine Learning algorithms, applied to the data collected in smart products, may be increasingly used to support the recognition of human preferences, even those that the users are not aware of, thus offering new personalisation opportunities. The comprehensive, special issue edited by Panchal et al. (Reference Panchal, Fuge, Liu, Missoum and Tucker2019) provides a rich overview of machine learning applications in engineering design, which can also be used to elicit users’ preferences. Nevertheless, some gaps still exist in translating the observed behaviour into proposals for new product functions. For example, in the context of this study, Company 4 produces two-wheeled vehicles and has started to offer ‘sharing services’ to exploit real-time data about the density and timing of scooter movements to target specific customer segments, such as residents of the same building, and to develop tailored solutions (Ardolino, Reference Ardolino, Rapaccini, Saccani, Gaiardelli, Crespi and Ruggeri2018).
The recognition of unexpected alternative uses could enable ex-post updates of the software of a product to match the new functionalities that are offered. In this perspective, Affordance-based Design (Maier and Fadel, Reference Maier and Fadel2009) provides the cognitive elements necessary to frame the development of smart products that can be easily upgraded to offer new functions and unexpected user experiences (Pucillo & Cascini Reference Pucillo and Cascini2014). For instance, the smart toothbrush made by Company 20, which produces personal care and cleaning products, could be used to help adult users monitor the hygiene habits of elderly people as a proxy for their wellness and care (Datar et al. Reference Datar, Mehta and Hamilton2020).
Overall, functional expansion is emerging as a pervasive phenomenon that increasingly involves consumer products, and the design theory allows such dynamics to be represented beyond the optimisation perspective of econometric models (Le Masson et al. Reference Le Masson, El Qaoumi, Hatchuel and Weil2019). Qualitative transformations of products are also being mapped through patterns derived from the empirical observations of the evolution of technical systems, as proposed in TRIZ models (Cascini Reference Cascini2012). In this context, the systematic comparison of successful and unsuccessful products with their predecessors (Borgianni et al. Reference Borgianni, Cascini, Pucillo and Rotini2013; Casagrande-Seretti et al. Reference Casagrande-Seretti, Montagna and Cascini2019) allows the expected market appraisal of the alternative product profiles that have to be designed to be assessed in advance, thereby partially addressing the phenomenon of derivative innovations.
Furthermore, User-centred Design has analysed the similarities and differences in the concept of user value in different domains, such as anthropology, sociology, philosophy, business and economics, thus producing a comprehensive categorisation to distinguish between utility, social significance and emotional and spiritual dimensions of user value (Boztepe Reference Boztepe2007).
The Agile approach, applied to design and development, also goes in this direction, thanks to its iterative process, as it does not force a designer to start working on high-fidelity prototypes straight away, but instead fosters interactions to constantly validate the users’ needs, translate them into design attributes and improve the product (Da Silva et al. Reference Da Silva, Martin, Maurer and Silveira2011).
This kind of data exploitation obviously raises serious ethical concerns about what the new balance between machines and human beings should be, and it might infringe on privacy and security regulations. These concerns are well known in the design of assistive technology. Participatory multidisciplinary approaches have already been successfully adopted in this field, and they could inspire reference models to incorporate ethical and social issues in the development of smart products (Participatory Design; Oishi et al. Reference Oishi, Mitchell and Van der2010; Udoewa Reference Udoewa2022).
Finally, analogous considerations can be made for design practices aimed at integrating production process knowledge. Production process parameters can be taken into account in Design Optimisation models through both simulation and empirical approaches (Zhao et al. Reference Zhao, Icoz, Jaluria and Knight2007).
Table 4 presents the concerns that have emerged from the literature (Section 2, CN1-CN11) and the opportunities recognised from the analysis of the case studies (Table 3), relating them to the extant engineering design literature. In the second and third columns, indeed, the authors suggest some engineering design practices, either consolidated or emerging, that appear relevant to address those identified concerns and opportunities. Even though only in a preliminary state, this attempt at mapping concerns and engineering design resources is meant to offer insights into future directions of design research.
Table 4. Concerns from the literature, opportunities recognised in the case studies and engineering design topics that might have a role in addressing them
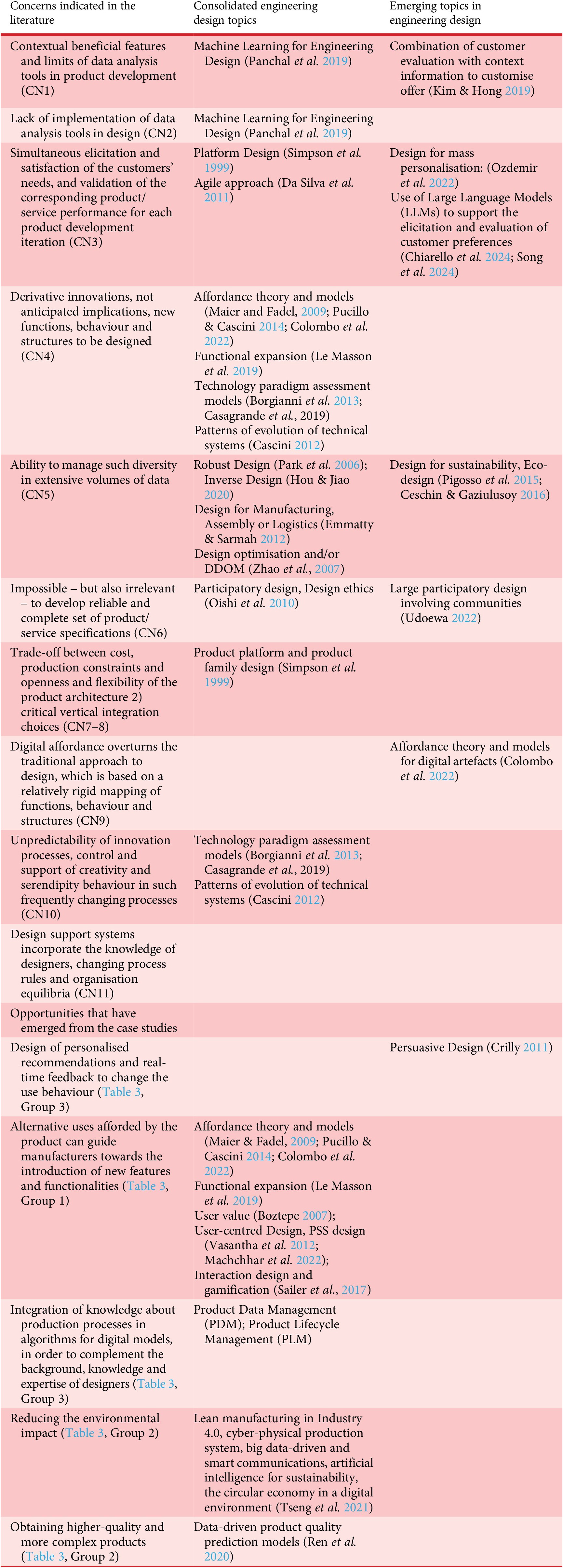
6. Conclusions
Exploiting digitalisation and data-driven innovation raises new concerns that have not yet been addressed for the current innovation and development processes or practices.
The paper offers a structured overview of the use of data in innovation processes, distinguishing between the studies available in the literature on customer and user data, data related to the context (environmental conditions, socio-cultural conditions, complementary goods), usage and operational data, as well as supply-side data. All these types of data can play a role in the design of smart products and digital services and allow the technical, operational and managerial changes necessary to lead such a data-driven transformation to be depicted. Starting from a careful literature review, this paper provides an original structured classification of challenges and concerns emerging in the field of data-driven innovation processes. These have been analysed and discussed against the information related to digitalisation initiatives that occurred in 36 Italian manufacturing companies from several industrial sectors. In doing so, the paper also proposes an updated version of the data-driven design paradigm presented by Cantamessa et al. Reference Cantamessa, Montagna, Altavilla and Casagrande-Seretti2020, incorporating the extension of Kim (Reference Kim2022). The analysis of the 36 Italian companies confirms the validity of the revised model by mapping the data flows and information gathered and exchanged in the innovation processes.
Among the others, it emerged that new operational and design tasks are becoming increasingly necessary, but the current industrial practice has no reference processes to address such tasks, and the literature does not offer adequate responses. Moreover, although design teams and processes are largely involved in the digital transition, the role design research and its literature can play in enabling data-driven innovation and overcoming emerging concerns is still unclear. The paper has attempted to provide a methodologically rigorous map of data flow types and the related opportunities and concerns. The latter ones offer the opportunity to suggest some consolidated engineering design literature resources that can provide useful support in building a new methodological reference framework for data-driven innovation.
On the practical side, the classification of the analysed companies into three groups (i.e., service development group, production process transformation group and support for development/design group), the elicitation of their investment targets and the data-driven design activities described in the reports of those digitalisation initiatives offer an overview of what is already ongoing in some advanced companies, hence worthy of consideration for replicability. Furthermore, strategically relevant data flow types in the groups of companies recognised in this study have been connected with innovation opportunities and might attract the attention of further stakeholders in the exploitation of product and process data. Ultimately, the collection of the proposed cases and new ones in a repository built on the main types of companies and data flows identified in this paper can provide practical guidance in industrial practice. Nevertheless, how to properly structure a repository with this intent requires further elaboration and preliminary testing; as such, it is not part of this study.