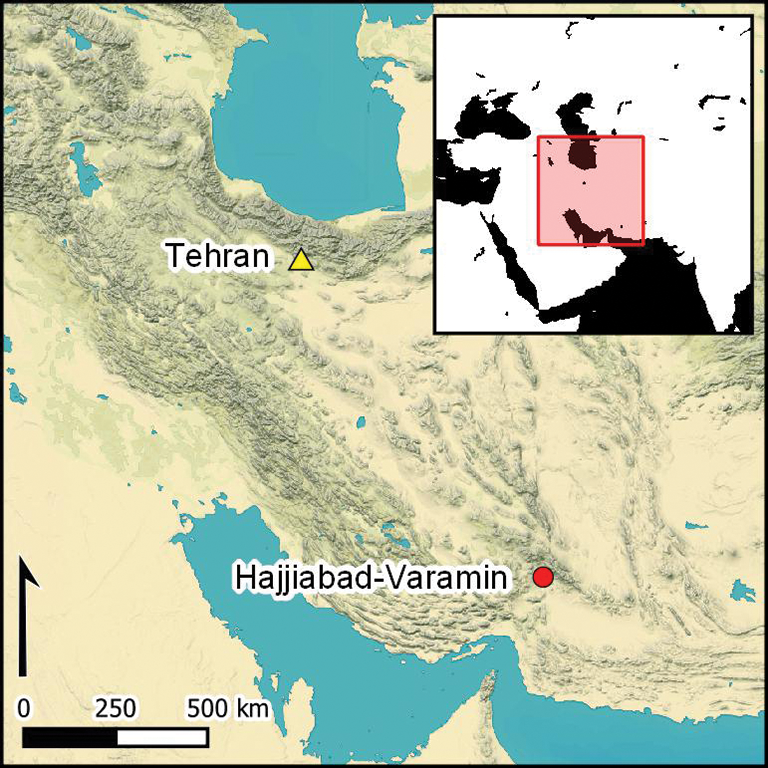
Introduction
Stone vessels produced from a variety of lithologies were widely used across the ancient Middle East. In this article, we present evidence from a craft-production site at Hajjiabad-Varamin in south-eastern Iran and focus, in particular, on a collection of stone drill heads, or bits, used for the manufacture of travertine/calcite vessels (Figure 1) (Eskandari et al. Reference Eskandari2021). We establish the regional geological context and then use a comparative approach to consider the manufacturing techniques used and possible networks of technological knowledge across the wider Middle East. Through better documentation of stone-vessel manufacturing and the technologies used, we aim to deepen understanding of Bronze Age stone working in Southwest Asia. We also consider the question of whether there was a specific south-eastern Iranian technological style that distinguished it from contemporaneous stone-working traditions, such as that located in Egypt.
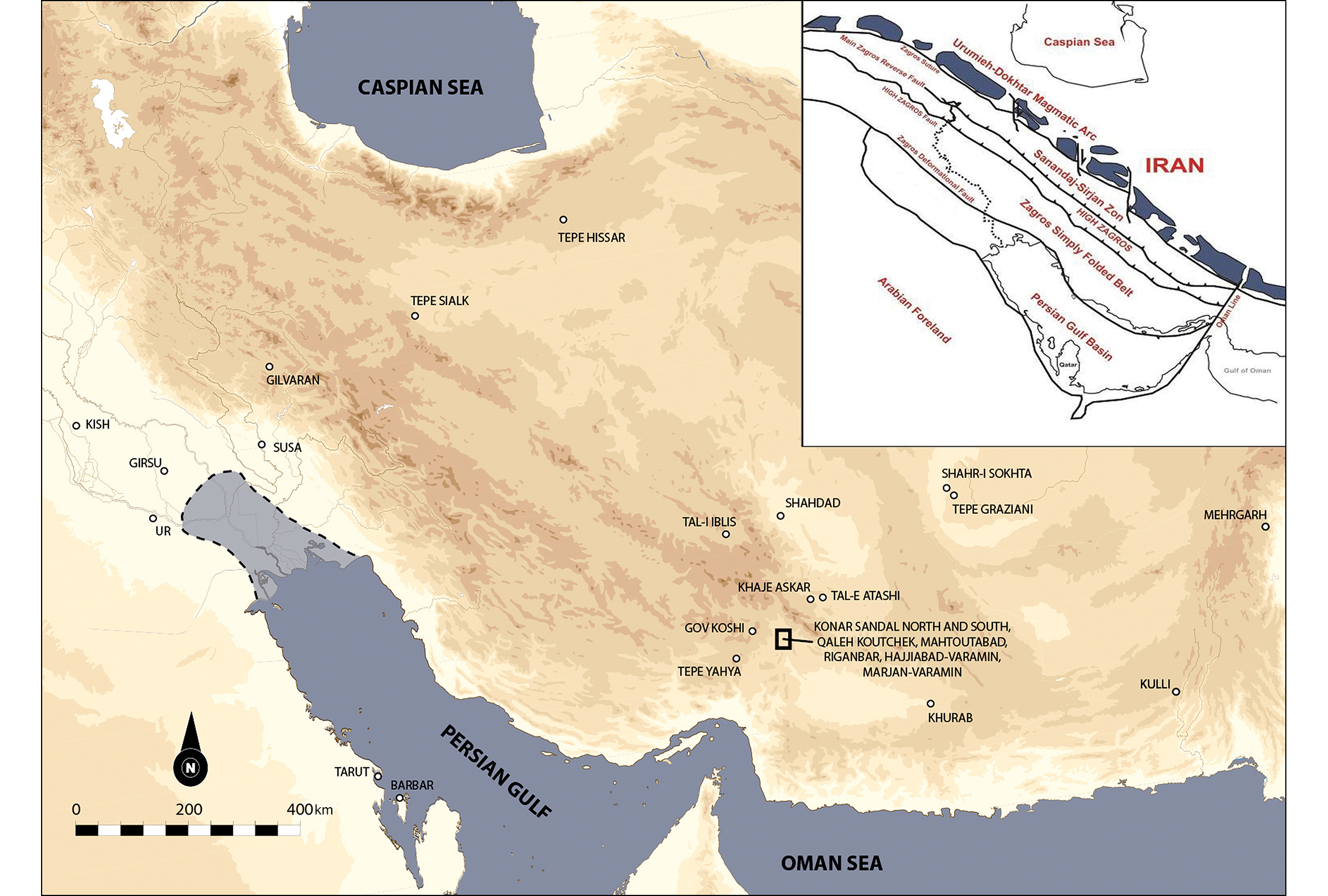
Figure 1. Map of the Iranian Plateau, showing the location of the prehistoric and protohistoric sites mentioned in the text. Upper right) geological map of the Iranian Plateau: the dark areas mark the Urumieh-Dokhtar arc, rich in travertine outcrops (map by M. Vidale, modified after Samari Reference Samari2016).
When archaeologists of the ancient Middle East speak of ‘alabaster’ vessels (e.g. Casanova Reference Casanova1991), the term applies to the wide spectrum of semi-precious stones used for the production of these containers, and is considered “a hybrid name not recognised by geologists” (Moorey Reference Moorey1999: 59; also see Ciarla Reference Ciarla and Haertel1981: 46). In Iran, the raw materials used for the manufacture of these vessels were banded, fibrous-crystalline calcium carbonate rocks found within travertine deposits (Samari Reference Samari2016). Composed of the carbonate minerals of calcite and aragonite, these rocks—approximately 3–4 on the Mohs scale—are relatively easy to work. Typically sub-translucent, they have a lustre ranging from dull to pearly and sub-vitreous. Bands of contrasting colours vary from white to greenish, brown, reddish, pink, yellow and, more rarely, blue. Research at third-millennium BC craft-production sites in eastern Iran (e.g. Shahdad, Shahr-i Sokhta and the Konar Sandal South complex) reveals that stonecutters produced vessels, beads and other objects using carbonate rocks with white/translucent bands of calcite alternating with bands of deep red aragonite (e.g. Kavosh et al. Reference Kavosh, Vidale and Nashli2019; Eskandari et al. Reference Eskandari2021). This evidence complements the documented long-term exploitation of travertine deposits in Iran as a source of various ornamental stones through to the present day (Hora Reference Hora, Lefebure and Höy1996). In the still-active ornamental stone industries of Afghanistan, Iran and Pakistan (e.g. Shafai et al. Reference Shafai2020: 70–75), such travertine deposits are erroneously considered to be varieties of marble. Other designations include ‘green onyx’ or ‘Balochistan onyx’; however, these commercial labels should be reserved for banded varieties of silica/chalcedony, whose mineralogy is distinct from carbonate rocks. In this article, we focus exclusively on vessels produced using translucent carbonate rock varieties.
Carbonate rock formation in south-eastern Iran and neighbouring regions
Capezzuoli et al. (Reference Capezzuoli, Gandin and Pedley2014) explain the geological processes that lead to the formation of deposits of banded calcite/travertine thus:
Terrestrial carbonates comprise a wide spectrum of lithologies (speleothems, calcrete, lacustrine limestone, travertines and tufas) which are mainly precipitated under subaerial conditions from calcium bicarbonate-rich waters in a large variety of depositional and diagenetic settings. (Capezzuoli et al. Reference Capezzuoli, Gandin and Pedley2014: 1)
In areas that are tectonically active, however, they suggest that “localised travertine deposits are also developed from deeply circulating hydrothermal waters” (Capezzuoli et al. Reference Capezzuoli, Gandin and Pedley2014: 1). In Iran, the proximity of prehistoric sites to mineral springs (Heydari-Guran et al. Reference Heydari-Guran, Ghasidian, Conard, Otte, Biglari and Jaubert2009), where the precipitation of calcium carbonate forms deposits of travertine, suggests that human groups have long been attracted to this visually appealing type of stone. According to a conference presentation by Samari (Reference Samari2016), a major part of Iranian travertine reserves is located along the Iranian volcanic belt, or magmatic arc, known as Urumieh-Dokhtar (Figure 1). This belt, on average 100km wide, runs parallel with the Zagros Mountain range, from north-west to south-east, extending 1700km from the Sahand and Sabalan volcanoes in Azerbaijan to the Bazman and Taftan volcanoes in Balochistan. Samari (Reference Samari2016: slide 2) calls this belt the “Iranian overall onyx and travertine hot spring strip”.
Along the course of the Urumieh-Dokhtar belt, Tarrah et al. (Reference Tarrah, Aedpour and Mirhosseini2014) report major deposits of white-banded calcite near the village of Tazerj in Hormuzgan Province, at the southern end of the Halil Rud Valley, where the stone vessel manufacturing sites presented in this article are located.
Travertine is ubiquitous in this geological context and easily accessible from the Halil Rud Valley; the massive outcrops of white carbonates are still being quarried today, 10–15km west of Jiroft. Further east, in the Chagai Hills in western Balochistan, Pakistan, and the Sukalok-Arbu belt to the north and west of the Chagai in Afghanistan, aragonite (travertine) deposits have long been a source of ‘onyx marble’ as an ornamental stone (Stoeser Reference Stoeser, Peters, King, Mack and Chornack2011). Ciarla (Reference Ciarla and Haertel1981: 47–48) mentions travertine deposits along the banks of the Helmand River, on the eastern side of the Kuh-i Birjand ridge (between the Lut Desert and the Sistan endoreic basin near the Afghan border) and on gravel fans of the Kuh-i Malik Siah (along the southern Sistan piedmont on the borders of Afghanistan, Iran and Pakistan). This wealth of carbonate rocks available across south-eastern Iran makes it a likely source of these raw materials for the large-scale production of stone vessels to supply the wider ancient Middle East, including Mesopotamia.
Hajjiabad-Varamin
The site of Hajjiabad-Varamin is located near the town of Jiroft in Kerman Province. Investigations of the site have identified a large settlement on a mound, with occupation extending from the late fifth to the late third millennium BC, forming part of a dense network of contemporaneous sites, including the urban centre at Konar Sandal South 5km to the north-east (Pfälzner & Soleimani Reference Pfälzner and Soleimani2017; Eskandari et al. Reference Eskandari2021). The site includes a number of cemetery areas, and, to the immediate east of the main mound, an area characterised by large quantities of broken stone vessels, indicating industrial-scale craft production (Figure 2). The production area covers approximately 0.5ha (50 × 100m) and represents the largest known industrial site of this date on the Iranian Plateau. The pottery recovered from the surface of this area is highly fragmented and ranges in date from the early to mid-third millennium BC. The stone vessel fragments include carinated shapes (Figure 3a–e) and larger, sub-cylindrical forms (Figure 3f–i), as well as thousands of less distinctive fragments. These vessels were presumably broken during production, although a small number have polished bases that may indicate modification and reuse.

Figure 2. View of Hajjiaba-Varamin from the east. The manufacturing area (approximately 50 × 100m) is marked on the surface by a spread of pebbles, stone fragments and tools. In the background is the site's main mounded area (photograph by M. Vidale).

Figure 3. Calcite stone vessel fragments from Hajjiabad-Varamin: a–e) small, carinated forms with everted rims; f–i) cylindrical forms; in (j) and (k), the drilling axis does not match that of the vessel; l) quartzite drilling capstone (upper image) or unfinished dish (lower image); m) multiple borings; n) rare bumps on the inner base suggest the use of hollow drill heads; o) coarse concentric drilling marks indicate that the piece was broken while being hollowed (scales in cm) (illustrations by I. Caldana).
A full analysis of the organisation of stone-vessel production at Hajjiabad-Varamin will require quantitative surface collection of the thousands of fragments visible on the site's surface, combined with stratigraphic excavation—work not yet undertaken. It is clear, however, that the scale of production at the site was intended for export, most likely destined for the Mesopotamian market (Moorey Reference Moorey1999: 45–46). We focus on the recovery from the production area of 12 drill heads of different forms and various lithologies, nine of which are published here. These are discussed alongside the evidence of travertine vessels from the same location, broken during the manufacturing process while being hollowed out. All of these objects are now stored at the Iranian Centre for Archaeological Research at Jiroft (Kerman Province).
Calcite stone vessel production: Hajjiabad-Varamin in context
Stone vessels and possible production are attested at a number of sites in Bronze Age Iran. The large Bronze Age centre of Shahr-i Sokhta, in Sistan and Balochistan Province, has produced abundant evidence of production waste and unfinished vessels. Although no discrete workshop areas have been found at the site, Ciarla (Reference Ciarla and Haertel1981) argues that it was a production centre. Based on this evidence, Ciarla (Reference Ciarla and Haertel1981, Reference Ciarla1985) reconstructs a four-step manufacturing process, supported by ethnoarchaeological observation of contemporary Egyptian workshops (Hester & Heizer Reference Hester, Heizer, Gould and Schiffer1981). First, the stonecutters shaped a preform from a rough chunk or pebble by hammering and increasingly fine chiselling. Second, the interior was hollowed out using bulbous, jasper drill heads of different diameters and abrasiveness (Ciarla & Bökönyi Reference Ciarla and Bökönyi1985: 420). Third, the vessel walls were thinned by fine shaping with hard chisels and rubbers made of fine-grained stone. In the fourth and final step, the vessels were finished by intensive polishing, and, in some cases, covered with molten wax.
Comparison of some of the Hajjiabad-Varamin stone vessel fragments to material from other sites in the region provides insights into dating and production techniques. Ciarla (Reference Ciarla and Haertel1981: figs 3–5, Reference Ciarla1985: fig. 1) presents a formal classification of approximately 1300 calcite vessel fragments from Shahr-i Sokhta. Notably, this classification does not include the low, carinated forms that are so frequent in the Hajjiabad-Varamin collection. Recent research on the sequence of the Early Bronze Age Sistan region dates the abandonment of Shahr-i Sokhta to c. 2400/2350 cal BC (Kavosh et al. Reference Kavosh, Vidale and Nashli2019). The carinated vessel type, therefore, can probably be ascribed to Akkadian or post-Akkadian times (c. 2300–2100 BC). The same carinated stone vessel form features among the cache of 110 objects of gold, silver, copper, bronze and lapis lazuli from the so-called Vase à la Cachette, an important hoard of valuable objects discovered at Susa and dated to c. 2300 BC (Benoit Reference Benoit, Aruz and Wallenfels2003). Akkadian inscriptions appear on stone vases of various forms (Potts Reference Potts1989), while a carinated bowl made of Waagenophyllum coral limestone bears an inscription of Ur-Bawu, one of the rulers of Lagash in Mesopotamia (Marchesi Reference Marchesi2016: fig. 2). The abundance of carinated vessels at Hajjiabad-Varamin therefore suggests that the workshops were probably active during or after the twenty-fourth/twenty-third century BC. By this date, the regional centre of Konar Sandal South, 5km from Hajjiabad-Varamin, had been abandoned (with a final radiocarbon date of no later than 2400 cal BC; Madjidzadeh & Pittman Reference Madjidzadeh and Pittman2008: 76), so the production may have been controlled by another, currently unidentified centre.
Comparison of the Hajjiabad-Varamin material with the Shahr-i Sokhta assemblage also allows us to recognise evidence of the four manufacturing steps attested at the Sistan workshops. As at Shahr-i Sokhta (Ciarla Reference Ciarla and Haertel1981: 56 & fig. 9), vessel fragments from Hajjiabad-Varamin indicate that a frequent manufacturing mishap was the displacement of the drilling axis from that of the preform (Figure 3j–k). A disc in a yellowish-red, fibrous quartzite with a central indentation (Figure 3l) is unattested elsewhere in the wider region, although it finds a parallel in an object published by Pfälzner & Soleimani (Reference Pfälzner and Soleimani2017: fig. 27, top right) from the same area as Hajjiabad-Varamin. This object could be a tool rather than an unfinished vessel—possibly a drill capstone or socket (Ilan Reference Ilan2016: 4) used to exert pressure on some type of drill. Another convincing parallel for this piece is known from Egypt (Willems et al. Reference Willems2009: fig. 4C).
Other evidence for stone-vessel production includes a few banded lumps with multiple, incomplete drillings made from different directions: these could be training or test pieces (Figure 3m). The interior of some bases preserve unusual bulbs (Figure 3n) and evidence for coarse rotatory marks (Figure 3o). Finally, thick, biconical stone discs with traces of pecking are common finds in the craft-activity area and more widely across Hajjiabad-Varamin. Their function is unknown; some may have been used as flywheels for drills (see Ilan Reference Ilan2016: fig. 5).
Drilling stone vessels: current state of knowledge
While the pre-forming of stone vessels was a painstaking if straightforward step, as noted above, the hollowing out of the vessels’ interiors was the most complex and risky part of the manufacturing process (Figure 3j–k). This hollowing-out was performed with a drill, although there is debate about the process and tools used. So-called ‘twist-reverse-twist drills’ (hereafter TRTD) are frequently depicted in funerary art from Old Kingdom (third-millennium BC) Egypt (Firth & Quibell Reference Firth and Quibell1935–1936: 193; Lucas Reference Lucas1948: 53, 84–87 & 484–87; Stocks Reference Stocks2003: 139–55). Hartenberg and Schmidt (Reference Hartenberg and Schmidt1969) suggest that the TRTD was a type of crank drill with no permanent, vertical axis, used for hollowing out vessels at variable angles. Experimental studies by Stocks (Reference Stocks2003: 148; see also Stocks Reference Stocks1986, Reference Stocks1993), however, have rejected the identification of the tools depicted in Old Kingdom art as TRTD types.
A short summary of the chaîne opératoire for Egyptian stone-vessel production, with a focus on hollowing of the vessels using copper tubular bits, appears in Nicholson & Shaw (Reference Nicholson and Shaw2009: 64–65). In Egypt, copper tubular bits were used for drilling hard stone from the mid fourth millennium BC (Stocks Reference Stocks2003: 12). In the East Mediterranean, systematic use of tubular or core drills for stone-vessel production is well attested at the Minoan and Mycenaean centres of the second millennium BC (see Morero Reference Morero, Poursat and Carter2013, Reference Morero2014, Reference Morero2015). In the Indus Valley, where fine copper drills were used in bead production from the late fourth millennium BC, tubular drills are not known before the Mature Harappan phase (2600–1900 BC) (Kenoyer Reference Kenoyer, Jarrige and Lefévre2005: fig. 6). Boccutti et al. (Reference Boccuti2015) searched for evidence for the use of copper tubular drills in the production of travertine vessels at Shahr-i Sokhta, but the results were inconclusive. It seems, therefore, that copper tubular bits were not a feature of stone-vessel production in the Iranian context.
Stocks (Reference Stocks2003: 128–33) argues that Egyptian stone vessels could have been hollowed using up to three different types of stone drill heads throughout the chaîne opératoire: 1) a crescent-shaped flint or chert bit; 2) a conical or circular bit, with two deep lateral grooves acting as hafting slots to host the wooden fork of a TRTD drill; and/or 3) figure-of-eight, hourglass-shaped points, whose narrow waists would have served the same function. The latter type are:
conical in shape when viewed from the side, round in shape when viewed from the bottom, and figure-of-eight in shape when viewed from above. The rounded part of the tool is the perforating bit. The indentations on the sides of the drill bit are the place where the fork-shaped shaft were [sic]attached and tied. (Malak Eyad Reference Malak Eyad2014: 33)
Because of the presence of lateral slots, types 2 and 3 may be considered variants of the same general type of bit. While conical points were used for drilling bores deeper than their width, the flatter figure-of-eight drill heads were used to make wider cavities, enlarging those previously made with other tools (Stocks Reference Stocks2003: 131–32).
Moorey (Reference Moorey1999: 55) notes that the crescent-shaped drill heads used in Egypt are unknown in Mesopotamia. In the ancient Near East, figure-of-eight drill heads are attested at Neolithic Jarmo, and were widely adopted from the late fourth millennium BC (e.g. at Ur, Uruk and Nineveh) and remained in use until Neo-Babylonian times in the mid-first millennium BC (Moorey Reference Moorey1999: 56).
Stocks (Reference Stocks1993, Reference Stocks2003) also discusses the late fourth-/early third-millennium BC technology of stone-vessel production in Mesopotamia. He considers whether the techniques used were similar to those found in Egypt, comprising copper tubular bits used to make cylindrical cavities, followed by the use of figure-of-eight drill heads to enlarge them. Stocks argues that Mesopotamian stonecutters attached the figure-of-eight drill head to some form of TRTD drill.
The few drill heads so far identified on sites of the eastern Iranian Plateau—at Shahr-i Sokhta, Konar Sandal South (Figure 4b–d) and now, Hajjiabad-Varamin (see Figures 5–10)—have no deep, lateral slots and were probably fixed to the drill shaft in a different manner, so they were not the TRTD type. The only figure-of-eight drill bit from the Iranian Plateau known to the authors (Figure 4a) was found during excavation of a secondary refuse layer rich in artefacts, on the floor of a building at site ABC at Tal-e Malyan (ancient Anshan) in Fars Province, south-western Iran, dating to the Middle Banesh period (Sumner Reference Sumner2003: fig. 42i). A radiocarbon sample from this layer (P-2334) dates to 3350–2920 cal BC (at 95.4% confidence) and 3340–3020 BC (at 68.2% confidence) (Sumner Reference Sumner2003: tab. 13). This figure-of-eight drill head was made of a very fine-grained, light brownish-grey stone, with a triangular section, a functional convex surface with thin striations, and pecked depressions on the other two sides.

Figure 4. Stone vessel drill bits from late fourth- to mid-third-millennium BC sites on the Iranian Plateau: a) Tal-e Malyan (Anshan); b–c) Shahr-i Sokhta; d) Konar Sandal South (scale in cm) (illustrations by M. Vidale).

Figure 5. Lateral view of a possible crescent-like drill bit from Hajjiabad-Varamin. Note the battered edges on the two symmetrical concave sides (scale in cm) (photograph by M. Vidale).

Figure 6. Thick, green chert drill bit from Hajjiabad-Varamin: a–c) lateral views (as if rotated anti-clockwise); d) view from the active end of the tool (photographs by M. Vidale).

Figure 7. Triangular green chert drill bit from Hajjiabad-Varamin. Black dots mark the most intensively worn functional surfaces. a–c) lateral views (as if rotated anti-clockwise); d) view from the active end of the tool (photographs by M. Vidale).

Figure 8. Hajjiabad-Varamin: reddish-grey porphyry artefacts: a) possible drill bit preform; b–c) drill heads with rounded, worn functional ends, marked by black dots. a–c) show lateral views (as if rotated anti-clockwise), with c) showing a fourth view from the active end of the tool (photographs by M. Vidale).

Figure 9. Hajjiabad-Varamin: reddish-grey porphyry drill heads: a) cone-like, highly worn specimen; b) drill head obtained by recycling a broken polished grinding tool. In both cases, lateral rotating views are provided alongside a view of the active end of the tool (photographs by M. Vidale).

Figure 10. Unique drill bit made of red lava from Hajjiabad-Varamin, with a lateral slot for a plug: a) view from the top; b–d) lateral views (as if rotated anti-clockwise); e) view from the active end of the tool (photographs by M. Vidale).
The other known drill heads from the eastern Iranian Plateau come from Shahr-i Sokhta and Konar Sandal South. The tool illustrated in Figure 4b, from Shahr-i Sokhta (Ciarla & Bökönyi Reference Ciarla and Bökönyi1985), was reportedly a surface find recovered along with four similar objects. It has a sub-cylindrical body and a bulbous end, and bears rotation marks. The enlarged head of the tool concentrated pressure and friction at the base of the drilled cavity. In contrast, the tool shown in Figure 4c, also from Shahr-i Sokhta, is made of a fine granite and might have been used for grinding and enlarging the entire inner surface of larger, conical cavities. Lateral slots would make these tools similar to the figure-of-eight drill heads, but slots are not apparent in previously published illustrations. Finally, Figure 4d depicts a double-ended porphyry tool found at the settlement of Konar Sandal South (Rafifar et al. Reference Rafifar, Micheli, Vidale and Madjidzadeh2008), currently radiocarbon-dated to between c. 2800 and 2400 cal BC (Madjidzadeh & Pittman Reference Madjidzadeh and Pittman2008: 76).
This small number of examples represents the sum of our knowledge of stone-vessel production tools from eastern Iran. The 12 examples from Hajjiabad-Varamin therefore add substantially to the regional dataset.
The stone drill heads from Hajjiabad-Varamin
The surface of the production area at Hajjiabad-Varamin is characterised by thousands of broken stone vessels and other waste. Among this material, we report, in detail, on nine of the 12 drill heads so far identified. These are described below, grouped according to lithology.
Chert
1) A crescent-shaped or trapezoidal lithic object measuring 77 × 49 × 27mm and made of a fine-grained, reddish-brown chert, with partial bleaching on its surface (Figure 5). This object has no obvious wear marks, although the two concave sides have been symmetrically battered. Its form closely resembles the lunate examples from Egypt, but its function as a drill bit must remain hypothetical, as this is the only example of this type so far found at the site.
2) A thick, cone-like drill head, measuring 66 × 65 × 42mm, made of a very fine, green chert (Figure 6). The tool was flaked from a pebble, using a process similar to a core preparation sequence. A large portion of the original cortex is visible on two sides. The upper side was also reduced through a crested ridge preparation process. The active, curved part of the point is 19mm deep and 67mm wide. Its surface retains cortex, but the abrading edge of the point seems to have been prepared by light hammering, possibly with a copper tool.
3) A chert tool with cortical patches, indicating that it was obtained from a flat pebble that had been reduced by perimetral flaking to produce its regular, triangular form. If hafted as illustrated in Figure 7a and c, the point could have rotated, so that the two active faces laterally abraded a wider cavity; if hafted differently, with the active ends (emphasised by black dots) in a vertical, axial setting, it could have been used to bore the vessel to a greater depth. Thus, by alternating its hafting, the tool could have been used to hollow out a vessel to different depths and diameters. As with the example illustrated in Figure 6, the continuous active edge (Figure 7d), which is rather worn, was intentionally pecked by light hammering.
Reddish-grey porphyry
Five objects in reddish-grey, coarse-grained rock were identified visually as porphyry (Figures 8 & 9). These represent a possible preform and four drill heads. Figure 8a shows a thick flake (118 × 98 × 59mm), bifacially flaked by heavy blows and rectangular-trapezoidal in section. As the drill heads are made of the same rock and are of comparable size, this bifacial artefact is likely to have been an unfinished point. Figure 8b–c illustrates artefacts used as heavy-duty, rotating drill heads. Figure 8b shows a thick, dihedral flake (91 × 88 × 41mm), whose damaged, rotating end is a rounded, smooth cone, 14mm deep × 41mm wide. Figure 8c shows a thick flake (104 × 76 × 53mm), detached from a larger block or boulder. It has an approximately triangular section and retains cortex on one side. Its main end is rounded by friction, with faint rotation lines. Part of a second, rounded tip is visible on the opposing side, indicating that both ends of the drill were used.
Figure 9a shows a thick flake (76 × 69 × 53mm) with a triangular section. Cortex survives on one side. The tip, which is broken, is a deep cone and displays faint rotation lines. A small, rounded area remains on the opposing side, suggesting that the drill was used from both sides. The conical point is 31mm deep × 24mm wide. Figure 9b illustrates an object, measuring 92 × 83 × 76mm, made by flaking a larger, older tool with heavy blows. It has at least three highly polished surfaces. Three corners seem to have been used as rotating points. The main rotating end is a very shallow cone, measuring 12mm deep and 39mm wide.
Red lava
A distinctive tool, made of red lava (Figure 10). It measures 63 × 45 × 42mm and has a cylindrical, slightly tapered upper hafting section, coming to a smooth, conical point (22mm deep, 36mm in diameter). There is a conical hole in the side of the hafting section, which would have held a removable plug to fix the drill head within a hollow, cylindrical drill shaft. The location of the hole so close to the cutting point suggests that the tool was worn beyond practical use. The cutting point is worn similar to the porphyry drill head (Figure 4d). Carefully shaped by chipping and grinding, it was probably designed for a very specific rotatory function, perhaps to deepen rather than widen cavities. No known parallels for this object have been found in the published literature.
Conclusions
We have presented evidence from the Bronze Age site of Hajjiabad-Varamin, suggesting that the area to the immediate east of the main mound was a craft-production area for the manufacture of stone vessels. We have not yet been able to apply the types of analytical techniques recently deployed, for example, at Shahr-i Sokhta (Boccuti et al. Reference Boccuti2015), and the site awaits a full systematic surface collection. Here, however, we have provided comparisons with other sites across Egypt and Southwest Asia to elucidate the date and organisation of production.
In the absence of use-wear analysis, the brown chert crescent (Figure 5) seems comparable to the crescent drill heads of the Naqada II period (mid fourth millennium BC) found at Hierakonpolis in Egypt (Hikade Reference Hikade, Hendrickx, Friedman, Cialowicz and Chlodnicki2004: 185–87, figs 1.1 & 3–6). Later, in the third millennium BC, parallels exist among chert drill heads from the Old Kingdom workers’ settlement of Heit el-Ghurab at Giza (Malak Eyad Reference Malak Eyad2014: 31–32, images 2.4–2.5). The Hajjiabad-Varamin brown chert crescent also appears similar to the ‘boat-shaped drills’ from Al-Shaykh Sacid-Wadi Zabayda in Egypt, dating to the second-millennium BC New Kingdom (Willems et al. Reference Willems2009: fig. 3B). Stocks (Reference Stocks1993: 598) argues that “crescent-shaped flints … were used exclusively for cutting soft stone, for example, gypsum, without sand abrasive” and were therefore unsuitable for working calcite vessels (Stocks Reference Stocks2003: 139–40). The apparent absence or rarity of this type of drill head in Mesopotamia, combined with its isolated presence in the Halil Rud Valley, is notable. The current scarcity of evidence does not allow us to conclude whether this might be due to a documentary gap or, rather, reflects the type's lack of suitability for the local manufacturing process.
Figure-of eight drill heads seem to be the most common type in both Egypt and Mesopotamia in the late fourth millennium BC. At Ur, Woolley noted:
stone borers for hollowing stone vases … [are] common in the Uruk and Jamdat Nasr periods; the drill-point is a circular stone, flat on the top and curved underneath, and from each side a piece is cut out for attachment; the shaft of the drill would be made of two pieces of wood laid together (or one piece forked at one end … [that] gripped the stone drill head). (Woolley Reference Woolley1956: 14, fig. 5; see also Stocks Reference Stocks1993: fig. 2)
In Egypt, heavy, quartzite figure-of eight drill heads with rotation marks on their abrading surfaces are reported from Hierakonpolis (mid fourth millennium BC) as vessel-making tools (Hikade Reference Hikade, Hendrickx, Friedman, Cialowicz and Chlodnicki2004: 185–87 & figs 1.7–1.9). Other similar drill heads, dating to c. 3000 BC, have been found at Tell el-Farkha and at contemporaneous manufacturing sites (Jórdeczka & Mrozek-Wysocka Reference Jórdeczka, Mrozek-Wysocka, Chłodnicki, Ciałowicz and Mączyńska2012: 289–91 & figs 16–18). By the second millennium BC, the calcite vessel-manufacturing workshop of Al-Shaykh Sacid-Wadi Zabayda in Middle Egypt used an impressive array of different silicified limestone drill heads attested among more than 1000 finds. Classified into five groups (figure-of-eight, boat-shaped, vertically oblong, discoidal with flat underside, and bits with a shallow hollow), these drill heads hint at specialised functions in the local mass-production industry (Ilan Reference Ilan2016: fig. 11; after Willems et al. Reference Willems2009: fig. 3). By contrast, figure-of-eight drill heads have not been recovered at third-millennium BC Hajjiabad-Varamin and they seem to be absent (or unrecognised) at Shahr-i Sokhta.
The technical convergence among drilling equipment in Egypt, Mesopotamia and Tal-i Malyan/Anshan, in Iran, is probably the result of the well-known but poorly understood sphere of exchange and cultural interaction between these regions in the late fourth millennium BC (see, for example, Ward Reference Ward1964; Mark Reference Mark1998; Joffe Reference Joffe2000). In this scenario, the technical/formal convergence of the late fourth millennium BC was followed, in the third and second millennia, by increasing adaptation to local stone varieties for making vessels of new, specific forms.
The diversity of the drill heads found at Hajjiabad-Varamin recalls that of the later, New Kingdom workshop of Al-Shaykh Sacid-Wadi Zabayda (Willems et al. Reference Willems2009). In this latter context, the alternate use and shifting friction planes of the drill heads, alongside the use of copper tools, attests to a completely new, dynamic approach to stone drilling.
In the Halil Rud Valley, different types of drilling tools were also developed and used for distinct steps in the production cycle, perhaps on different types of rocks, and possibly in different periods. Along the Halil Rud Basin, experimentation with lithic technologies, including abrasive tools, was encouraged by the geological diversity of the region (Fouache Reference Fouache2008). Whether this expresses a specific south-eastern Iranian trend is currently unknown and can only be resolved by excavations to recover stratigraphic sequences and archaeometric analyses of lithic objects. Nevertheless, our study shows that the makers of drilling tools in eastern Iran were well aware of the properties of the local resources available for the production of the semi-precious stone vessels that circulated in third-millennium BC Mesopotamia.
Funding statement
This research was supported by the Universities of Jiroft and Padova, and by the International Association for Mediterranean and Oriental Studies, Rome.