Introduction
Inefficient weed control remains a major threat to global food security, as it reduces crop yields due to weed–crop resource competition (Chauhan Reference Chauhan2020). Additionally, it also impacts environmental integrity by altering the structure, function, and diversity of the natural ecosystem (D’Antonio and Meyerson Reference D’Antonio and Meyerson2002). Within Australia, there is heavy reliance on using herbicides as the predominant weed control method (Beckie et al. Reference Beckie, Flower and Ashworth2020). This has been exacerbated by a movement toward conservation cropping that has minimized the use of mechanical weed control methods (Beckie et al. Reference Beckie, Flower and Ashworth2020). Nonselective weed control is utilized at various agronomically relevant stages of broadscale grain and cotton (Gossypium hirsutum L.) cropping, viticulture, annual and perennial horticulture, and other areas such as native vegetation, amenity areas, irrigation or drainage channels, roadsides, and rail corridors (Beckie et al. Reference Beckie, Flower and Ashworth2020). However, its use is threatened by growing herbicide resistance and increasingly negative public perception, which has led to restrictions and bans in multiple countries (e.g., of glyphosate) (Beckie et al. Reference Beckie, Flower and Ashworth2020; Hébert et al. Reference Hébert, Fugère and Gonzalez2019; Mertens et al. Reference Mertens, Höss, Neumann, Afzal and Reichenbecher2018). To address this issue, alternative methods of nonchemical and nonselective weed control are needed in Australia, and in some situations, electric weed control (or electro-weeding) may provide a solution.
Since the 1970s, mechanisms to provide weed control by the passing of electricity through a plant and into the soil have been investigated to prevent weed germination (Sahin and Yalınkılıç Reference Sahin and Yalınkılıç2017; Vigneault et al. Reference Vigneault, Benoit and McLaughlin1990). The concept dates back to the late 1800s, with patents registered as early as 1890 (Sahin and Yalınkılıç Reference Sahin and Yalınkılıç2017; Vigneault and Benoit Reference Vigneault, Benoit, Vincent, Panneton and Fleurat-Lessard2001). This technology offers several benefits, such as reducing herbicide use and chemical residues in the environment, preventing soil erosion risk, and preserving soil structure (Vigneault and Benoit Reference Vigneault, Benoit, Vincent, Panneton and Fleurat-Lessard2001). However, it also has drawbacks, including the potential electric shock and fire hazards and the need for direct contact with the target plants, which requires some crop–weed separation (when not being applied during fallow) (Bauer et al. Reference Bauer, Marx, Bauer, Flury, Ripken and Streit2020; Vigneault et al. Reference Vigneault, Benoit and McLaughlin1990).
Currently, a growing number of these devices are commercially available, mainly in Europe and the United States (Table 1). However, while the principle of electric weed control is not new and this recent machinery development has occurred, it has not gained widespread adoption, and limited scientific analysis of its efficacy has occurred. Further, electric weed control has not yet been certified for use in Australia. Therefore, this review provides a comprehensive review of international literature on the theory of and advances in electric weed control, as well as the potential associated risks. Secondarily, it focuses on potential uses of electric weed control in Australian agriculture, as well as in urban, industrial, and natural environments, and includes an overview of modern machinery and its applications.
Table 1. A comparison of the commercially available electric weed control machinery in the global market.a

a Abbreviations: NA, non-applicable information; PTO, power take-off; HP, horsepower.
b Includes all European countries.
c This application width is mirrored on each side of the machine.
d Includes the countries Brazil, Chile, Nicaragua, Paraguay, and Uruguay.
e Machinery available on farm early 2024.
Theoretical Understanding of Weed Responses to Electric Weed Control
Mode of Action
The technology for electric weed control can deliver the electrical current to plants via two methods: spark-discharge or continuous electrode–plant contact. The spark-discharge method (depicted in Figure 1) transfers a high-voltage current from an energy storage capacitor to electrode(s) that discharge sparks that enter the target plants when they come into close proximity, or contact (Diprose and Benson Reference Diprose and Benson1984; Savchuk and Bayev Reference Savchuk and Bayev1975; Slesarev Reference Slesarev1972; Wilson and Anderson Reference Wilson and Anderson1981). The continuous electrode–plant contact method operates by maintaining physical contact between the machine’s electrode(s) and the plant (as depicted in Figure 2). This creates an electrical circuit by passing the electricity through the plant foliage and stems and into the roots and soil before the current returns to the machine through a ground-contact device (Koch et al. Reference Koch, Hermann, Ergas and Risser2020b; Vigneault and Benoit Reference Vigneault, Benoit, Vincent, Panneton and Fleurat-Lessard2001). Both methods cause nonselective plant damage through a similar mechanism whereby the electric current transforms into heat energy within the plant’s cells, vaporizing water and other volatile liquids (Diprose et al. Reference Diprose, Benson and Hackam1980; Dykes Reference Dykes1977; Mizuno et al. Reference Mizuno, Tenma and Yamano1990). This results in a pressure buildup that ruptures the cells’ membranes in both the roots and foliage, leading to plant death or the suppression of growth (Diprose et al. Reference Diprose, Benson and Hackam1980; Mizuno et al. Reference Mizuno, Tenma and Yamano1990). Little research has occurred to compare these two application methods and evaluate whether they have different efficacies. A preliminary experiment by Lati et al. (Reference Lati, Rosenfeld, David and Becharb2021) found that when applying 0.16 watt-hours (Wh) with prototype spark-discharge and continuous-contact machinery, efficacy was dependent on the application location of the current, rather than the method. It was also dependent on the species of weed treated, for reasons as discussed in the following sections.

Figure 1. Schematic representation of electric weed control technology using the spark-discharge method; produced by Guanhao Cheng from the information presented in Diprose and Benson (Reference Diprose and Benson1984), Savchuk and Bayev (Reference Savchuk and Bayev1975), Slesarev (Reference Slesarev1972), and Wilson and Anderson (Reference Wilson and Anderson1981). The process starts when the plant comes into close proximity to or contact with the electrode (t i). Electricity is then transferred through the plant’s foliage and into the roots before dissipating into the soil. The application is grounded by the ground-contact device (GCD). Each object through which the current passes is depicted as having individual resistance, such as the target vegetation (R v), soil and machinery (R s), or parallel objects (R p). This continues over time until the final point of electrode–plant contact (t f). The efficacy of weed control depends on contact time (t c), which is the duration of the electrode’s contact with the plant. Contact time is determined by the electrode’s effective contact surface and the distance traveled while the electrode is transferring the current to or in contact with the plant (S e).
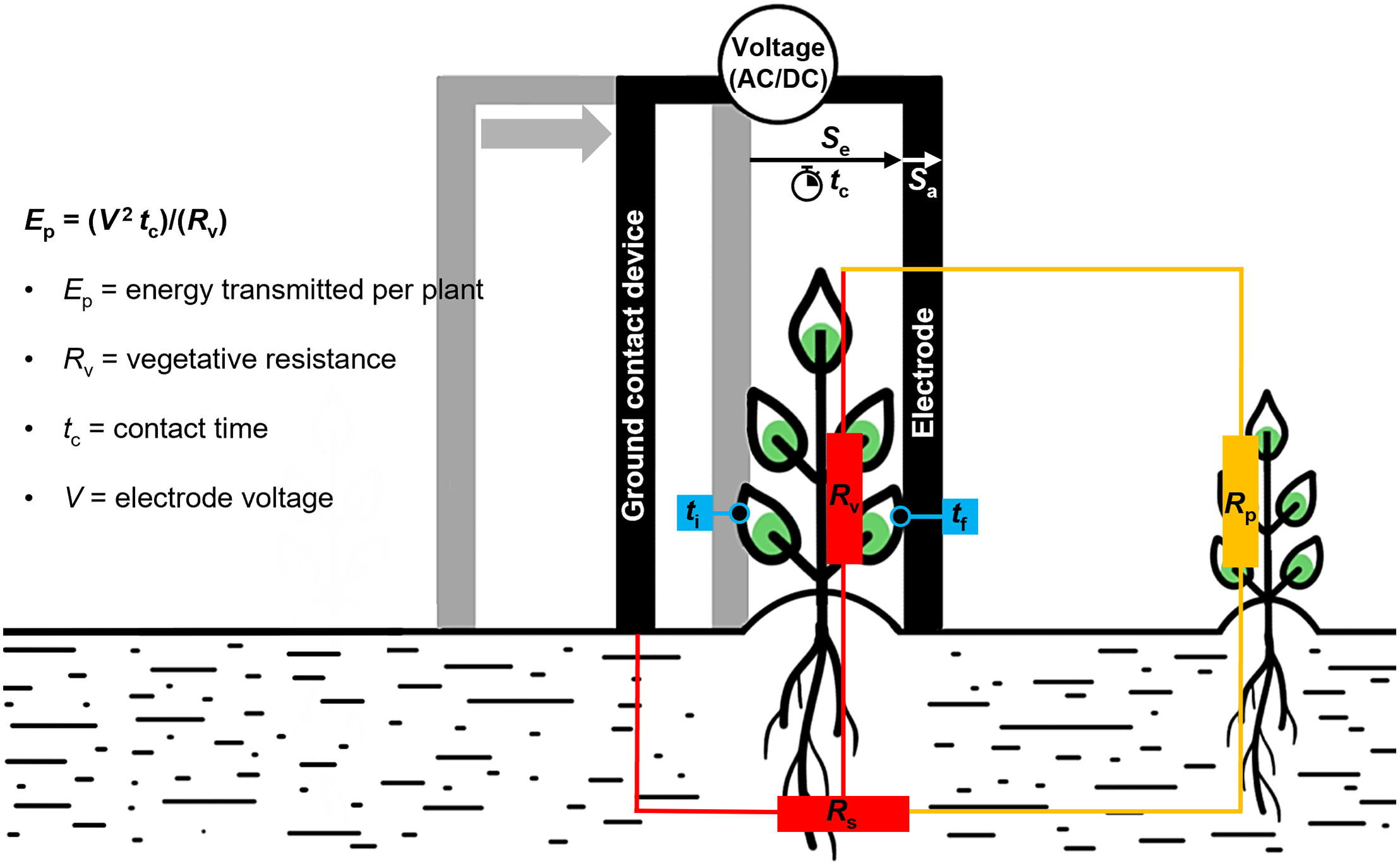
Figure 2. Schematic representation of electric weed control technology using the continuous electrode–plant contact method; produced by Guanhao Cheng and adapted from Vigneault and Benoit (Reference Vigneault, Benoit, Vincent, Panneton and Fleurat-Lessard2001) and Bauer et al. (Reference Bauer, Marx, Bauer, Flury, Ripken and Streit2020). The process starts when the electrode initially contacts the plant (t i). Electricity is then transferred through the plant’s foliage and into the roots and soil before returning to the machine via a ground-contact device, forming a complete electrical circuit. Each object through which the current passes is depicted as having individual resistance, such as the target vegetation (R v), soil and machinery (R s), or parallel objects (R p). The circuit continues over time until the final point of electrode–plant contact (t f). The efficacy of weed control depends on contact time (t c), which is the duration of the electrode’s contact with the plant. Contact time is determined by the electrode’s effective contact surface, the distance traveled while the electrode is in contact with the plant (S e), which will always be greater than the electrode’s actual contact surface (S a).
Factors Affecting Electric Weed Control Efficacy
The amount of energy transmitted to a single plant and the severity of the resulting damage depend on electrode contact time, electrical voltage, and the resistance of the electrical circuit (Vigneault et al. Reference Vigneault, Benoit and McLaughlin1990). The resistance of the total circuit is influenced by various factors, such as the species, morphology, anatomy, and age of the vegetation, as well as the soil conditions, and resistance of the machine and parallel objects, such as other plants (reviewed in Bauer et al. Reference Bauer, Marx, Bauer, Flury, Ripken and Streit2020; Vigneault et al. Reference Vigneault, Benoit and McLaughlin1990). However, many of the factors that affect this resistance have undergone limited scientific analysis, and their impact on the efficacy of electrical weed control measures is unquantified. Furthermore, the interaction between these factors and the application efficacy may not be linear. Although much of this knowledge is theoretical, it is expected that, as with other weed control measures, these factors will vary in Australian systems in comparison to current testing sites, and site-specific adaptions may be required with the integration of the current local weed management knowledge base.
Energy Application and Threshold
The amount of energy needed for electric weed control is determined by the average lethal threshold required per plant to ensure complete death (reviewed in Vigneault and Benoit Reference Vigneault, Benoit, Vincent, Panneton and Fleurat-Lessard2001; Vigneault et al. Reference Vigneault, Benoit and McLaughlin1990). The energy flow will damage cell walls as it travels through the plant, releasing the cell’s contents. As this cellular damage increases, plant resistance decreases, and energy flow increases (Diprose and Benson Reference Diprose and Benson1984; Diprose et al. Reference Diprose, Benson and Hackam1980) (Figure 3). Mizuno et al. (Reference Mizuno, Tenma and Yamano1990, Reference Mizuno, Tenma and Yamano1993) reported that with the destruction of both stem and root cells during the application, plant electrical resistance changed over time as the current flow increased.

Figure 3. Representative diagram of the theoretical relationship between electrical flow and plant electrical resistance (R v) when using electric weed control measures. This diagram is not to scale and was produced by Guanhao Cheng from the information presented in Diprose et al. (Reference Diprose, Benson and Hackam1980) and Diprose and Benson (Reference Diprose and Benson1984).
In theory, when a plant is subjected to a constant voltage, energy flow begins at a slow, linear rate through its tissue (the first stage). This is followed by a plateau that corresponds to the plant’s lethal threshold, where maximum plant damage occurs, and then a faster, exponential flow (the second stage) (Diprose and Benson Reference Diprose and Benson1984; Diprose et al. Reference Diprose, Benson and Hackam1980). Maintaining the current flow past the plateau can cause excessive structural damage within the plant. Parts of the plant may break off, or high levels of cellular damage in specific areas of the plant (localized hotspots) may disrupt the current flow and result in energy wastage (Diprose and Benson Reference Diprose and Benson1984; Diprose et al. Reference Diprose, Benson and Hackam1980). It should be noted, however, that the type of electrode and applicator used during the application can also affect the amount of electrical power transferred into plants, which may have different levels of resistivity.
Growing conditions may also alter the plant’s lethal threshold, with studies establishing that weeds grown in the field are more difficult to control than those grown in a greenhouse (reviewed in Vigneault and Benoit Reference Vigneault, Benoit, Vincent, Panneton and Fleurat-Lessard2001). This was determined by comparing the lethal threshold requirements of sugar beet (Beta vulgaris L.), corn daisy [Chrysanthemum segetum (L.) Fourr.], and charlock mustard (Sinapis arvensis L.) grown in glasshouse conditions (Diprose et al. Reference Diprose, Hackam and Benson1978) with those of sugar beet, velvet leaf (Abutilon theophrasti Medik), field mustard (Brassica campestris L. var. rapa), lambsquarters (Chenopodium album L.), and rough cocklebur (Xanthium strumarium L.) grown in field conditions (Drolet and Rioux Reference Drolet and Rioux1983). The research concluded that such applications may need to be 5- (Diprose and Benson Reference Diprose and Benson1984) to 10-fold greater (Chandler Reference Chandler1978) for field-grown weeds using an experimental continuous plant–electrode contact applicator. Yet understanding of why this relationship occurs is limited, with Diprose and Benson (Reference Diprose and Benson1984) only speculating that the difference in the plant’s physical size may be the cause. However, other factors that could alter efficacy include plant stress, amount of cellular cellulose and lignin (Rankenberg et al. Reference Rankenberg, Geldhof, van Veen, Holsteens, Van de Poel and Sasidharan2021), soil moisture, or root volume. Further, there is little research into the amount of energy required to ensure complete weed population control, and existing research has been conducted on widely divergent machinery, some of which is not commercially available (Coleman et al. Reference Coleman, Stead, Rigter, Xu, Johnson, Brooker, Sukkarieh and Walsh2019; Diprose et al. Reference Diprose, Benson and Hackam1980; Vigneault and Benoit Reference Vigneault, Benoit, Vincent, Panneton and Fleurat-Lessard2001). For example, a recent review included the energy requirements for both the continuous plant–electrode contact and spark-discharge methods, but only referenced studies between 1984 and 2002 in which prototype machinery was used (Coleman et al. Reference Coleman, Stead, Rigter, Xu, Johnson, Brooker, Sukkarieh and Walsh2019).
Electrode Contact Time
Contact time, as described in Figures 1 and 2, must be sufficient to ensure that the amount of energy transferred from the electrode is high enough to reach the plant’s lethal threshold, including in heterogeneous weed populations, where thresholds may vary (Vigneault and Benoit Reference Vigneault, Benoit, Vincent, Panneton and Fleurat-Lessard2001). This can limit the application speed when using a constant voltage (Vigneault and Benoit Reference Vigneault, Benoit, Vincent, Panneton and Fleurat-Lessard2001). For example, in sugar beet crops, control rates as low as 5% of weed beet (sugar beet and annual wild beet [Beta maritima L.] hybrids) and bolting beet (sugar beet bolting after planting due to environmental effects) have been recorded if plant–electrode contact time is insufficient when using experimental spark-discharge applications (Diprose et al. Reference Diprose, Benson and Hackam1980). Further, a recent study by Sahin and Yalınkılıç (Reference Sahin and Yalınkılıç2017) found that under controlled conditions, the mortality of garden cress pepperweed (Lepidium sativum L.) was 52%, 56%, and 61% following 100-V electrical applications with an experimental continuous plant–electrode contact device for 300, 420, or 540 s, respectively. When the application was increased to 200 V, mortality was 79% at 300 s and 90% at both 420 and 540 s (Sahin and Yalınkılıç Reference Sahin and Yalınkılıç2017). Similarly, Lehnhoff et al. (Reference Lehnhoff, Neher, Indacochea and Beck2022) found that when treating tamarisk (Tamarix spp. L.) with experimental continuous plant–electrode contact technology at 2 mA for 0, 12 or 24 h, a reduction of 0%, 37%, and 75% in plant biomass can be seen. After 36 and 48 h, this increased to a 100% reduction. However, it should be noted that while low-voltage applications and long contact times may be useful in urban and industrial settings, they are not practical for large-scale applications, such as in agriculture, and instead illustrate proof of concept.
To ensure lethal dosage, the required contact time also depends on the applied voltage. Specifically, increasing application speed reduces electrode contact time and, thus, energy applied per plant if the application voltage remains constant (Drolet and Rioux Reference Drolet and Rioux1983). Studies have shown that for every doubling of voltage, electrode contact time can decrease by at least 4-fold (Diprose et al. Reference Diprose, Benson and Hackam1980). Diprose et al. (Reference Diprose, Benson and Hackam1980) found that when using an experimental spark-discharge applicator with an average voltage of 3.6 kV, a contact time of 21.8 s was required to achieve 75% control of weed and bolting beets in sugar beet crops. However, when the voltage was approximately doubled to 7.6 kV, the contact time was reduced to 4.3 s while achieving a similar level of control. Similarly, Drolet and Rioux (Reference Drolet and Rioux1983) observed that reduced contact time resulted in a lower percentage of C. album mortality in direct proportion to the energy applied per plant. Yet solely increasing the voltage did not affect mortality in this study, as 100% efficacy was achieved with the initial applications (Drolet and Rioux Reference Drolet and Rioux1983). Similarly, Bloomer et al. (Reference Bloomer, Harrington, Ghanizadeh and James2022) observed increased mortality of Italian ryegrass (Lolium perenne L. ssp. multiflorum [Lam.] Husnot) from 17% to 33% at 15 d after treatment following the increase of an experimental spark-discharge machine from 6 to 10 kV. Chenopodium album was also treated with a 67% to 75% efficacy at 28 d after treatment, but significant differences were not observed between the voltages. Multiple electrical pulses at 6 or 10 kV were also applied to L. perenne, Powell’s amaranth (Amaranthus powellii S. Watson), and black nightshade (Solanum nigrum L.), but no significant differences in efficacy were determined between the voltages (Bloomer et al. Reference Bloomer, Harrington, Ghanizadeh and James2022). These findings may be attributed to the comparably low voltage applied, and it is acknowledged that the surviving individuals did have reduced biomass and, likely, fitness. However, it should be noted that these studies were not undertaken on modern or commercially available machinery (e.g., Table 1); therefore, findings may not be comparable to present-day applications, and further research is required. Applications of lower voltages have decreased electrocution and fire risk and may be more suitable for certain application patterns, such as spot applications or in urban areas (Mizuno et al. Reference Mizuno, Tenma and Yamano1993).
Weed Morphology and Anatomy
The efficacy of electric weed control can also be impacted by the morphology and anatomy of the treated weeds (reviewed by Bauer et al. Reference Bauer, Marx, Bauer, Flury, Ripken and Streit2020; Vigneault and Benoit Reference Vigneault, Benoit, Vincent, Panneton and Fleurat-Lessard2001). Theoretically, the application should be the most effective when the vegetative resistance (R v) of the weed is much smaller than that of the resistance of parallel objects (R p) (Bauer et al. Reference Bauer, Marx, Bauer, Flury, Ripken and Streit2020). This is because the electric current will follow the path of the lowest resistance (Bauer et al. Reference Bauer, Marx, Bauer, Flury, Ripken and Streit2020), potentially reducing the amount of energy applied to the target plant if the resistance of the parallel object is lower.
The morphological factors of the weed, such as its branching patterns, root structure, and cellular characteristics, affect its susceptibility to electric weed control. In theory, multibranched weed species may have a reduced mortality rate, as energy consumption over the total tissue is potentially reduced if only a portion of the plant contacts the electrode and is lethally damaged. Such undamaged tissue can continue to grow and/or resprouting can occur from the undamaged section (Diprose and Benson Reference Diprose and Benson1984; Drolet and Rioux Reference Drolet and Rioux1983). Similarly, extensive spreading or specialized root systems, such as those found in running grasses or species with belowground growth points, can be less susceptible to electric weed control during application, allowing for regrowth (Diprose et al. Reference Diprose, Benson and Hackam1980; Drolet and Rioux Reference Drolet and Rioux1983). Higher cellulose and lignin content in cell walls can increase cell resistance to bursting as the internal liquids are vaporized from the application of current (Vigneault et al. Reference Vigneault, Benoit and McLaughlin1990). This can occur in structures such as the epidermis, making them thicker as well as more pressure and electrically resistant (Bauer et al. Reference Bauer, Marx, Bauer, Flury, Ripken and Streit2020). Theoretical reviews have also suggested that layers of hair, wax, or water on the epidermis may further protect vital plant tissues from an electric voltage (Bauer et al. Reference Bauer, Marx, Bauer, Flury, Ripken and Streit2020).
These factors will vary according to species and age and may result in the need for increased energy levels to reach the lethal threshold (Vigneault et al. Reference Vigneault, Benoit and McLaughlin1990). For example, Lati et al. (Reference Lati, Rosenfeld, David and Becharb2021) treated red clover (Trifolium pratense L.) with experimental continuous-contact machinery at 2, 4, and 6 wk after sowing (WAS). An application of 0.0025 Wh applied at 2 WAS resulted in a >95% biomass reduction compared with the untreated control, but 0.0500 Wh was required to achieve similar results at 4 WAS. Annual ryegrass (Lolium rigidum Gaudin) and black mustard [Brassica nigra (L.) W.D.J. Koch] were not effectively controlled with 0.0025 Wh at 2 WAS, with 15% and 47% biomass reductions compared with the control. At 6 WAS, only ≈30% biomass reduction in T. pratense and L. rigidum could be achieved following applications of 0.0250 and 0.0500 Wh. It should be noted that this study was conducted as a pot trial using experimental machinery. Electrical applications in the field using commercially available machinery may have different outcomes. As the impact of morphological and anatomical factors is mainly theoretical, with little research available to quantify their effect on the lethal dosage of electricity, further research is required to analyze the difference in morphological factors between species and across different growth stages under varying field conditions (e.g., soil and weather). This will reduce the application of excess energy and may make electric weed control more economically viable (Vigneault et al. Reference Vigneault, Benoit and McLaughlin1990). Additionally, research is needed to determine whether repeated electrical applications select morphological traits that enhance the plant’s resistance to electric weed control.
A wide range of problematic weeds in Australian systems have the potential to be effectively controlled by electric weed control; however, no research has yet occurred. For example, brome grass (Bromus diandrus Roth ssp. diandrus or Bromus rigidus Roth ssp. rigidus (Roth) Lainz) is an annual grass with comparably wide (10 mm), hairy leaves and a branching root system usually confined to the top 30 cm of soil and does not develop stolons (runners) (Borger et al. Reference Borger, Torra, Royo-Esnal, Davies, Newcombe and Chauhan2021; Kleemann and Gill Reference Kleemann and Gill2009). These characteristics indicate that it may be effectively controlled by electric weed control measures. However, if the application is insufficient to reach the lethal threshold, plants may recover. Possibly, the leaves’ hairs may also increase plant resistance and the lethal threshold in comparison to smooth-leaved grasses. On the other hand, wild radish (Raphanus raphanistrum L.) is an annual broadleaf that grows from a rosette with a taproot to have an extensively branched shoot system up to 1-m tall (Coleman et al. Reference Coleman, Kristiansen, Sindel and Fyfe2021). Early control within crops may be challenging if sufficient contact is not achieved with the short rosettes. However, effective control could be possible during fallow periods and through crop topping or weed wiping using suitable applicators. To achieve a lethal dose of electricity, mature plants may require high voltage and prolonged contact times due to the plant’s extensive branching and fibrous stems (Preston Reference Preston2019), which would reduce efficiency. Yet the discrete nature of the root will make regrowth unlikely. More research is required to better understand the characteristics of important Australian weed species to optimize electric weed control methods.
Weed Population Structure
High-density weed populations cause an increased load on the electrodes through multiple simultaneous contacts at a constant application voltage (reviewed in Vigneault and Benoit Reference Vigneault, Benoit, Vincent, Panneton and Fleurat-Lessard2001). This results in an increase in the generator’s power requirement in proportion to the number of weeds in contact with the electrode(s) (Vigneault and Benoit Reference Vigneault, Benoit, Vincent, Panneton and Fleurat-Lessard2001). Moreover, in the case of high densities and substantial biomass, a decrease in electrical power per plant may occur, as depicted in Figure 4 (Vigneault and Benoit Reference Vigneault, Benoit, Vincent, Panneton and Fleurat-Lessard2001; Vigneault et al. Reference Vigneault, Benoit and McLaughlin1990). As a result, efficacy may be reduced if the electrical application falls below the lethal threshold (Vigneault and Benoit Reference Vigneault, Benoit, Vincent, Panneton and Fleurat-Lessard2001; Vigneault et al. Reference Vigneault, Benoit and McLaughlin1990). Past research using the Lasco Lightning Weeder (spark–discharge) has indicated that the control rate for bolting beet populations in sugar beet crops was greater than 98% for 100 to 5,000 stems ha−1 (Vigoureux Reference Vigoureux1981). However, when densities were increased to 18,000 stems ha−1, control was reduced to 24% (Vigoureux Reference Vigoureux1981).

Figure 4. Representative diagram of the theoretical distribution of maximum electrical power (E p max) during electric weed control application in a constant application direction under different weed population density scenarios. In the scenario where only one plant (plant one; left) is initially in contact with the electrode(s) (t i), E p max is delivered to the plant until the final point of plant–electrode contact (t f). However, when multiple plant contacts occur (plants one, two, and three; right), E p max is divided among each plant in contact at that time. Note that this diagram is not to scale and was produced by Guanhao Cheng from the information presented in Vigneault and Benoit (Reference Vigneault, Benoit, Vincent, Panneton and Fleurat-Lessard2001).
Additionally, if the weeds are clustered, some plants may be shielded by others that make initial contact with the electrode and may not be effectively controlled (Diprose et al. Reference Diprose, Fletcher, Longden and Champion1985; Drolet and Rioux Reference Drolet and Rioux1983). Taller weeds may also bend when pushed by the electrode, covering and protecting shorter weeds (Vigneault and Benoit Reference Vigneault, Benoit, Vincent, Panneton and Fleurat-Lessard2001; Vigneault et al. Reference Vigneault, Benoit and McLaughlin1990). Research suggests that these shielding effects can be avoided through two applications from opposite directions, leading to a more uniform control rate (Diprose et al. Reference Diprose, Fletcher, Longden and Champion1985; Drolet and Rioux Reference Drolet and Rioux1983). Alternatively, preliminary mowing may be effective to reduce biomass before electric weed control application. Further, effective control of dense weed populations may also need an integrated weed management approach to obtain effective control. It is also possible that the correct selection of a specific machine and/or applicator could also address this issue, but further research is required.
In addition to shielding smaller weeds, taller weeds will also remain in contact with the electrode for a longer period due to bending and will absorb a greater proportion of energy than shorter weeds (reviewed in Vigneault et al. Reference Vigneault, Benoit and McLaughlin1990). Therefore, to ensure control efficacy for smaller weeds, higher-energy applications may be necessary, with electricity applied above the minimum threshold required per plant. This can be achieved by either increasing voltage if sufficient plant–electrode contact is already established or lowering the electrode height if contact is insufficient (Vigneault et al. Reference Vigneault, Benoit and McLaughlin1990). However, it should be noted that any weed control technique is less effective on dense, clumped, or mature vegetation and may require specific adaptation. These issues can be avoided by incorporating electric weed control as part of an integrated weed management plan that aims to maintain weed densities at low, economically acceptable levels.
Soil Conditions
Soil moisture may also have an impact on the efficacy of electric weed control, which may vary depending on the specific application conditions and equipment used. To ensure that the current passes through the plant, into the soil, and to the ground-contact device, a certain level of soil moisture is required to ensure conductivity. Studies have theorized that the damage to the weed’s root system from electric weed control is more severe in dry soil conditions (reviewed in Bauer et al. Reference Bauer, Marx, Bauer, Flury, Ripken and Streit2020; Vigneault and Benoit Reference Vigneault, Benoit, Vincent, Panneton and Fleurat-Lessard2001; Vigneault et al. Reference Vigneault, Benoit and McLaughlin1990). It was reported that the soil’s resistance (R s) increases as the soil’s moisture decreases, making it harder for the electric current to dissipate out of the roots (Bauer et al. Reference Bauer, Marx, Bauer, Flury, Ripken and Streit2020). Therefore, it is possible that in certain field conditions where plants are often moisture stressed, lower-voltage applications than have been currently tested internationally may be required to overcome plant resistance. Further, delaying irrigation before application in relevant situations may assist in achieving optimal weed control.
A study by Vigoureux (Reference Vigoureux1981) using the Lasco Lightning Weeder (spark–discharge) showed that control of weed beet in sugar beet crops ranged from 29% to 67% when electric weed control was applied in moist soil conditions, but increased to 80% to 92% in dry conditions, likely due to the increase in root damage. Similarly, Mizuno et al. (Reference Mizuno, Tenma and Yamano1993) found that when using prototype handheld continuous-contact machinery to apply 200 W to annual bluegrass (Poa annua L.) in winter, withering occurred 4 d later than withering following applications in spring. It should be noted that the exact water content of the soils studied was not specified. Lati et al. (Reference Lati, Rosenfeld, David and Becharb2021) also found that 18% of redroot amaranth (Amaranthus retroflexus L.) biomass was controlled in soils with 15% water content at 3 WAS, compared with only 4% in soils with a 35% water content following the application of 0.0125 Wh with an experimental continuous-contact device.
However, little other research into this effect has occurred, and the responses observed may have been related to plant stress, which can be linked to soil moisture content. Specifically, soil moisture may also influence the moisture content of the plant and the electrical flow through it, if maintained for an extended period. For example, Schreier et al. (Reference Schreier, Bish and Bradley2022) found a significant correlation between increasing plant moisture content and a decreasing level of weed control following electric weed control application on barnyardgrass [Echinochloa crus-galli (L.) P. Beauv.], X. strumarium, annual ragweed (Ambrosia artemisiifolia L.), Japanese bristlegrass (Setaria faberi Herrm.), great ragweed (Ambrosia trifida L.), Canadian horseweed [Conyza canadensis (L.) Cronquist var. canadensis], yellow foxtail [Setaria pumila (Poir.) Roem. & Schult.], and roughfruit amaranth [Amaranthus tuberculatus (Moq.) Sauer] in a soybean [Glycine max (L.) Merr.] crop. Here, the electric weed control treatments were applied with the Weed Zapper™ 6R30 (spark-discharge) at 3.2 or 6.4 km h−1, either singly or twice sequentially (a week apart).
It is also noted that if the growth points of the target plants are not destroyed, sufficient soil moisture may increase the probability of plant regrowth following electric weed control. Further, higher electrical conductivity (EC) may lead to greater dispersion of the current through the soil. Therefore, soils with a higher clay content, which have higher water-holding capacity and EC, may have lower weed mortality rates or require higher voltage due to this dispersion. However, research is required to determine the optimum soil conditions and how they will vary on a site-specific basis.
In Australia, multiple dryland (nonirrigated) agricultural systems frequently experience droughts (ABARES 2021) and often have high sand content (Hall et al. Reference Hall, Davies, Bell and Edwards2020) compared with agronomic systems in parts of the United States or Europe where previous research has been conducted. These soil characteristics can potentially affect the lethal threshold needed for effective electric weed control. As a result, soil resistance will likely be comparatively higher in Australian conditions. However, high-EC (saline) soils also often occur in Australian systems due to the removal of deep-rooted native vegetation (George et al. Reference George, Nulsen, Ferdowsian and Raper1999), and this may affect electric weed control efficacy in such areas, but is yet to be studied. Therefore, more research is required to understand the interactions among EC, moisture content, and salinity for effective electric weed control.
Ecological Impacts of Electric Weed Control
Soil Biota
It has been speculated that the high-voltage current applied during electric weed control may impact soil biota as it travels through the plant’s root system and into the soil. While limited studies have occurred, it can be hypothesized that as the current converts to heat energy and travels effectively through water, it can potentially affect the cell constituents, structure, and viability of these organisms (reviewed in Ruf et al. Reference Ruf, Oluwaroye, Leimbrock and Emmerling2023). Studies on the effect of electrical current applied to microbes have found that the current can have negative effects (Palaniappan et al. Reference Palaniappan, Sastry and Richter1990; Sale and Hamilton Reference Sale and Hamilton1967). Effects are influenced by the voltage and length of the current application and may be altered by the thermal tolerance and moisture content of the soil biota. A recent study by Lati et al. (Reference Lati, Rosenfeld, David and Becharb2021) found that an application of 0.05 Wh with experimental continuous-contact machinery could result in a >40 C increase in the temperature of A. retroflexus, S. nigrum, and johnsongrass [Sorghum halepense (L.) Pers.]. Therefore, it stands to reason that if such large changes are observed in the temperature of the plant shoots, there may be a change in the root and soil temperatures that affects the soil biological population. However, this temperature change will be dependent on the electrode’s effective contact surface in the machinery used, as well as the voltage applied.
Ruf et al. (Reference Ruf, Oluwaroye, Leimbrock and Emmerling2023) found that 2 wk after the use of the Zasso™ XPower with XP300 applicator (continuous contact) at 3 km h−1, there was a reduction in earthworm biomass in the top 25 cm of the soil profile compared with the untreated control (predominately Aporrectodea caliginosa, Aporrectodea rosea, and Lumbricus terrestris). The earthworm community composition and abundance was not reduced following the application of the electric weed control treatment but did after mechanical weed control (chisel plow). At the time of treatment, Ruf et al. (Reference Ruf, Oluwaroye, Leimbrock and Emmerling2023) observed that 15% to 25% of the earthworms in the electric weed control treatment exhibited skin changes, including necrotic tissue and bulging or swollen segments, potentially indicating ruptured cells. This was mainly observed on the larger anecic earthworms, which may explain the observed reduction in earthworm biomass, even though there was no change to abundance. Similar observations of injured earthworms have been made by Schild et al. (Reference Schild, Dierauer and Maurer2017) in the top 30 cm of soil with a notation that the worm’s vitality was significantly reduced a day after the treatment (described by Ruf et al. Reference Ruf, Oluwaroye, Leimbrock and Emmerling2023). Yet it was not specified in either study where the injured earthworms were found in the sampled depth, and it may be expected that if they were on the surface, or in near contact with the electrodes, such injuries may be likely. Ruf et al. (Reference Ruf, Oluwaroye, Leimbrock and Emmerling2023) also observed a significant increase in the labile carbon fraction (0 to 15 cm) at 1 d and 2 wk following the application of electric weed control compared with the control. Increases in microbial biomass carbon and microbial respiration were observed, likely stimulated by the influx of carbon to the soil. Ruf et al. (Reference Ruf, Oluwaroye, Leimbrock and Emmerling2023) concluded that this is likely due to cell damage of living and non-living organic soil constituents, and therefore, the electric weed control application was harming soil biology. However, this assertion may be flawed, as this additional carbon cannot specifically be linked to soil biology. Rather, it could have resulted from the degradation of the weed root and shoot cells following treatment. Schild et al. (Reference Schild, Dierauer and Maurer2017) found no significant differences in microbial biomass carbon or respiration following electric weed control.
If there is an effect on soil biota, there is potential that electric weed control could be used to reduce undesirable organisms within the soil, especially those directly attached to the treated plant’s shoots and roots. Initial studies into microwave technology, which utilizes a similar mode of action, have found impacts on the soil biota (reviewed in Diprose et al. Reference Diprose, Benson and Willis1984). Specifically, 2,450 MHz eliminated the root-knot nematode (Meloidogyne incognita) population following 30 to 300 s of exposure, while 15 s severely reduced activity (O’Bannon and Good Reference O’Bannon and Good1971). Similar findings were reported by Heald et al. (Reference Heald, Menges and Wayland1973) in soil infested with reniform nematodes (Rotylenchulus reniformis). Microwave radiation has been found to be useful in the control of insect pests present aboveground (reviewed in Diprose et al. Reference Diprose, Benson and Willis1984). Applications of 2,450 MHz were able to control powder post beetles and larvae (Lyctinae spp.) in imported hardwoods (Pinus spp. and Abies spp.) when the timber reached 50 C. Lower frequencies (39 MHz) were effective in treating insect pests in stored grain. Therefore, there is the potential for electric weed control to be used in a similar form to control pest species both in and above the soil.
However, other studies on the soil biota following electric weed control applications have shown no negative effects. For example, Koch et al. (Reference Koch, Hermann, Ergas and Risser2020b) analyzed macro- and mesofauna such as earthworms (Lumbricina spp.) and springtails (Collembola spp.) and found that the population densities before and 4 wk after electric weed control treatment with the Zasso™ XPower (continuous contact) with XP300 applicator were comparable or more stable than those following the application of mechanical and chemical weeding techniques. Further studies have determined similar results, with Löbmann et al. (Reference Löbmann, Klauk, Lang, Petgen and Petersen2022) finding no significant differences in Lumbricina spp. populations in the untreated control and following electric weed control at 2 and 4 km h−1 using the Zasso™ XPower (continuous contact) with XPS applicator or mechanical tillage (star hoe and disk harrow) in a viticulture site in Neustadt an der Weinstraße, Germany, during 2020 and 2021. Epigeic arthropod populations (multiple species) were also investigated over 2 yr at another trial site in Bingen, Germany, and similarly, no significant differences were found between the untreated control, electric weed control (at 3 or 6 km h−1), and mechanical tillage (disk harrow) (Löbmann et al. Reference Löbmann, Klauk, Lang, Petgen and Petersen2022).
Due to these conflicting findings, more research is necessary to confirm and quantify these effects. In such research, short-term immediate and long-term effects need to be analyzed, considering site-specific soil and climatic factors, the size, life cycle stage, and position of the biota within the soil, as well as the seasonality of the electric weed control application and the previous weed control measures applied at the site. Further, it should be noted that the removal of weeds by any weed management strategy is known to alter the plant microbiota in the rhizosphere (Trognitz et al. Reference Trognitz, Hackl, Widhalm and Sessitsch2016), which needs to be accounted for.
Seed Effects
The application of electric weed control has been reported to reduce pollen production and seed viability by administering a sublethal dose of electricity, which can be accomplished by increasing application speed or lowering the voltage. In Europe, the application of electric weed control with the Zasso™ XPower with XPU applicator (continuous plant–electrode contact) at 3 km h−1 controlled 90% of A. artemisiifolia per year; the pollen from this plant is a common allergen in Europe, where an estimated 33 million people suffer from pollen allergies (Lake et al. Reference Lake, Jones, Agnew, Goodess, Giorgi, Hamaoui-Laguel, Semenov, Solmon, Storkey, Vautard and Epstein2017; Trognitz et al. Reference Trognitz, Follak, Koch and Sessitsch2020). In a separate study, Schreier et al. (Reference Schreier, Bish and Bradley2022) found that electric weed control reduced weed seed viability by 54% to 80% in E. crus-galli, X. strumarium, A. artemisiifolia, S. faberi, A. trifida, S. pumila, and A. tuberculatus with the Weed Zapper™ 6R30 (spark–discharge), as previously discussed. In this way, electric weed control can help reduce not only allergy symptoms but also agricultural weed seedbanks. However, the timing of such applications must be carefully considered to achieve optimal results. Depending on this timing, these applications can also be used in conjunction with crop desiccation efforts using electric weed control machinery (Table 1); however, the effects on crops have yet to be extensively researched.
In addition to reducing seed and pollen production, electric weed control can also impact the existing soil weed seedbank. While preventing seed germination was an initial use of conducting electricity through the soil (Sahin and Yalınkılıç Reference Sahin and Yalınkılıç2017), it has not yet been explored as a benefit of current technologies. This could be an additional form of weed management attained through electric weed control application, with other thermal weed control technologies such as microwave radiation already advertising it as a benefit (Bauer et al. Reference Bauer, Marx, Bauer, Flury, Ripken and Streit2020; Diprose et al. Reference Diprose, Benson and Willis1984). However, this would likely be affected by the amount of electricity applied as well as the seed’s size, depth, moisture, and level of hard seededness (Diprose et al. Reference Diprose, Benson and Willis1984).
Applicability to Australian Systems
In the 2019 to 2020 financial year, Australian statistics indicate that improved pasture and broadacre crops of predominantly cereal grains, as well as canola (Brassica napus L.), cotton, pulses, sugarcane (Saccharum officinarum L.), and hay/silage, were the most common agricultural land use (ABARES 2021). Other common agricultural uses included fruit, nuts, vegetables, and viticulture (ABARES 2021). Each of these systems presents different challenges for weed management. Weeds are also managed in urban and industrial areas such as roadsides, rail tracks, and drainage areas in Australia. However, to date, there is no research on how electric weed control could be used in Australian systems, and there has been limited international research in these areas. This may be attributed to the reluctance, specifically of farmers, to adopt weed control measures other than chemical use for multiple reasons, including increased management complexity and cost (Moss Reference Moss2019).
However, while land managers may be reluctant to consider integrated weed control options until their benefits far outweigh the implementation cost and extensive trialing has occurred, the widespread development of herbicide resistance and increasing social pressure to reduce chemical use have forced the consideration of such alternatives (Beckie et al. Reference Beckie, Ashworth and Flower2019, Reference Beckie, Flower and Ashworth2020). Furthermore, the total average lost expenditure from weeds in Australian agricultural industries of almost A$5 billion annually highlights the limitations of relying solely on chemicals to control weeds (McLeod Reference McLeod2018). In addition, new herbicides cannot keep pace with the development of resistance (Gaines et al. Reference Gaines, Busi and Kupper2021). As a result, growers have embraced integrated weed management strategies to supplement chemical control (Busi et al. Reference Busi, Beckie, Bates, Boyes, Davey, Haskins, Mock, Newman, Porri and Onofri2021; Llewellyn et al. Reference Llewellyn, Lindner, Pannell and Powles2004, Reference Llewellyn, Ronning, Clarke, Mayfield, Walker and Ouzman2016; Moss Reference Moss2019; Walsh et al. Reference Walsh, Ouzman, Newman, Powles and Llewellyn2017).
Therefore, exploring the applicability of electric weed control to major land uses in Australia is crucial for sustainable weed management. Integrating this new technology will be potentially beneficial, as it provides weed control with minimum soil disturbance and no known reduction in soil health, while also ensuring no chemical contamination of the soil, water, or air. Further, it applies to most areas where weed control occurs, including areas where herbicide use is restricted, such as in organic farming or near waterways. However, the limitations of application speed, labor, and cost still need to be effectively studied for modern machinery (Table 1), as previously discussed.
Fallow Weed Control
Electric weed control, as a nonselective weed control strategy, is most suitable for fallow fields, as well as in non-cropped or urban and industrial areas. For example, Landers et al. (Reference Landers, Challiol, Vilela and Lanz2016) applied electric weed control to weeds for preplant control in organic soybeans in Brazil and Paraguay. They used a prototype continuous plant–electrode contact machine and, at speeds of 16.6 km h−1 (voltage discharge undisclosed), controlled a wide range of weed species. Control after 28 d was lowest for pillpod sandmat [Chamaesyce hirta (L.) Millsp.] at 75%, but between 94% to 100% for common sowthistle (Sonchus oleraceus L.), high mallow (Malva sylvestris L.), common wheat (Triticum aestivum L.), gallant soldier (Galinsoga parviflora Cav.), and Mexican fireplant (Euphorbia heterophylla L.).
The biggest impediment to the adoption of electric weed control in Australian grain cropping is the scale. Electric weed control application speed is comparatively slower than chemical application (Table 1) to ensure that sufficient voltage is applied per plant. In Australia, the average farm size of grain-cropping enterprises is 4,331 ha (ABARES 2021; Llewellyn et al. Reference Llewellyn, Ronning, Clarke, Mayfield, Walker and Ouzman2016). So, weed control at a low speed is not logistically practical. However, utilizing the technology in conjunction with autosteer will optimize application efficiency. Further, there may be scope to combine the technology with fully automated agricultural systems. While, these are a few years away (Machleb et al. Reference Machleb, Peteinatos, Kollenda, Andújar and Gerhards2020), electric weed control in a fallow will be easier to achieve once such a system is available and may reduce operating costs. Blasco et al. (Reference Blasco, Aleixos, Roger, Rabatel and Molto2002) developed a prototype of an autonomous machine and demonstrated its ability to control weeds in lettuce crops (species not defined). In that study, 84% of weeds with fewer than five leaves or less than 20-cm tall (multiple species) were accurately located, and 100% of located weeds were effectively controlled by 4 d after treatment. Commercially available machinery is also currently in development by RootWave™ in conjunction with Small Robot Company: a weed-scouting robot, Tom, and a second electric application robot, Dick (Carrington Reference Carrington2021; RootWave™ 2021c). The two robots communicate through the AI engine Wilma, which plots the determined targets, allowing for effective control (Carrington Reference Carrington2021). Alternatively, in small-scale enterprises such as vegetable farming or viticulture, slower application speeds for nonselective weed control will be more acceptable due to the smaller application areas (ABARES 2021).
Electric weed control may be valuable in organic enterprises, where chemical control is limited (Röös et al. Reference Röös, Mie, Wivstad, Salomon, Johansson, Gunnarsson, Wallenbeck, Hoffmann, Nilsson, Sundberg and Watson2018). Benefits could also be seen in cotton production systems, where irrigation channels are common, and weeds, such as asthmaweed [Conyza bonariensis (L.) Cronquist], are difficult to manage due to widespread resistance and restrictions of herbicide use near waterways (Aves Reference Aves2017; Kennedy et al. Reference Kennedy, Rose, Crossan and Burns2013). Roadsides and railway corridors are common sources of glyphosate resistance and also need to find other nonselective forms of weed control (Richmond Reference Richmond2018). As previously discussed, German trials have found electric weed control to be greater than 90% effective for invasive weed species such as A. artemisiifolia on roadsides with the continuous plant–electrode contact method (Trognitz et al. Reference Trognitz, Follak, Koch and Sessitsch2020), indicating that such applications will also be applicable in Australia.
Fallow applications of electric weed control are also suitable for use in urban and industrial settings in Australia, where the use of herbicides has become controversial due to perceived health risks, especially glyphosate, and local governments and weed management authorities are actively seeking innovative solutions to address the public’s concerns (Environmental Health Directorate 2020). However, the development of applicable electric weed control technology must prioritize the user’s safety and those nearby during operation. Lehnhoff et al. (Reference Lehnhoff, Neher, Indacochea and Beck2022) recently analyzed the suitability of such applications to xeriscaping using an experimental mesh screen over urban groundcover that was consistently exposed to a safe, low-level current of 6 mA for 4 mo (continuous plant–electrode contact). Compared with the untreated control at 64%, this resulted in only 11% coverage of carelessweed (Amaranthus palmeri S. Watson), silverleaf nightshade (Solanum elaeagnifolium Cav.), Indian rushpea [Hoffmannseggia glauca (Ortega) Eifert], field bindweed (Convolvulus arvensis L.), and several lovegrass species (Poa spp.), and 5% coverage when it was used in combination with mulching (Löbmann et al. Reference Löbmann, Klauk, Lang, Petgen and Petersen2022). Spot treatment also offers a promising solution, with the development of such devices occurring through multiple companies (Table 1); however, no trials were found to have occurred with such devices.
Interrow Weed Control
Traditional interrow weed control methods, such as shielded application of chemicals or mechanical cultivation, have drawbacks due to the potential risk of crop damage (Machleb et al. Reference Machleb, Peteinatos, Kollenda, Andújar and Gerhards2020; Osuch et al. Reference Osuch, Przygodziński, Rybacki, Osuch, Kowalik, Piechnik, Przygodziński and Herkowiak2020; Preston Reference Preston2019). Currently, there is no evidence that electric weed control applied to interrow weeds would damage the crop if direct contact between the crop and electrodes was prevented (Lutman Reference Lutman and Walker1980). This can be achieved with the future development of shielded applicators or by ensuring the weeds are spatially separate from the crop during treatment. This can occur through a suggested height differential of between 10 to 20 cm or from the weeds being between the crop rows (Lutman Reference Lutman and Walker1980).
Currently, electric weed control technology offers interrow control in horticulture, as well as in tree and vine crops (Table 1). In horticulture or viticulture, where crop plants are mature with well-established root systems, the potential for yield reduction due to root damage is likely to be even smaller than for annual crops. Postemergent weed control performed by Bongard et al. (Reference Bongard, Haberlah-Korr and Koch2022) in sugar beet crops determined that the double or triple interrow application of electric weed control with the Zasso™ XPower with prototype XPR applicator (continuous plant–electrode contact) was 94% effective at 11 d after treatment in controlling Canada thistle [Cirsium arvense (L.) Scop.], C. arvensis, and C. album in the sugar beet row when used in conjunction with a regionally appropriate banded herbicide regime. Comparatively, 84% efficacy was achieved by the herbicides alone. However, Lehnhoff et al. (Reference Lehnhoff, Neher, Indacochea and Beck2022) determined that prolonged exposure of up to 30 h to low-voltage electrical applications (10 to 250 mA) with experimental continuous plant–electrode contact technology was able to effectively kill white mulberry (Morus alba L.) and Siberian elm (Ulmus pumila L.) trees up to 20 cm in diameter. Further, C. arvensis was controlled from climbing up metal screen–wrapped wooden poles with the constant application of 300 V for approximately 6 wk (Lehnhoff et al. Reference Lehnhoff, Neher, Indacochea and Beck2022). Such applications may be beneficial to remove undesirable vegetation in urban and industrial settings without chemical use (Lehnhoff et al. Reference Lehnhoff, Neher, Indacochea and Beck2022). However, there is no indication that they will be effective for transient interrow electric weed control applications on mature crops as in Bongard et al. (Reference Bongard, Haberlah-Korr and Koch2022).
There may also be potential for developing large-scale electric weed control units to target interrow weeds in grain-cropping and horticultural systems, and the market is still waiting on the release of such a device that can cover large areas at a reasonable speed. Brighenti and Brighenti (Reference Brighenti and Brighenti2009) investigated such interrow weed control in soybean, using a prototype continuous plant–electrode contact machine at 4,400 or 6,800 V in each of the two experiments. At 4 km h−1, 90% to 100% of E. heterophylla, morningglory (Ipomoea spp.), fanpetals (Sida spp.), plantain signalgrass [Urochloa plantaginea (Link) R. Webster or Brachiaria plantaginea (Link) R. Webster], and crabgrass (Digitaria spp.) were controlled. Building on this study, Landers et al. (Reference Landers, Challiol, Vilela and Lanz2016) used a prototype continuous plant–electrode contact machine at 6,000 V and found that 28 d following treatment at speeds of 3.4, 9.5, and 16.6 km h−1, an average control rate of 77% was achieved for weeds taller than 5 cm with no significant differences between the speeds of application. At 16.6 km h−1, 100% of C. bonariensis, slender amaranth (Amaranthus viridis L.), lilac tasselflower [Emilia sonchifolia (L.) DC.], tropical white weed (Ageratum conyzoides L.), stinking chamomile (Anthemis cotula L.), high mallow (Malva sylvestris L.), hairy beggarticks (Bidens pilosa L.), tropical Mexican clover (Richardia brasiliensis Gomes), Phyllanthus acutifolius Poir ex Spreng., and S. oleraceus were controlled (Landers et al. Reference Landers, Challiol, Vilela and Lanz2016). However, electric weed control may also have a use in broadscale agricultural systems on the tramlines in controlled traffic farming (Tullberg et al. Reference Tullberg, Yule and McGarry2007). These tramlines are a small proportion of the field and are often used in conjunction with chaff lining, so it would be easier to treat these selected areas. Alternatively, combining electric weed control with weed detection technology, such as the previously discussed RootWave™ technology, may allow increased travel speed as a smaller proportion of the field is targeted (Nicholas et al. Reference Nicholas, Jennifer and Judit2021). This is because these areas are consistent, potentially making it easier to link electric weed control devices to autosteer and automated technology. Specifically, Nørremark et al. (Reference Nørremark, Sørensen and Jørgensen2006) identified electric weed control as a tool with the potential to operate in the interrow space and close to crop plants while attached to an autonomous vehicle. Similarly, its use along fire breaks and fence lines may be applicable. However, out of the technologies reviewed, this study did not find that electric weed control was the preferred method of weed management for sugar beet crops. Yet it should be noted that Nørremark et al. (Reference Nørremark, Sørensen and Jørgensen2006) did not compare modern commercially available machinery (Table 1), but rather a prototype charged water sprayer (14 kV), and utilized historical efficacy data.
In a mature crop, growth suppression, combined with the competitive ability of the crop, may be sufficient to maintain crop yield potential, making it unnecessary to completely kill interrow weeds. In current agricultural systems, many herbicides suppress rather than kill weeds outright, for example, B. diandrus (Borger et al. Reference Borger, Torra, Royo-Esnal, Davies, Newcombe and Chauhan2021). If weed suppression rather than total mortality is the goal of electric weed control, this would allow greater application speeds (reducing application voltage via reduced contact time) and reduced cost of application. Additionally, some agricultural systems may prefer to retain some ground cover, particularly tree horticulture or viticulture systems (Abad et al. Reference Abad, Hermoso de Mendoza, Marín, Orcaray and Santesteban2021; Bartel et al. Reference Bartel, Archontoulis, Lenssen, Moore, Huber, Laird, Fei and Dixon2019), as it can have environmental benefits related to erosion, water infiltration, soil aggregate stability, nitrogen leaching, carbon sequestration, gas emissions, and biodiversity (Abad et al. Reference Abad, Hermoso de Mendoza, Marín, Orcaray and Santesteban2021; Bartel et al. Reference Bartel, Archontoulis, Lenssen, Moore, Huber, Laird, Fei and Dixon2019).
Crop Topping or Weed Wiping
Crop topping is a common practice in Australian grain cropping that involves applying a low rate of nonselective herbicide before crop maturity to reduce seed production in mature weeds such as R. raphanistrum and L. rigidum (Gill and Holmes Reference Gill and Holmes1997; Walsh and Powles Reference Walsh and Powles2009). However, early herbicide application can result in a greater loss of crop yield (Gill and Holmes Reference Gill and Holmes1997; Walsh and Powles Reference Walsh and Powles2009). Weed wiping, a technique in which herbicide is physically wiped over weeds that are taller than the crop, is also used for reducing weed seed production, but it has variable efficacy and can result in inadvertent herbicide contact and crop damage (Harrington and Ghanizadeh Reference Harrington and Ghanizadeh2017). Electric weed control offers an alternative approach to crop topping or weed wiping where the weeds are taller than the desired vegetation (Table 1). Such applications may not only be suitable to use in agricultural settings to remove weeds that emerge above crops and pastures but also in urban areas such as parklands. Diprose et al. (Reference Diprose, Benson and Hackam1980) used electric weed control in a sugar beet crop, at 8 to 15 cm above the crop, to target weed beet and bolting beet. They employed an experimental spark-discharge tractor-driven system that produced 7.6 kV, traveled at 1.6 km h−1, and targeted a six-row-wide area. This approach prevented seed set in 75% of the target weeds without any observable damage to the crop plants that were not in electrode contact (Diprose et al. Reference Diprose, Benson and Hackam1980). However, there was no indication of how the yield was assessed, and the trial was not replicated.
Further, similar applications could be exploited for crop desiccation and field fodder conversion; while machinery is being developed for this use (Table 1), limited studies have occurred into its efficacy or its effect on the crop. A preliminary 2020 field trial by Klauk et al. (Reference Klauk, Löbmann and Petersen2022) found that when using the Zasso™ XPower with XP300 applicator, desiccation of 100% of early potatoes (Solanum tuberosum L.) could be achieved at speeds of 1, 3, and 6 km h−1. However, a second trial in 2021 with suboptimal application conditions, including wet weather and better-established potato canopy, reduced efficacy to 80% to 90%. The perennial weeds C. arvense and quackgrass [Elymus repens (L.) Gould] were also effectively controlled (85% to 100%) in both trials regardless of the speed of application but were found to resprout approximately 4 wk later (Klauk et al. Reference Klauk, Löbmann and Petersen2022). No analysis was made concerning whether there was any change in the quality of the potato crop following the applications. Ruf et al. (Reference Ruf, Oluwaroye, Leimbrock and Emmerling2023) also assessed field fodder conversion methods. They found that using electricity applied with the Zasso™ XPower with XP300 applicator (continuous contact) at 3 km h−1 had a lower efficacy than chemical (glyphosate) and mechanical measures (chisel plow) at 7 mo after treatment. However, this assessment of efficacy was not the aim of the study and therefore relies on a single visual assessment of the site. More research is required to determine the impact of an electrical voltage applied to different weed species at varying stages of maturity and seed production and the potential impact on crop yield.
Potential Application Issues
Resistance
Herbicide resistance is driving the search for the development of alternative weed control methods such as electric weed control (Beckie et al. Reference Beckie, Flower and Ashworth2020; Somerville et al. Reference Somerville, Powles, Walsh and Renton2017). However, there may also be a risk of resistance to electric weed control developing, especially if it is used repeatedly (as for some herbicides) and not as part of an integrated management plan. There is currently no research to investigate resistance to electric weed control following early- or late-season application or whether cross-resistance between management practices may occur. Yet it should be noted that resistance to physical weed control methods has rarely been observed. For example, harvest weed seed control (HWSC) measures, including chaff tramlining, chaff lining, and impact mills, have been adopted by 75% of Australian grain growers (Walsh and Powles Reference Walsh and Powles2022). Despite HWSC’s extensive use for >20 yr for species such as L. rigidum, no evidence of adaptation has been found (Walsh and Powles Reference Walsh and Powles2022).
However, as discussed earlier, the success of electric weed control is influenced by a range of morphological and physiological traits, including height, branching, cellulose, and lignin. If electric weed control is used repeatedly, it is possible that weeds could evolve to have a shorter growth habit (Diprose et al. Reference Diprose, Benson and Hackam1980), which will increase the chances of weed survival. In Diprose et al. (Reference Diprose, Benson and Hackam1980), 25% of weeds survived to produce seed after electrocution, including those with multiple branches where not all branches had contact with the electrode or those weeds that were too short for contact with the electrodes set at 8 to 15 cm above the crop. In a study by Ashworth et al. (Reference Ashworth, Walsh, Flower, Vila-Aiub and Powles2015), R. raphanistrum was found to be able to produce new biotypes within 5 yr with earlier flowering times but less competitive growth habits, such as reduced height and biomass, indicating that similar effects could occur following evolutionary stimuli such as the repeated application of herbicides and HWSC techniques (Ashworth et al. Reference Ashworth, Walsh, Flower, Vila-Aiub and Powles2015; Shergill et al. Reference Shergill, Schwartz-Lazaro, Leon, Ackroyd, Flessner, Bagavathiannan, Everman, Norsworthy, VanGessel and Mirsky2020). Therefore, repeated application of electric weed control could result in a similar response with shorter plants or increased branching, but the development of such less-competitive traits could be beneficial when weeds occur within crops. Weeds may also develop differences in cellular cellulose and lignin contents or other characteristics that influence electric weed control as detailed previously, given sufficient selection pressure.
However, as electric weed control acts on phenotypes that can be coded for by multiple gene combinations, it is less likely to select resistant genes. Additionally, its application can also be modified by timing, voltage, speed, and applicator type to create an effect similar to the application of several herbicides with different modes of action. Specifically, the voltage can be increased and/or application speed decreased to increase the amount of electricity transferred to each plant. Applicators can also be adapted to function at a greater or lesser height above the ground or by increasing the electrode’s effective contact surface to target shorter or taller weeds and instances of greater branching. For example, Lati et al. (Reference Lati, Rosenfeld, David and Becharb2021) found that with applications by either spark-discharge or continuous contact (prototype machinery), greater efficacy was achieved when the current (0.16 Wh) was applied to the youngest fully emerged leaf, rather than the middle part of the plant stem. Therefore, while electric weed control represents a possible solution for current herbicide-resistance issues, research is required to determine the ability of weeds to adapt to its potential uses. Furthermore, like any weed management technique, electric weed control will need to be incorporated into an integrated weed management program to reduce the potential for resistance development.
Physical Impediments
Australian systems may also have physical impediments to electric weed control, including irrigation ditches, irrigation pipes, wire fences or trellis, or debris like old wires or metal tools on the ground. These physical objects can limit application efficacy by conducting the current away from the target plant and reducing the electrical dosage. Moreover, during the application, there are safety risks if the electric current is directed to non-target areas. For instance, crops such as cotton, rice, fruit and nut trees, and vegetables, which are frequently irrigated using varying systems (ABARES 2021) may pose impediments. However, such systems are often well-earthed in case of lightning, which could limit potential risks.
In some systems, wire trellises are used to support plants, such as in urban gardenscapes or in viticulture and horticulture, and wire fences are used to separate paddocks or contain livestock, which may make it impractical to apply electric weed control around them. Such wire fences have also become increasingly unmaintained in the Australian landscape, due to less diversity in industrial broadscale grain-cropping and livestock systems (Beckie et al. Reference Beckie, Flower and Ashworth2020). Therefore, physical impediments such as scrap metal debris or superfluous wire fences, which may occur in such systems, must be removed if electric weed control is to become a common practice in the industry. However, if it is to be integrated into urban areas and industrial agricultural systems in the future, optimal plant support structures and irrigation systems will need to be developed to ensure the safe application of electric weed control as well as optimal crop growth.
Fire Risk
The conservation cropping system is common to Australian broadscale grain industries, with residue and/or mulch also frequently maintained in horticultural and viticultural systems (DeVetter et al. Reference DeVetter, Dilley and Nonnecke2015; Llewellyn et al. Reference Llewellyn, D’Emden and Kuehne2012). In some urban and industrial settings, there can also be high levels of surface plant residue. At specific locations in the grain-cropping system, such as Wongan Hills and Cunderdin in Western Australia, the maximum dry crop residue in the winter cropping season was found to be 1,910 and 4,480 kg ha−1 (Borger et al. Reference Borger, Riethmuller, Ashworth, Minkey and Hashem2015). However, while retaining residue offers several environmental benefits, it also poses a fire risk, particularly during times of high fire danger ratings, which are regularly reported by the Bureau of Meteorology (2021).
In spring and summer, agricultural communities throughout Australia are commonly advised of a “harvest ban” or “vehicle movement ban” in locations where the fire risk is too high. During such periods, electric weed control can pose an active fire risk during application, because the electrical current can “arc” between the target plant and the electrode. However, this potential fire risk will vary broadly, mainly depending on the machinery and time of year. The fire risk is generally low to moderate during the winter growing season, but the application of electric weed control over the summer fallow may not be safe or practical. Further research is required to determine the fire risk associated with different electric weed control machinery and to optimize the technology to minimize this risk (e.g., adjusted voltages, altered applicators, and improved arc control).
The Electric Weed Control Market
Patents for electric weed control have been issued since the 1890s, but it has historically been viewed as less cost-effective, more energy-intensive, and less efficient than conventional chemical or mechanical methods, regardless of the environmental benefits (reviewed in Vigneault et al. Reference Vigneault, Benoit and McLaughlin1990). Despite these drawbacks, there has been a recent resurgence of investment in the development of electric weed control machinery, as shown in Table 1. This review does not aim to provide a comprehensive evaluation of the commercially available machinery, as there is insufficient literature available and a lack of published data on economic analysis, such as machinery depreciation or servicing schedules. However, following the purchase of the machinery, the main application cost associated with electric weed control is generator fuel, which fluctuates with market price, weed density, species, and growth stage as well as the area covered. Future fuel costs may be reduced by using electric vehicles powered by renewable energy in conjunction with this technology. It is also noted that this article focuses on key machinery examples that may be relevant for agriculture or urban weed management in Australia, rather than providing an exhaustive review of all available products.
The Lightning Weeder
Lasco Inc. has developed the Lightning Weeder (Figure 5), a commercial tractor-mounted electric weed control unit that is currently being used in the U.S. Midwest to target tall weeds with the electrodes positioned slightly above the crop (Bennett Reference Bennett2019; Vigneault et al. Reference Vigneault, Benoit and McLaughlin1990). These machines can be utilized as either front-mounted or pull-behind units (Bennett Reference Bennett2019). The efficacy of the machine has been demonstrated in 10 sugar beet field trials at 4.7 km h−1 using 50 kW (Kaufman and Schaffner Reference Kaufman and Schaffner1982). These trials revealed that the cost of using Lightning Weeder on a 210-ha basis per year was equivalent to the average application cost of glyphosate (Roundup®, rate undisclosed, Bayer, Leverkusen, Germany 51373) when using a roller (Roll-Wipe, Irrigation Specialties Manufacturing, Scottsbluff, NE, USA 69631) and a recirculating sprayer (Spray Sickle, Sprayrite Manufacturing, West Helena, AR, USA 72390) (Kaufman and Schaffner Reference Kaufman and Schaffner1982).
Hackam (Reference Hackam1985) attempted to modify the Lightning Weeder to target smaller weeds while protecting the crop using a series of short electrodes positioned near the ground, as well as shields and deflectors. Although this modified system was partially successful in controlling weeds, it failed to work effectively at high densities due to excessive power consumption and mechanical failure (Hackam Reference Hackam1985). After this venture, no further scientific trials were found to have been conducted using this machine.
The Weed Zapper™
The Weed Zapper™, an electric weed control machine manufactured by Old School Manufacturing (Figure 6) is available in four tractor models known as the Annihilator Series and three self-propelled models called the Terminator Series. They comprise a front-mounted flexible boom with horizontal copper electrodes powered by a rear-mounted power take-off (PTO)-driven generator (Ruen Reference Ruen2018; Weed Zapper Reference Zapper2021a, Reference Zapper2021b). However, as each unit is built to order, modifications can be made to convert to a rear-mounted boom, add trailer tow packages, or switch to wide-row configurations (Ruen Reference Ruen2018). The booms also fold for transportation (Ruen Reference Ruen2018). The efficacy of the Weed Zapper™ 6R30 unit was recently studied in a soybean crop by Schreier et al. (Reference Schreier, Bish and Bradley2022), as previously discussed.

Figure 6. The Weed Zapper™ electric weed control machine, produced by Old School Manufacturing (Table 1). The image includes the Annihilator Tractor Series (right, 12R30 model) and the Terminator Self-Propelled Series (left, T3 model), each fitted with flexible front applicator booms of 9.1 and 18.3 m (30 and 60 feet), respectively. The image is sourced from B. Kroeger and N. Kroeger (personal communication, March 25, 2022).
NUCROP
The German company crop.zone and the Australian-based company Nufarm have collaborated to build a hybrid-electric weed control solution commercialized under the name NUCROP, which is shown in Figure 7 (Claver Reference Claver2021a, Reference Claver2021b; crop.zone 2021). This machine consists of a sprayer front that coats the plants with an organic, conductive liquid pretreatment (Volt.fuel), claimed to enhance EC (Claver Reference Claver2021a, Reference Claver2021b). The 12-m-long electric applicator boom (Volt.apply PDM12) at the back of the tractor then applies an electric charge to the weeds (Claver Reference Claver2021a, Reference Claver2021b).

Figure 7. crop.zone and Nufarm’s electrochemical weeding machine, NUCROP (Table 1). Image sourced from D. Vandenhirtz (personal communication, September 10, 2021).
XPower
ZassoTM, in collaboration with Case New Holland Industrial and other companies, has developed electric weed control machinery marketed as the XPower, which utilizes a power unit mounted on the rear of the tractor that runs off the PTO shaft. The XPower can be used with a variety of applicator units that contain flexible metal electrodes that can adapt to the application surface, such as the XPS, XPU, and XP300 described below (Ergas Reference Ergas2020a; Zasso Group AG 2020).
The XPS applicator (Figure 8), designed for weed control under vines and trees, uses two static electrodes to eliminate weeds and an additional electrode that swings on passive rotary axes to treat weeds under the crop and around the stems while preserving crop stem integrity (Zasso Group AG 2021i). Preliminary studies with the XPS conducted by Zasso in conjunction with the French Vine and Wine Institute showed that, at an application speed of 3.5 km h−1, an average of 70% of the weeds were controlled in a Lisle-sur-Tarn vineyard with clay-silt soils following three applications (Vitisphere 2020). Subsequent studies in collaboration with the German Institute for Wine and Oenology used the machine at 4 km h−1, resulting in a decrease of 5% to 67% in the number of species present across three field sites (Lang et al. Reference Lang, Kurz, Löbmann, Klauk, Petersen and Petgen2022). However, it should be noted that efficacy was not consistent across all species, and reduced efficacy was observed in both studies for species with higher levels of root and shoot branching or older individuals that tended to have high biomass and cellulose/lignin content. Further, efficacy was also influenced by the environmental conditions at the time of application (Lang et al. Reference Lang, Kurz, Löbmann, Klauk, Petersen and Petgen2022; Vitisphere 2020).
The XPU applicator (Figure 9), designed to control weeds in urban areas, can be shifted sideways up to 0.5 m to avoid spatial constraints (Zasso Group AG 2021g). A recent study in Burgenland, Austria, compared seven weed control methods and found that the XPU was greater than 90% effective in controlling weeds and preventing pollen production, particularly in A. artemisiifolia and Japanese knotweed (Fallopia spp.) (Ergas Reference Ergas2020b). However, resprouting of the rhizomes was noted in Fallopia (Ergas Reference Ergas2020b).
The XP300 is another applicator developed by Zasso™ for agricultural area applications (Figure 10) (Zasso Group AG 2021a). When operating at 72 kW and 3 and 5 km h−1 speeds, the XP300 was found to be more effective than glyphosate and mechanical weeding (harrowing) for controlling populations predominately dominated by volunteer grain (cereal, canola, and greening crop remnants) and dicotyledonous species (C. album, fool’s parsley [Aethusa cynapium L.], catchweed bedstraw [Galium aparine L.], and black bindweed ]Polygonum convolvulus L. var. convolvulus]) in sugar beet crops (Koch et al. Reference Koch, Hermann, Ergas and Risser2020a). Control plots, where no weed control methods were applied, showed an average weed density of 54 to 97 plants 10 m−2 (Koch et al. Reference Koch, Hermann, Ergas and Risser2020a). However, the effectiveness of using the XP300 as the primary control method was limited when dealing with high weed densities characterized by high lignin content and multiple branching, as this resulted in shielding, which impeded electrode contact (Koch et al. Reference Koch, Hermann, Ergas and Risser2020a, Reference Koch, Hermann, Ergas and Risser2020b).
Zasso™ has also several applicators and smaller-scale machinery options available in Central and South America, as outlined in Table 1, which no studies were found to have analyzed their effectiveness. An XPR applicator for use in horticultural row crops and the XPN, a tractor-less machine for use in narrow-row vineyards, are also in development (New Holland Agriculture 2022; Zasso Group AG 2021e).
RootWave™
RootWave™ is an electronics company that has been developing weed control alternatives since 2012 (RootWave™ 2020, 2021a). The company has designed the RootWave™ Pro (Figure 11; Table 1), a handheld weeder designed for small-scale spot applications. It runs on a generator with a compact design to ensure mobility in small utility vehicles and has variable levels of power application (RootWave™ 2021b). The unique patented spectrum of electrical applications used by RootWave™ may be safer for operators and bystanders, as the current can pass through the body without causing damage (Diprose Reference Diprose2016).

Figure 11. The RootWave™ handheld electric weeder, the RootWave™ Pro (Table 1). Image sourced from T. Archer (personal communication, April 2, 2022).
The company has also adapted its technology for vineyards and orchards with the RootWave™ Top Fruit (Figure 12; Table 1), but no research with this machinery has been done. Further adaptations for different agronomic situations may also occur, such as a tractor-mounted weeding unit for row crops and a fully autonomous weeding robot for use in arable cereal crops, as previously discussed (Bennett Reference Bennett2019; RootWave™ 2019, 2021c, 2021d).
Conclusions
Electric weed control is a promising technology with the potential to revolutionize weed management in urban, industrial, and agricultural areas. This review highlights the potential for electric weed control globally and, specifically, how current and potential applications can fit into Australian systems. An increasing number of private companies are investing in the development of electric weed control machines and will continue to investigate optimal machine operation, driven by industry requests for machines that are larger, faster, autonomous, and applicable to a wide range of enterprises. However, there is a significant gap in our knowledge of the technology’s efficiency, and as this review highlights, much of the “existing knowledge” is entirely theoretical or stated with promotional intent. While hypothetical knowledge cannot be subject to critical review, where experimental studies are available, this review has considered how the work will apply in the broader context and has highlighted possible limitations. However, to support industry development, further research is needed on aspects of weed biology and ecology and environmental characteristics possibly affecting electric weed control efficiency, including the impact of:
-
Species-specific plant morphological and anatomical traits, including height, branching, root structure, and leaf covering or other features, as well as cellulose and lignin content.
-
Population structure, such as plant density, cohort structure, size, and age.
-
Soil characteristics, including moisture, texture, EC, and salinity.
-
Electric current on the different stages of plant development, including the seedbank, emerging seedlings, mature plants, and plants at the reproductive stage (pollen and seed production).
-
Survival, resprouting, and growth patterns of any plants not fully controlled by electric current.
Electric weed control is also likely applicable to many of the major land uses in Australia where weed control occurs and may be crucial for ensuring sustainable management. Relevant application techniques may be during fallow periods, between the rows of crops, and through crop topping or weed wiping. Integrating this new technology will potentially provide the benefits of minimum soil disturbance while also ensuring no chemical contamination of the soil, water, or air. However, there is also a need for research on critical factors that can significantly affect the efficacy of electric weed control, especially in Australia. These factors include the optimal application speed, contact time, and voltage under site-specific conditions. Further, analysis of the degree of physical separation between the crop, or desirable vegetation, and the weeds is also required. It is also critical to investigate the effect of application at various stages of crop and weed growth, as well as of weed–crop competition interaction following applications. The potential for resistance development, fire risk and potential prevention strategies, and economic value should also all be analyzed. In completing this research, a standardized testing protocol should be established to assist with the technological evaluation of applicability and efficacy while considering site-specific soil and climatic factors, as well as the location’s weed control history. Comprehensive information from such research will help us understand the influence of these variables and can improve the sustainability and effectiveness of this technology and promote its responsible use in weed management practices.
A final goal of research on electric weed control will be to develop integrated weed management programs that can optimize weed control while ensuring responsible use of the new technology. While electric weed control has the potential to be an effective and sustainable tool in weed management, it is important to consider it as part of a broader approach that includes a variety of weed control techniques. By integrating electric weed control with other control techniques, we can achieve better weed control outcomes while minimizing the risks of overreliance on any single weed control option. With further research and development, electric weed control can be a valuable addition to integrated weed management programs in Australia, providing farmers and land managers with a range of options for effective and sustainable weed control.
Acknowledgements
The Department of Primary Industries and Regional Development’s (DPIRD) project on electric weed control in Australia has been made possible through collaboration with AGXTEND, a brand of CNH Industrial, and their partnership with Zasso™. It is also supported by funding from the Grains Research and Development Corporation, Wine Australia, and the Cotton Research and Development Corporation and in-kind support from AHA Viticulture and the Western Australian Local Government Association. We want to thank our DPIRD colleagues, Arslan Peerzada, Glen Riethmuller, and Bowen Zhang, as well as Melanie Davies (WALGA) for their comments on this review. We also want to thank the companies Old School Manufacturing, Nufarm and crop.zone, Zasso™, and RootWave™, who responded to our correspondence for information on their machinery; their insights were integral.
Maximilian Koch was an employee of Zasso™. The remaining authors have no conflicts of interest to declare.